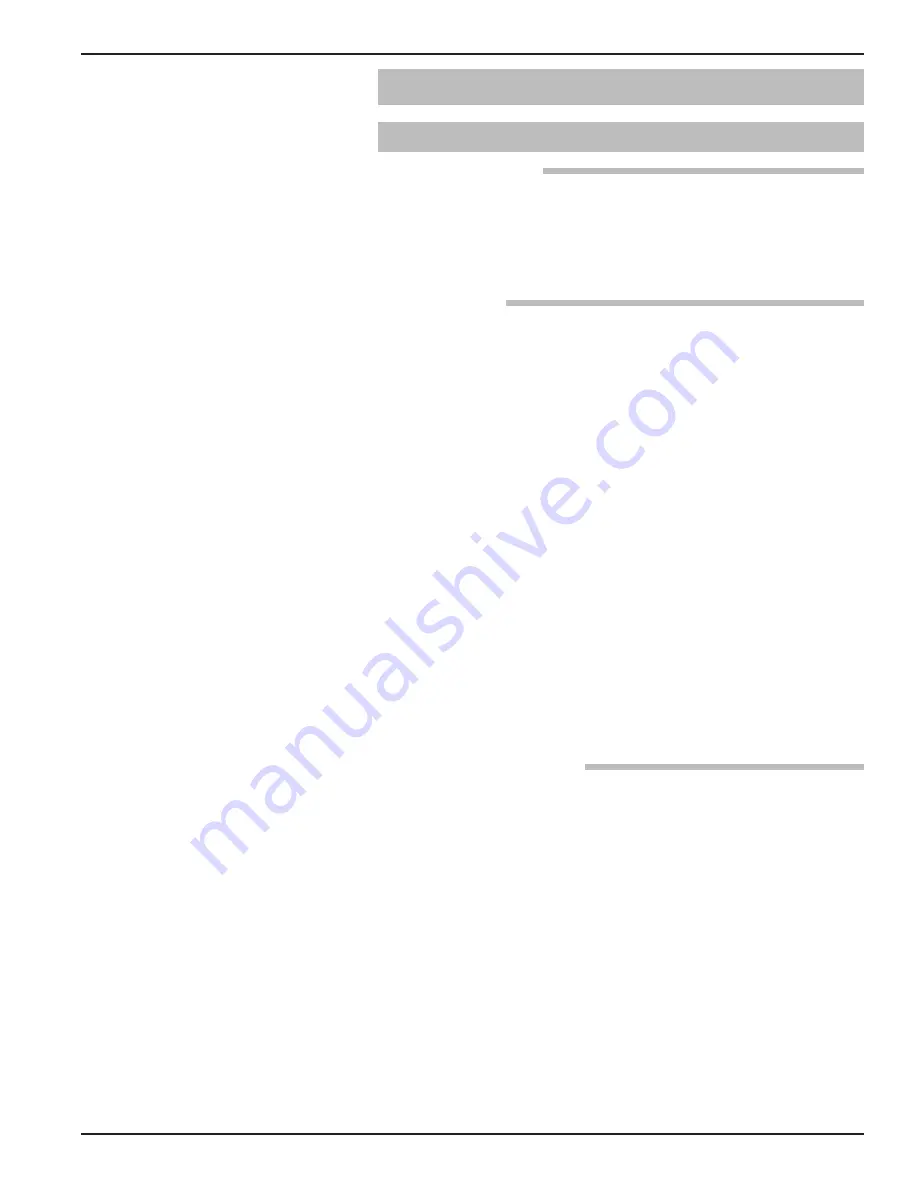
6.0
Recurrent Function Tests
6.1
Proof Testing
6.1.1 Introduction
Following are the procedures utilized to detect
Dangerous Undetected (DU) failures. The procedure
will detect approximately 90% of possible DU failures
in the Model R86.
6.1.2 Interval
To maintain the Safety Integrity Level of a Safety
Instrumented System, it is imperative that the entire system
be tested at regular time intervals (referred to as TI in the
appropriate standards). The onus is on the owner/operator to
select the type of inspection and the time period for these
tests.
The system check must be carried out to prove that the
functions meet the IEC specification and result in the
desired response of the safety system as a whole.
This system check can be guaranteed when the response
height is approached in the filling process; though, if this is
not practical, a suitable method of simulating the level of
the physical measurement must be used to make the level
sensor respond as if the fill fluid were above the alarm/set
point level. If the operability of the sensor/transmitter can
be determined by other means that exclude all fault condi-
tions that may impair the normal functions of the device,
the check may also be completed by simulating the corre-
sponding output signal of the device.
6.1.3 Recording results
Results of the Proof Test should be recorded for future
reference.
9
58-651 Pulsar
®
Model R86 SIL Functional Safety Manual