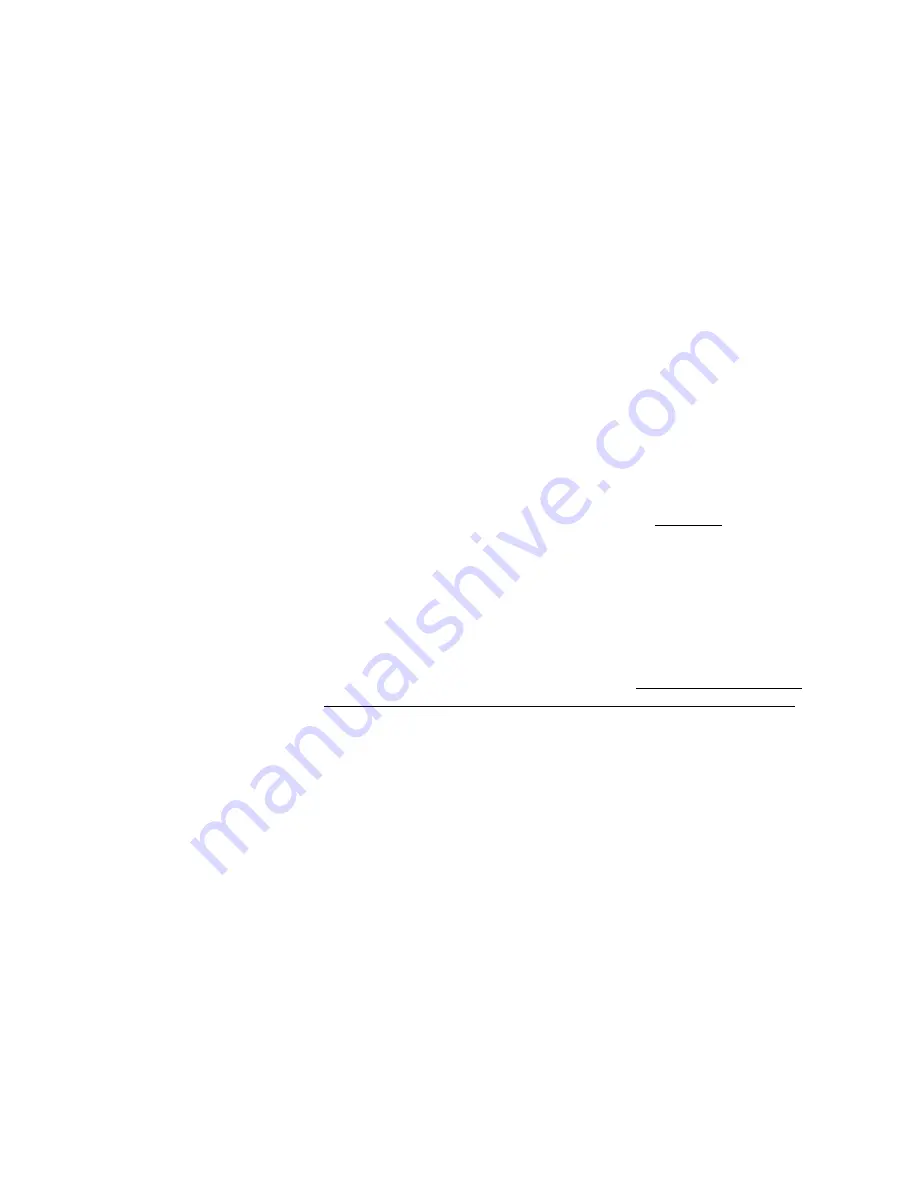
38
Cracked welds.
1. Check design of root opening, root face dimensions,
angle.
2. Check electrode wire compatibility with base metal.
3. Change welding speed or shielding gas to obtain a more
convex bead.
4. Change torch angle to improve deposition.
5. Revise joint design.
6. Determine if alloy requires preheat and/or post weld
heat
treatment.
7. Check wire for moisture in flux. (Weld using new sealed
spool)
8. Check gas for contamination. Change gas bottle.
13.4.1
MAINTAIN PROPER CONTACT TIP RECESS
For FCAW welding, the contact tip should be recessed
approximately 13mm (0.5') from the nozzle end.
13.4.2
MAINTAIN PROPER ELECTRODE STICK-OUT
The recommended electrode stick-out is critical for all-position
FCAW electrodes. These electrodes have a fast freeze slag. If
less than the minimum parameters recommended are utilized, the
slag may freeze too rapidly trapping escaping gas moisture and
causing worm tracks on the weld surface. The electrode stick out
should be approximately 25mm (1”) or more from the contact tip.
Many welders are used to welding GMAW vertical-up with the
nozzle between 1/4” (6.4 – 9.6 and 3/8” (6.4 – 9.6mm) from the
weld surface. They typically use a contact tip that was designed
for GMAW spray transfer. The electrode stick-out they often
utilize is less than 1/2” (13mm). If you use less than the minimum
electrode stick-out, you will use less voltage, less weld energy,
and increase the potential for fast freeze weld to trap excess
porosity.
Damaged GMAW and FCAW contact tips can be machine down
so that the contact tip is at least 1/2” (13mm) recessed in the
nozzle for FCAW welds.
13.4.3
CAUSES OF POROSITY AND “WORM HOLES” OR “WORM
TRACKS” (FCAW)
Porosity and worm tracks are usually the result of a combination
of incorrect electrode extension, incorrect parameters, humidity,
electrode moisture, mill scale, rust, paint, oils, or poor weld
technique.
Содержание Pipeliner II 609A
Страница 12: ...9...
Страница 13: ...10...
Страница 27: ...24...
Страница 34: ...31...
Страница 40: ...37 Undercutting 1 Reduce power 2 Reduce welding speed 3 Shorten arc length...
Страница 43: ...40 Remote Pendant...
Страница 46: ...43 14 0 ELECTRODE EXTENSION OFTEN NEGLECTED WHEN USING SELF SHIELDED CORED WIRES...
Страница 47: ...44...
Страница 48: ...45...
Страница 49: ...46 15 0 PREVENTING THE EFFECTS OF MOISTURE CONTAMINATION OF FLUX CORE WIRE...
Страница 50: ...47...