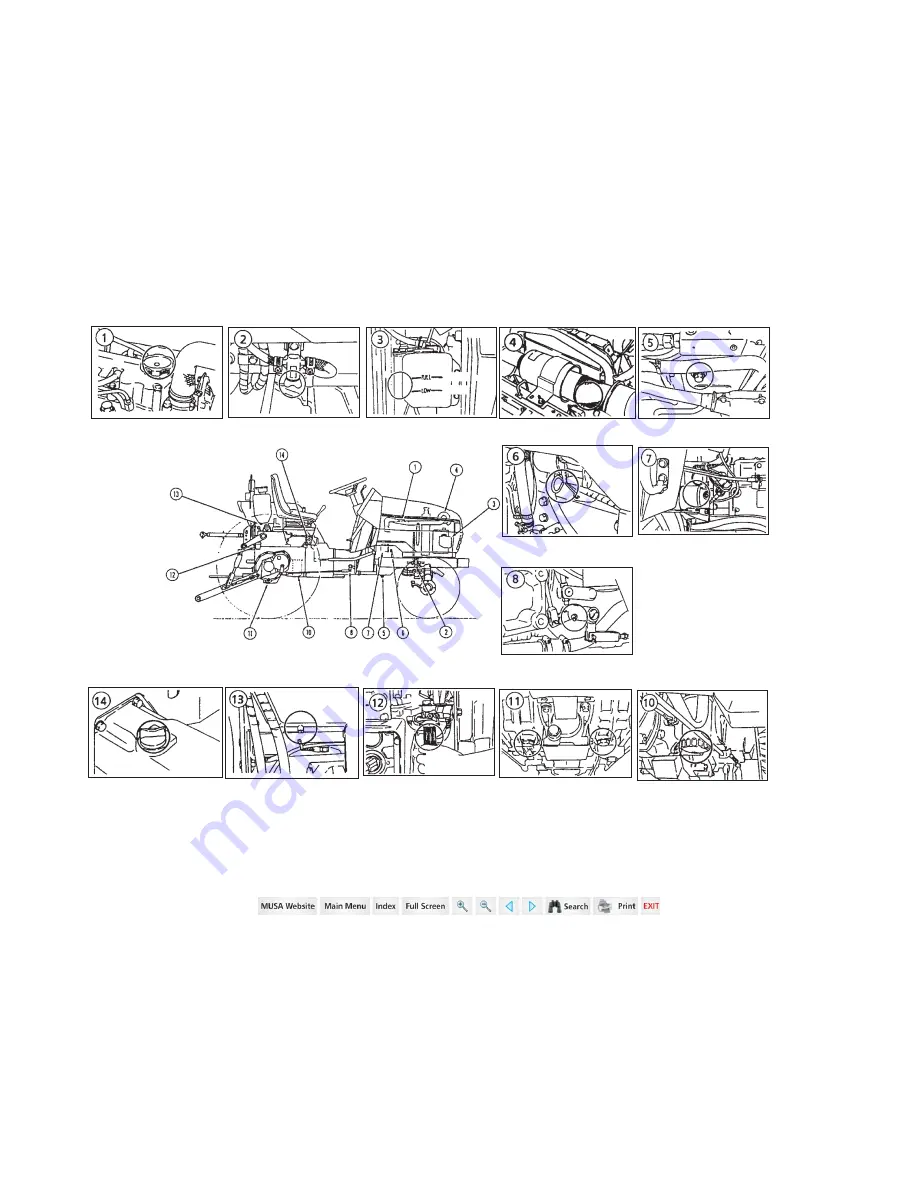
16 Series, Model - 2816 4WD
LUBRICATION/FILTERS/FLUIDS______________________________________________________________________________________________________________________________
Fluid
Levels
and
Filters
100 HRS
1000 HRS
10 HRS
10 HRS
100 HRS
10 HRS
200 HRS
10 HRS
200 HRS
200 HRS
10 HRS
50 HRS
Yearly
Engine Oil - Change
Radiator and Coolant - Drain,
Flush and Fill
Coolant Recovery Reservoir
- Check
Air Cleaner-Clean
Engine Oil - Drain
Engine Oil Filter - Change
Engine Oil - Check
Brake Pedal - Grease
Hydraulic Filter - Change
Transmission Oil - Change
Fuel Filter - Change
Fuel - Drain
Transmission Oil - Check
(Gear Drive)