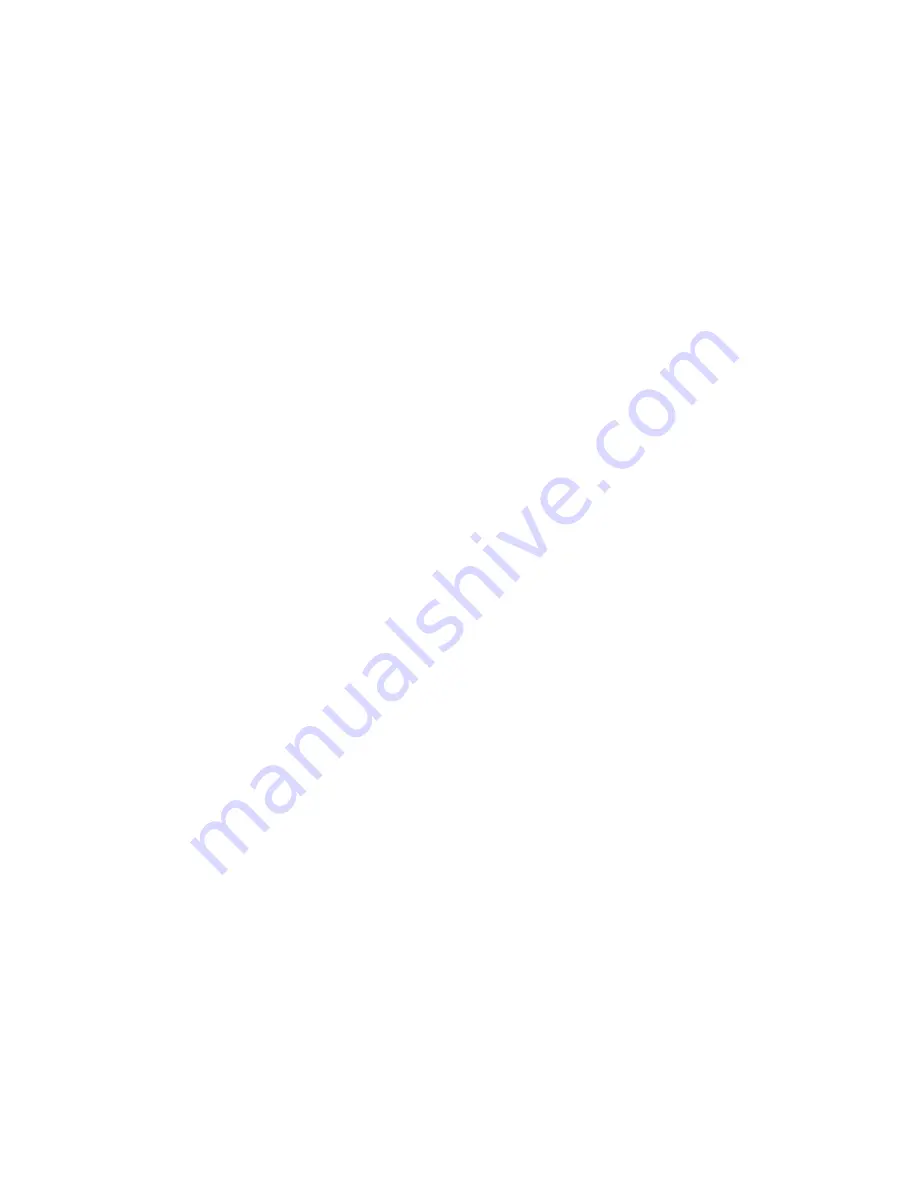
35
13.0 WELD
PROCESS
DEVELOPMENT
It is not possible within the context of this operation manual to provide a comprehensive
guide to weld procedure development. Weld procedure development requires the
experience of a competent individual experienced in the GMAW or FCAW process.
It is also important to note at this point that the Pipeliner should more properly be termed
a Mechanized Pipe Welding System. The Pipeliner Pipe Welding System is not truly
automatic in that it is not adaptive. The Pipeliner System will manipulate the torch as
required to make the weld in a highly repetitive and accurate fashion. However, the
Pipeliner System cannot sense variations in such things as fit-up and bevel geometry
which would allow it to make in-process corrections. Any procedure developed must
take into account normal variations in fit-up, prep machining etc. which will always occur
"in the field". However, the more repeatable the end prep geometry and fit-up can be
made, the more repeatable will be the welding results. It is to be expected that several
trials will have to be made before a satisfactory weld procedure can be determined. A
good starting point in developing any weld procedure is to extrapolate a previously
developed program which was been done on similar material, or pipe size, and/or bevel
geometry. If a given trial weld is unsatisfactory but shows promise, repeat the weld
changing only one parameter at a time. Always develop a procedure with the goal of
making it as tolerant as possible to weldment variations.
13.1
GENERAL COMMENTS ON WELD PROCEDURE DEVELOPMENT
The ARC TRIM CONTROL may have to be adjusted when changing shielding
gas composition, cable lengths, and sometimes with change of brand of filler
material. Start out with the ARC TRIM knob in its center position, and gradually
adjust while welding until the desired arc length/stick-out is achieved. It may be
necessary to maintain a very short arc length for puddle control when welding in
the overhead position - even at the expense of a slight amount of spatter.
13.2
The Pipeliner II can be used in all modes of metal transfer - short circuit
(Standard or non-Pulsed), globular, spray, and pulsed spray. We recommend
operation in either Standard or Pulsed mode. The MPS-4000 Power Supply will
provide programmed synergic operation in both modes. Ensure that the proper
filler wire diameters and types have been selected on the power source, and that
the appropriate shielding gas is being used. Ensure that the filler wire is of the
correct alloy and designated “ALL POSITION”.
13.3
Wire speed may be increased during sidewall DWELL periods (when using
POWER BOOST function), usually in the range of 20% - 50%. Wire speed
reductions of greater than 10 per cent during DWELL may result in an unstable
arc.
13.4
WELD PROCESS TROUBLESHOOTING GUIDE
Irregular arc start.
1. Check gas valves, increase flow 20 liters/min (45-55
CFH).
2.
Check
ground-return
circuit.
3.
Check
circuit
to
start
switch.
Содержание Pipeliner II 609A
Страница 12: ...9...
Страница 13: ...10...
Страница 27: ...24...
Страница 34: ...31...
Страница 40: ...37 Undercutting 1 Reduce power 2 Reduce welding speed 3 Shorten arc length...
Страница 43: ...40 Remote Pendant...
Страница 46: ...43 14 0 ELECTRODE EXTENSION OFTEN NEGLECTED WHEN USING SELF SHIELDED CORED WIRES...
Страница 47: ...44...
Страница 48: ...45...
Страница 49: ...46 15 0 PREVENTING THE EFFECTS OF MOISTURE CONTAMINATION OF FLUX CORE WIRE...
Страница 50: ...47...