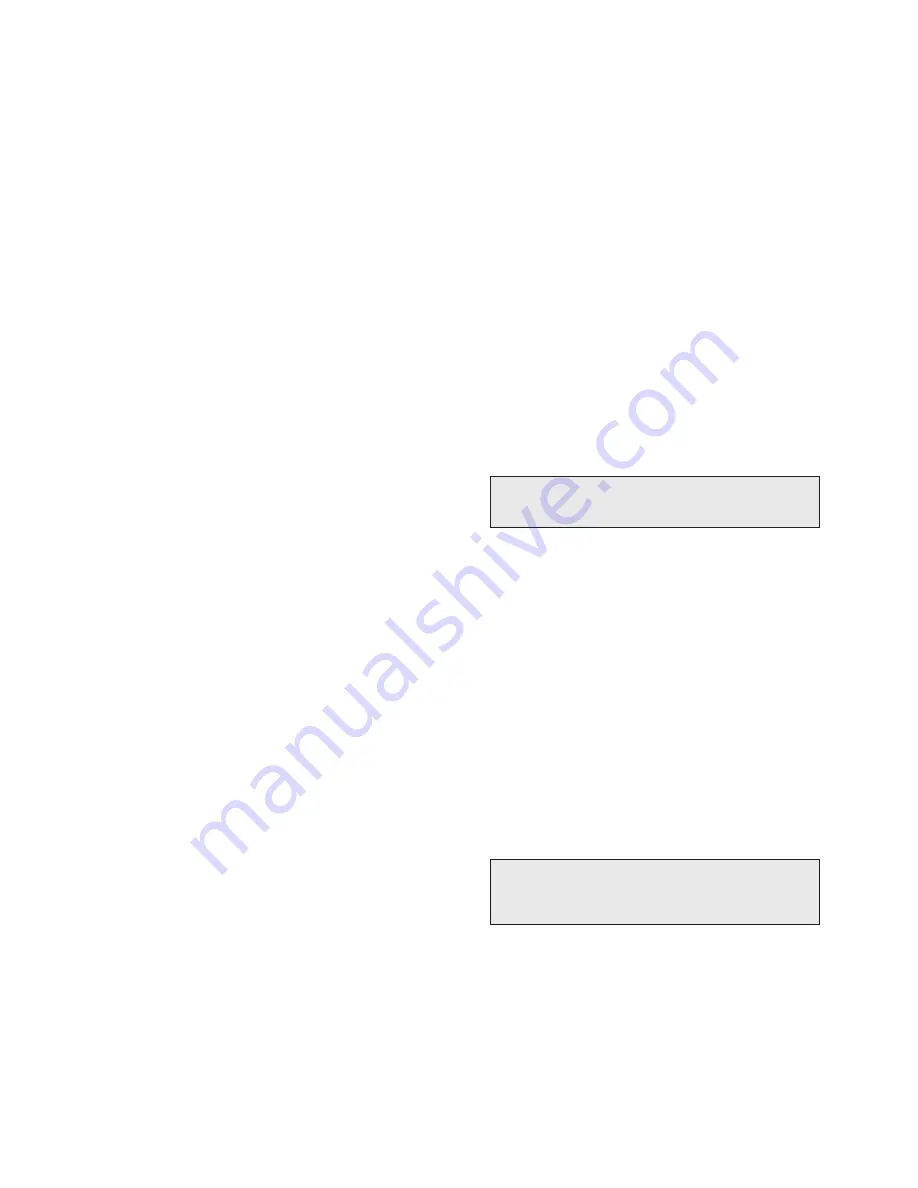
5
PREVENTIVE MAINTENANCE (cont.)
TROUBLE SHOOTING
Usually the first indication of improper operation is failure of
the controlled equipment to function i.e. pump will not start
(or stop); signal lamps fail to light, etc. When these symp-
toms occur, whether at time of installation or during routine
service thereafter, check the following potential external
causes first.
– Fuses may be blown.
– Reset button(s) may need resetting.
– Power switch may be open.
– Controlled equipment may be faulty.
– Wiring or medium lines leading to control may be
defective.
If a thorough inspection of these possible conditions fails to
locate the trouble, proceed next to a check of the controls
switch mechanism.
CHECK SWITCH MECHANISM
1. Pull disconnect switch or otherwise assure disconnect
power to the control.
2. Remove switch housing cover.
3. Disconnect power wiring from switch assembly.
4. Swing magnet assembly in and out by hand to check
carefully for any sign of binding. Assembly should
require minimal force to move it through its full swing.
5. If binding exists, magnet may be rubbing enclosing tube.
If magnet is rubbing, loosen magnet clamp screw and
shift magnet position. Retighten magnet clamp screw.
6. If switch magnet assembly swings freely and mechanism
still fails to actuate, check installation of control to be
certain it is within the specified three (3°) degrees of ver-
tical (use spirit level on side of enclosing tube in two
places, 90° apart).
7. If mechanism is equipped with a mercury switch, exam-
ine glass mercury tube closely as previously described
in “Preventive Maintenance” section. If switch is dam-
aged, replace it immediately.
8. If switch mechanism is operating satisfactorily, proceed
to check sensing unit.
CHECK SENSING UNIT
1. Check to be certain liquid is entering float chamber. A
valve may be closed or piping plugged.
2. Proceed to check level sensing action.
3. Remove the switch housing assembly by loosening the
enclosing tube nut located immediately below the hous-
ing base.
4. Inspect attraction sleeve(s) and inside of enclosing tube
for excessive corrosion or solids build-up which could
restrict movement, preventing sleeve(s) from reaching
field of magnet(s).
5. Fill chamber with liquid at room pressure. Check float(s)
to be certain it is buoyant in the liquid (float chamber
must have adequate liquid level). If float is determined to
be filled with liquid or collapsed, entire float chamber
assembly (sensing unit) should be replaced.
CHECK COMPLETE UNIT
Reassemble the unit. Reconnect the power supply and
carefully actuate the switch mechanism manually (using a
non-conductive tool) to determine whether controlled
equipment will operate.
If all components in the control are in operating condition,
the trouble must be (and should be) located external to the
control. Repeat inspection of external conditions previous-
ly described.
NOTE: If difficulties are encountered which can not be
identified, consult with the factory or your local representa-
tive for assistance. A complete description of the trouble
should be provided along with information concerning your
piping and mounting arrangement, plus a description of
your operation sequence. Sketches or photographs show-
ing the installation are also beneficial.
When communicating about your control, be certain always
to specify the complete Model and Serial numbers.
CAUTION: Unit must be normalized to atmospheric
pressure before removing switch housing assembly.
CAUTION: With electrical power “on”, care should be
taken to avoid contact with switch leads and connec-
tions at terminal block.
WHAT TO AVOID
1. NEVER leave switch housing cover off the control
longer than necessary to make routine inspections.
2. NEVER place a jumper wire across terminals to “cut-
out” the control. If a “jumper” is necessary for test pur-
poses, be certain it is removed before placing control
into service.
3. NEVER attempt to make adjustments or replace switch-
es without reading instructions carefully. Certain adjust-
ments provided for in Magnetrol controls should not be
attempted in the field. When in doubt, consult the facto-
ry or your local Magnetrol representative.
4. NEVER use lubricants on pivots of switch mechanisms.
A sufficient amount of lubricant has been applied at the
factory to ensure a lifetime of service. Further oiling is
unnecessary and will only tend to attract dust and dirt
which can interfere with mechanism operation.