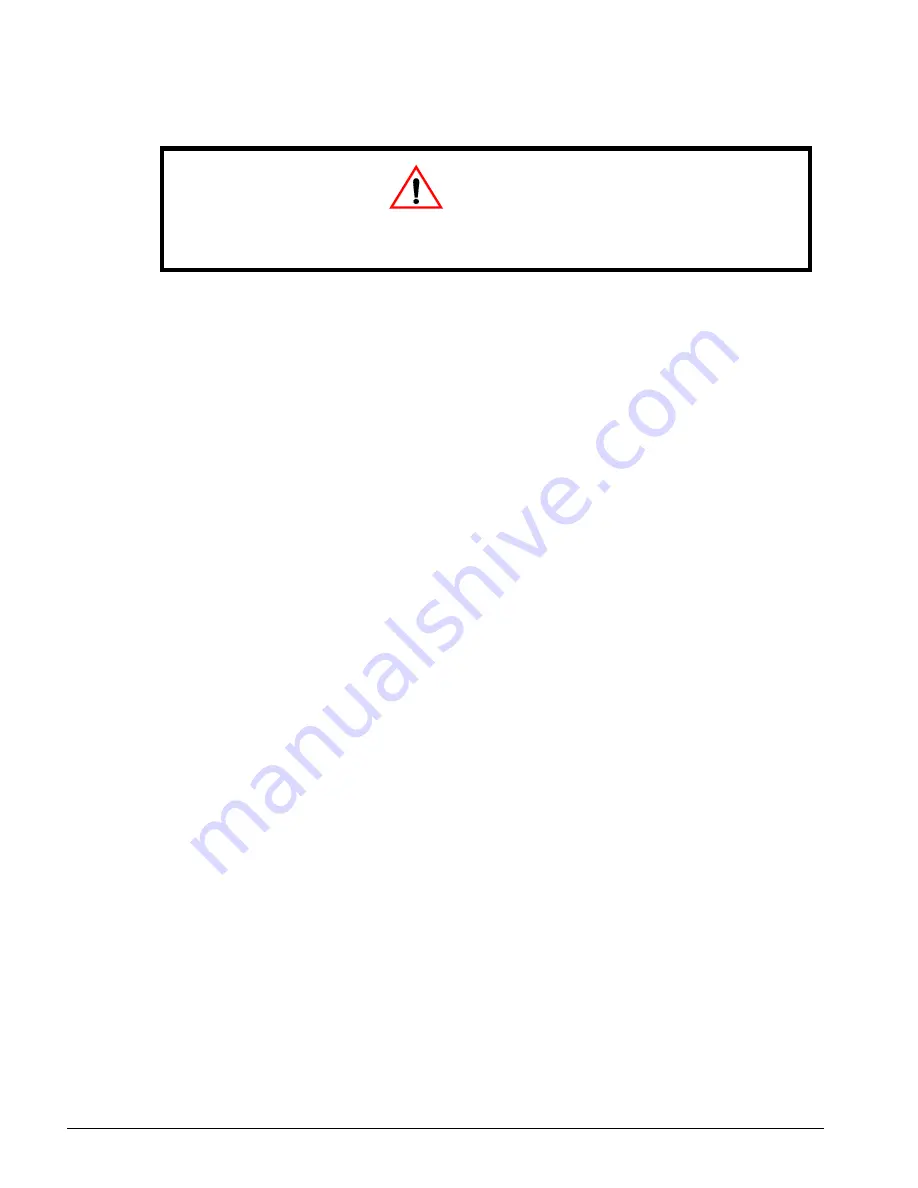
IMPULSE•T Instruction Manual - October 2015
3-3
IMPULSE•T Wiring Practices
•
Connect the incoming three-phase AC source to terminals R/L1, S/L2, and T/L3.
•
Connect the motor leads to terminals U/T1, V/T2, and W/T3.
•
Ensure that the drive-to-motor wiring distance is less than 150 ft (45.72 m) unless appropriate
reactors and/or filters are used.
•
Install a line reactor between the output of the drive in applications that require a disconnecting
means between the drive’s output and the motor. Use a “make before break” auxiliary contact
with the disconnect means and the hardware base block of the drive.
•
Use contacts between the PLC output and the drive 120/24/48 VAC input card. If using a solid
state output from a PLC (TRIAC) to a 120/24/48 VAC input card, use a 5K
Ω
, 5 Watt resistor
between the signal and X2.
•
If the power source is 500 kVA or greater, or more than 10 times the inverter kVA rating, ensure
that there is at least 3 percent impedance between the power source and the drive input. To
accomplish this, you can install a DC reactor between inverter ter1 and +2, or use an
AC line reactor on the input of the drive. If you don’t provide enough impedance, excessive peak
currents could damage the input power supply circuit.
•
Comply with “Suggested Circuit Protection Specifications and Wire Size” on page 3-7.
•
Use time delay fuses, which are sized at 150% of drive's continuous-rated current, for drive input
protection.
•
Use appropriate R-C or MOV type surge absorbers across the coil of all contactors and relays in
the system. Failure to do so could result in noise-related, nuisance fault incidents.
•
Use external dynamic braking resistors for all applications.
•
Do not ground the drive with any large-current machines.
•
Before you use any welding or high-current machines near the crane, disconnect all line and
ground wiring.
•
Do not let the wiring leads come in contact with the drive enclosure.
•
Do not connect power factor correction capacitors to the drive input or output.
•
Hard-wire the drive and motor (e.g., festoon cable). Do not use sliding collector bars.
•
If you have a user input device or interface board that is remote, use shielded cable between the
drive input terminals and the interface output terminals or user input device(s).
•
Before turning on the drive, check the output circuit (U/T1, V/T2, and W/T3) for possible short
circuits and ground faults.
•
Increase the wire size by one size for every 250 ft (76.2 m) between the drive and motor;
suggested for center driven cranes, trolleys, and bridges (voltage drop is significant at low
frequencies).
•
When using more than one transformer for the drive's power, properly phase each transformer.
WA R N I N G
Before you wire the drive, review the following practices to help ensure that your system is wired
properly.
Содержание Impulse-t 2006-T
Страница 2: ......
Страница 7: ...C h a p t e r 1 Introduction...
Страница 8: ...IMPULSE T Instruction Manual October 2015 1 2 This page intentionally left blank...
Страница 14: ...IMPULSE T Instruction Manual October 2015 1 8 This page intentionally left blank...
Страница 15: ...C h a p t e r 2 Installation...
Страница 16: ...IMPULSE T Instruction Manual October 2015 2 2 This page intentionally left blank...
Страница 21: ...C h a p t e r 3 Wiring...
Страница 22: ...IMPULSE T Instruction Manual October 2015 3 2 This page intentionally left blank...
Страница 33: ...C h a p t e r 4 Getting Started...
Страница 34: ...IMPULSE T Instruction Manual October 2015 4 2 This page intentionally left blank...
Страница 44: ...IMPULSE T Instruction Manual October 2015 4 12 This page intentionally left blank...
Страница 45: ...C h a p t e r 5 Programming Features...
Страница 46: ...IMPULSE T Instruction Manual October 2015 5 2 This page intentionally left blank...
Страница 69: ...C h a p t e r 6 Troubleshooting...
Страница 70: ...IMPULSE T Instruction Manual October 2015 6 2 This page intentionally left blank...
Страница 77: ...A p p e n d i x A Advanced Parameter Listing...
Страница 78: ...IMPULSE T Instruction Manual October 2015 A 2 This page intentionally left blank...