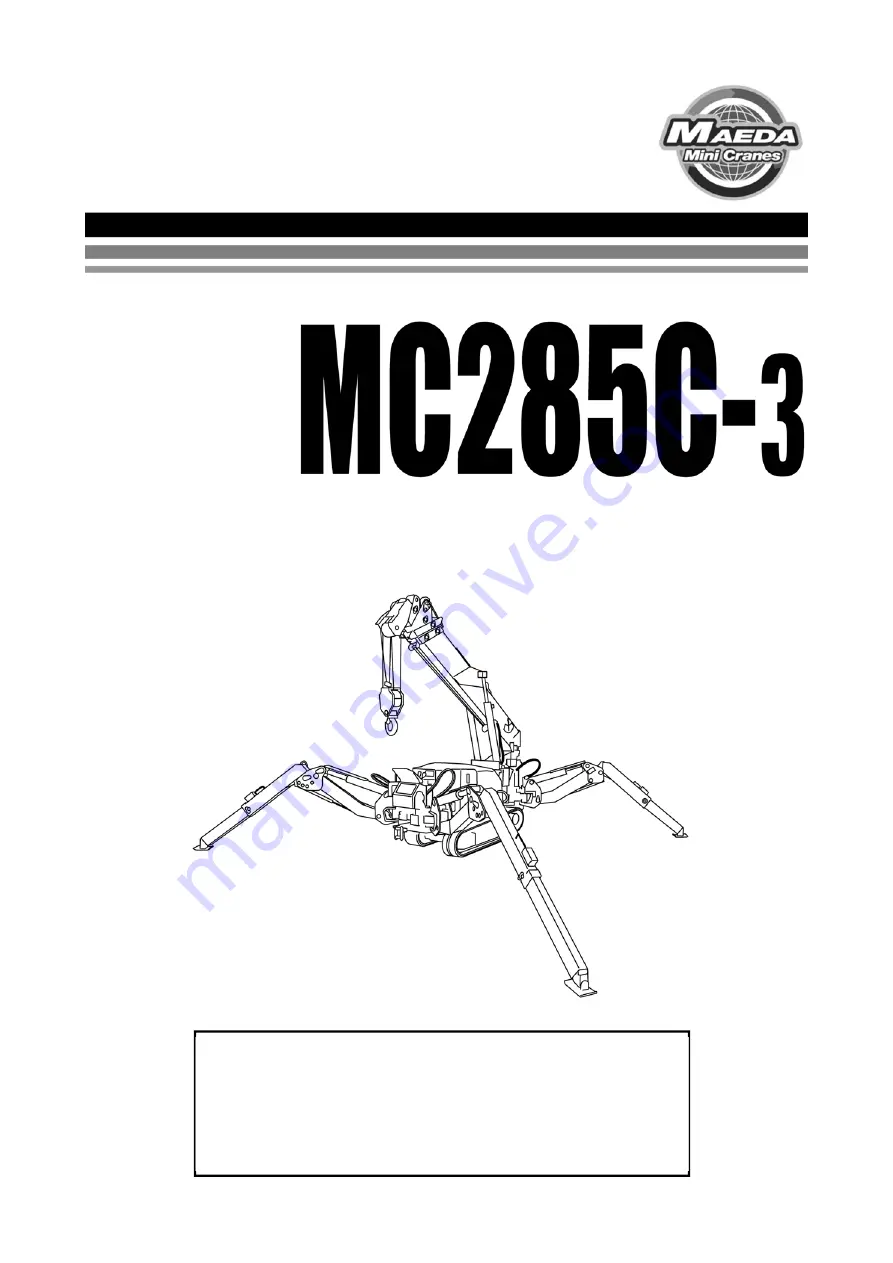
Service Manual
Mini-Crawler Crane
102ME-SM1906-00
The parts numbers and lists written in this service manual are the
references for the services such as disassembling and assembling.
Be sure to ALWAYS refer to the latest parts catalog (the latest
information) before ordering any part, since the parts and the model
numbers are subject to change during the endless improvements and
changes of our Machine.
