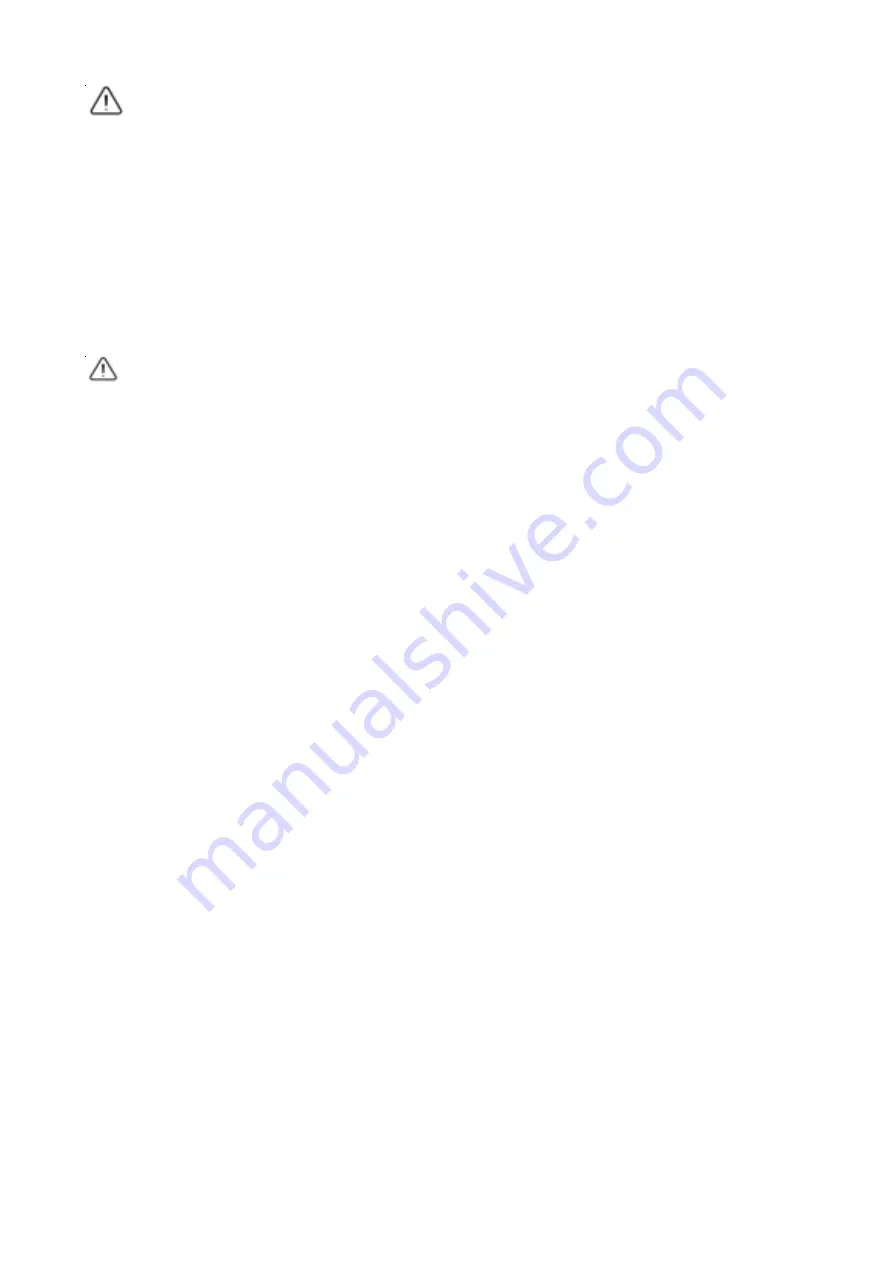
Most accidents occur because of a component
rupture. Be certain that any and all system
components will withstand the pressures being
developed. Never exceed the pressure rating of any
component installed in the system.
Weak, worn or damaged hoses are also a hazard.
Before each use check hose for signs of wear, leaks or
loose fittings. Tighten all fluid connections regularly
and replace weak or damaged hose. Your personal
safety and well being are at stake.