Содержание MC285C-3
Страница 2: ......
Страница 12: ......
Страница 14: ...1 2 1 OUTSIDE DRAWING 1 1 NON ELECTRIC MOTOR MODEL 1 2 ENGINE AND ELECTRIC MOTOR SPECIFICATIONS ...
Страница 15: ...1 3 2 DIMENSIONAL DRAWING OF OUTRIGGER WIDTH ...
Страница 20: ...1 8 6 WORKING RADIUS LIFTING HEIGHT ...
Страница 24: ......
Страница 28: ...2 4 1 1 3 ENGINE ACCESSORIES 102 1152100 ...
Страница 30: ...2 6 1 1 4 FUEL PIPING 102 2142400 ...
Страница 31: ...2 7 1 2 ENGINE U S MODEL SHIBAURA TYPE E672L F 6701 1 2 1 COMPONENTS OF ENGINE ...
Страница 33: ...2 9 1 2 3 ENGINE ACCESSORIES 102 1176300 ...
Страница 35: ...2 11 1 2 4 FUEL PIPING 102 2207700 ...
Страница 38: ...2 14 2 POWER TRANSMISSION SCHEMATIC DIAGRAM 2 1 HYDRAULIC SYSTEM DIAGRAM ...
Страница 39: ...2 15 2 2 SLEWING SYSTEM 2 2 1 OUTSIDE DRAWING ...
Страница 41: ...2 17 3 UNDERCARRIAGE AND FRAME 3 1 TRACK FRAME ...
Страница 42: ...2 18 3 2 FRONT IDLER 3 3 GREASE CYLINDER 353 2069500 ...
Страница 43: ...2 19 3 4 CARRIER ROLLER UPPER ROLLING WHEEL 3 5 TRACK ROLLER 353 3210400 ...
Страница 44: ...2 20 3 6 TANDEM ROLLER ASSEMBLY 3 7 SPROCKET ...
Страница 45: ...2 21 3 8 RUBBER CRAWLER ...
Страница 46: ...2 22 4 HYDRAULIC UNITS 4 1 HYDRAULIC UNITS LAYOUT DIAGRAM ...
Страница 47: ...2 23 ...
Страница 48: ...2 24 4 2 HYDRAULIC OIL TANK 102 2208500 ...
Страница 52: ...2 28 4 3 2 INTERNAL STRUCTURE S102J3957000 ...
Страница 64: ...2 40 4 11 DERRICKING CYLINDER 4 11 1 LEFT SIDE DERRICKING CYLINDER Part No 353S64500000 ...
Страница 66: ...2 42 4 11 2 RIGHT SIDE DERRICKING CYLINDER Part No 353S69700000 ...
Страница 68: ...2 44 4 12 TELESCOPING CYLINDER 4 12 1 APPEARANCE MODEL Part No 353S61300002 ...
Страница 71: ...2 47 4 12 2 TELESCOPING CYLINDER HYDRAULIC SYSTEM DIAGRAM ...
Страница 75: ...2 51 4 13 OUTRIGGER CYLINDER 4 13 1 APPEARANCE MODEL Part No S102F2389000 ...
Страница 84: ...2 60 4 14 5 RETURN LINE 02 TRAVEL CRANE CONTROL VALVE ROTARY JOINT 6 20 MANIFOLD BLOCK 102 1148800 5 ...
Страница 88: ...2 64 4 14 8 TRAVEL LINE TRAVEL CONTROL VALVE TRAVEL MOTOR 353 2068300 ...
Страница 90: ...2 66 4 14 9 CONTROL A LINE CRANE CONTROL VALVE OR SELECT VALVE 102 2140000 ...
Страница 94: ...2 70 4 14 11 OUTRIGGER LINE OR SELECT VALVE OUTRIGGER CYLINDER 102 2140300 ...
Страница 100: ...2 76 5 WORK EQUIPMENT 5 1 BOOM ASSEMBLY DIAGRAM 102 1207000 ...
Страница 101: ...2 77 ...
Страница 103: ...2 79 5 2 HOOK ASSEMBLY DIAGRAM ...
Страница 105: ...2 81 5 4 WINCH ASSEMBLY 353 1093700 ...
Страница 106: ...2 82 5 5 OUTRIGGER 5 5 1 APPEARANCE OF OUTRIGGER 1 102 2139500 ...
Страница 107: ...2 83 5 5 2 APPEARANCE OF OUTRIGGER 2 102 2139600 ...
Страница 108: ...2 84 5 5 3 APPEARANCE OF OUTRIGGER 3 102 2139700 ...
Страница 109: ...2 85 5 5 4 APPEARANCE OF OUTRIGGER 4 ...
Страница 110: ...2 86 5 6 TRAVEL CONTROL 5 6 1 TRAVEL CONTROL ASSEMBLY 102 119810 0 ...
Страница 111: ...2 87 5 6 2 TRAVEL CONTROL ASSEMBLY DETAILS 102 1198100 ...
Страница 112: ...2 88 6 ELECTRICAL UNITS 6 1 ELECTRICAL UNITS LAYOUT DIAGRAM ...
Страница 124: ...2 100 6 5 2 VEHICLE BODY WIRE HARNESS VALVE STAND PART 102 1206600 01 ...
Страница 125: ...2 101 6 5 3 VEHICLE BODY WIRE HARNESS ENGINE ELECTRIC BOX PART 102 1206600 01 ...
Страница 126: ...2 102 6 5 4 VEHICLE BODY WIRE HARNESS MONITOR CASE PART 102 1206600 01 ...
Страница 127: ...2 103 6 5 5 VEHICLE BODY WIRE HARNESS TRAVEL LEVER PART 102 1206600 01 102 1206600 02 ...
Страница 128: ...2 104 6 5 6 VEHICLE BODY WIRE HARNESS OUTRIGGER PART 102 1206600 02 ...
Страница 129: ...2 105 6 6 VEHICLE BODY WIRE HARNESS U S SHIBAURA ENGINE 6 6 1 VEHICLE BODY WIRE HARNESS GENERAL DRAWING 102 1206000 01 ...
Страница 130: ...2 106 6 6 2 VEHICLE BODY WIRE HARNESS ENGINE ELECTRIC BOX PART 102 1206000 01 ...
Страница 132: ...2 108 6 7 SENSORS 6 7 1 INCLINATION SENSOR Part No S102M3958000 6 7 2 TIP OVER WARNING DEVICE 102 3419900 ...
Страница 136: ...2 112 7 3 ML ASSEMBLY 102 3430100 102 1198300 ...
Страница 137: ...2 113 7 3 1 LDC CONTROLLER 7 3 2 MAIN CONTROLLER TTC60 ...
Страница 138: ...2 114 7 3 3 LOWER CONTROLLER TTC36X ...
Страница 139: ...2 115 7 3 4 UPPER CONTROLLER TTC30XH ...
Страница 140: ...2 116 7 3 5 TRI COLOUR LIGHTS 7 3 5 1 Tri colour lights model ...
Страница 143: ...2 119 7 4 OR POSITION DETECTION ASSEMBLY ...
Страница 144: ...2 120 7 5 OR OPEN DETECTION ASSEMBLY 7 6 OR EXTENSION DETECTION ASSEMBLY 102 2208300 102 2208400 ...
Страница 145: ...2 121 7 7 BOOM DISPLACEMENT DETECTION ASSEMBLY 102 2208700 ...
Страница 146: ...2 122 7 7 1 TOTAL LENGTH REEL 349S53400002 ...
Страница 148: ...2 124 7 8 LOAD DETECTION ASSEMBLY 102 3430700 ...
Страница 149: ...2 125 7 8 1 PRESSURE AND OIL TEMPERATURE SENSOR S200J3315000 ...
Страница 151: ...2 127 7 9 LEVER DETECTION ASSEMBLY 7 10 OVER UNWINDING PREVENTION DEVICE 102 3428600 102 2208100 ...