Before attempting any repairs or maintenance of this
product disconnect air supply and release oil line
pressure by squeezing hand piece/gun trigger.
Never allow any part of the human body to come
in front of or in direct contact with a material
outlet. Never point the nozzle of the gun at yourself or
anyone else.
ASSEMBLY
1) Measure the depth of the drum/tank and attach
appropriate length of 1” BSP (1” NPT USA/Canada)
threaded pipe to the inlet of the pump (or use a
Macnaught suction tube kit TB25s).
2) Remove the bung adaptor assembly from the pump
and screw into drum/tank opening. Carefully lower
the pump through bung adaptor and tighten the clamp
screw located at the clamp sleeve.
Note: There is a wire mesh strainer located in the brass
air inlet. It is recommended that a micro-fine (5 micron)
in-line air filter is fitted to the air inlet to ensure maximum
efficiency of this pump.
3) Before connecting the air supply, the user should add
a ‘stop’ compressed air cock.
Note: The air cock must be a ¼ turn type (allowing quick
closure ) and should be located close to the body of the
pump and be easily recognised.
OPERATION
1)
Ensure that the drum or tank is ‘vented’.
2)
Partially open the on/off air valve. The pump will
prime automatically.
3)
Open the oil delivery outlet/nozzle. The pump will
automatically start.
4)
Adjust on/off air valve to regulate the flow. Close
delivery outlet/nozzle to stop flow.
Caution! Do not run the pump dry. Remember to switch
air supply off if not using the pump for an extended period
e.g. at the end of each working day.
MAINTENANCE
Before carrying out any maintenance disconnect the air
supply and release the fluid pressure in the system.
Inspect your oil pump weekly for any signs of damage.
Replace any suspect or damaged parts/components as
required.
Every 2 weeks (or sooner if the pump is used every day)
apply a few drops of light oil to the air inlet of the pump.
(Sewing machine oil is ideal).
PUMP DISASSEMBLY
1) Remove oil hose from the pump unit.
2) Withdraw pump from the oil drum/tank. Use a clean
bench to carry out maintenance.
3) Remove the 4 screws (19) holding cylinder (7) to base
(14). Lever the cylinder off the base. There is a slot in
the base near the valve body (31).
4) Remove the cover screw (6) and valve body cover
(33).
5) Remove the 6 screws (35) holding the valve body (31)
to the cylinder (7). Remove the valve body assembly
and valve gasket (29).
6) Pull out the 2 brass pins (34) from the valve body.
Lever out the valve plugs (30) and (39).
7) Gently push the spool (36) out of the valve body. Be
careful when removing the O-Rings (5) and (38).
8) Remove top (long) poppet valve assembly (2), (3), (4)
and O-Rings (1), (5) and the bottom (short) poppet
valve assembly (28), (32) (3) and O’Rings (1) (5).
9) Hold hex section foot valve (27) horizontally in a vice.
Hold air piston firmly and unscrew allen head screw
(8). Remove screw and piston from piston rod.
10) Carefully unscrew the foot valve and pump cylinder
assembly (24), (25), (26) (27) from cylinder base
(14).
11) Withdraw the piston and piston road assembly from
the cylinder base.
12) Clean and inspect all parts. Replace any suspect or
worn or damaged parts.
PUMP REASSEMBLY
1) Ensure that all parts have the correct orientation. If
parts are assembled upside down, the pump will not
work. Check the parts diagram for correct orientation.
2) Apply thread sealant (Loctite or similar) to pump
cylinder thread (24) when reassembling the unit.
3) Assembly of the pump is a reversal of the disassembly
procedure.
4) Ensure that all O-Rings, particular in the valve body
(31) and poppet valve (2), (28) areas sit square.
5) Apply light grease (eg Petroleum Jelly) to O-Rings (17),
(43) and piston seals (11) before fitting cylinder (7) to
base (14).
6) Fit the pump to your oil drum/tank and reconnect
the oil hose and air supply. Open dispensing nozzle
to ensure correct operation.
WARNING