Страница 152: ...2 128 7 11 GROUND DETECTION ASSEMBLY 102 3430600 ...
Страница 153: ...2 129 7 12 SLEWING DETECTION ASSEMBLY 7 12 1 DIGITAL MAGNETIC REVOLUTION SENSOR Part No S102M395900 102 2206600 ...
Страница 154: ...2 130 7 13 OVER HOISTING PREVENTION DEVICE ASSEMBLY 102 3430800 ...
Страница 156: ......
Страница 161: ...F3 5 1 2 NAME AND DESCRIPTION OF THE TRANSMITTER DISPLAY 1 2 1 DESCRIPTION OF THE DISPLAY INDICATION SCREEN ...
Страница 165: ...F3 9 1 3 NAME AND DESCRIPTION OF THE RECEIVER R1 Control box R2 Monitor LED R3 Connector connection port R4 Antenna ...
Страница 172: ...F3 16 3 3 ELECTRICAL WIRING DIAGRAM FOR REMOTE CONTROL ...
Страница 173: ...F3 17 3 4 ELECTRICAL WIRING FOR REMOTE CONTROLLER DIAGRAM ...
Страница 175: ...F3 19 5 SERVICE LOCATIONS ...
Страница 176: ...F3 20 ...
Страница 199: ...HYDRAULIC CIRCUIT DIAGRAM 6 1 HYDRAULIC AND ELECTRIC CIRCUIT DIAGRAMS ...
Страница 200: ...ELECTRICAL DIAGRAM 6 2 ...
Страница 202: ...7 2 1 ELECTRIC MOTOR UNIT ASSEMBLY 102 1206400 ...
Страница 203: ...7 3 ...
Страница 206: ...7 6 2 ELECTRIC MOTOR WIRE HARNESS ASSEMBLY 102 3429700 ...
Страница 220: ...7 20 5 ELECTRICAL WIRING DIAGRAM ...
Страница 241: ...9 11 4 AUXILIARY WINCH ASSEMBLY 102 2161700 ...
Страница 242: ...9 12 5 AUXILIARY WINCH ACCESSORIES ASSEMBLY 5 1 AUXILIARY WINCH ACCESSORIES 102 1168300 102 1167400 ...
Страница 244: ...9 14 5 3 AUXILIARY WINCH THREE WIND STOP ...
Страница 246: ...9 16 6 APPEARANCE AND SPECIFICATIONS OF AUXILIARY WINCH MOTOR ...
Страница 247: ...9 17 7 HYDRAULIC PIPING FOR AUXILIARY WINCH ...
Страница 258: ......
Страница 266: ......
Страница 292: ......
Страница 299: ...T 307 Related electric circuits crane control valve ...
Страница 300: ...T 308 Location crane control valve ...
Страница 302: ...T 310 Related electric circuits engine start relay ...
Страница 303: ...T 311 Location power supply monitor box ...
Страница 305: ...T 313 Location crane control valve ...
Страница 308: ...T 316 Related electric circuits emergency stop valve low pressure valve ...
Страница 310: ...T 318 Relevant electric circuits sensor power supply ...
Страница 311: ...T 319 Location sensor power supply ...
Страница 312: ...T 320 Location sensor power supply ...
Страница 314: ...T 322 Related electric circuits emergency release inclination buzzer ...
Страница 316: ...T 324 Related electric circuits Lighting equipment horn ...
Страница 317: ...T 325 Location Lighting equipment horn ...
Страница 320: ...T 328 Related electric circuits upper control ...
Страница 321: ...T 329 Location upper control ...
Страница 326: ......
Страница 330: ...T 404 Yanmar 2TNV70 NMBA Engine Domestic CE specifications Location Yanmar engine ...
Страница 331: ...T 405 Shibaura model E672L F 6701 U S specifications Location Shibaura engine ...
Страница 337: ...T 411 Location fuse valve stand ...
Страница 341: ...T 415 Related electric circuits engine start ...
Страница 346: ...T 420 Location information Crane control valve S102G3946000 NSS50 REFA4T 12 ...
Страница 358: ......