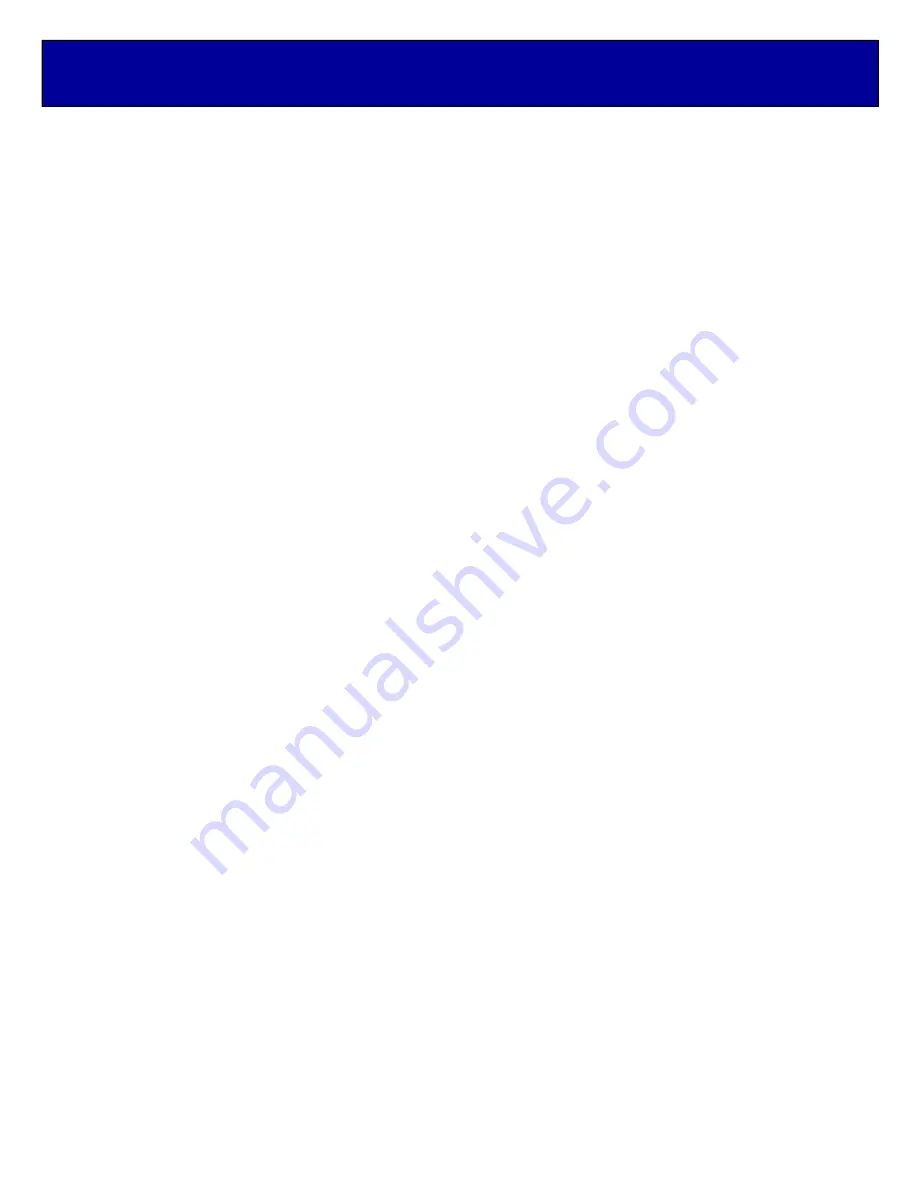
4. Element #3 is has 3 internal sleeves as noted on the ELEMENT ASSEMBLY drawing. Again start
at the butt and insert the 1-3/8 x 25” sleeve and hold in place with a 1/4-20 x 2” bolt and locknut
but don’t tighten. Next, install an element clamp block 1/4” in from the end. Secure with 8-32 x 2”
screw and locknut, align with the element hole and tighten. Add the small clamp block and secure
as before. Now insert ( if not already in) the 1-1/8” x 35” inner sleeve into the butt of the 1-1/4”
section and attach to the 1-1/2” section. Continue assembling the rest of the element. Tighten all
element hardware. Finally remove the 1/4-20 x 2” bolts and install the element halves on the
center insulator assembly. Re-install the bolts and tighten.
5. Element #2 has an outer 1-5/8 x 27” sleeve and an inner 1-3/8 x 85” sleeve. The inner sleeve
should already be in place from the factory. Slide on the outer sleeve and hold in place using
another 1/4-20 x 2” bolt and locknut but don’t tighten. Next slip on another ELEMENT CLAMP
BLOCK with a 1-1/2” hole. Note that the very end of the element is still 1-1/2” O.D. secure the
clamp at 1/4” from the butt end of the element and secure with 8-32 x 2” screw and locknut
aligning as before. Add the small clamp block and secure loosely with another 1/-20 x 1” flat head
bolt and locknut. As you insert the next 1-1/4” section, note that it goes in 5” instead of the normal
3”. This is so it can couple with the last inch or so of 1-3/8” sleeve inside the 1-1/2” section. This
overlap is extremely important to maintain the overall strength of the element in this joint. Continue
assembling the rest of the element. Tighten all element hardware. Finally, remove the bolts and
slip each element half on the center insulator assembly. Re-install the bolts and tighten.
Now install the two 1/4” eyebolts. Install a thimble or cable eye in each eyebolt and attach a 166”
length of HPTG-1200 and secure with two clips. Repeat for the other element half. Open the 5/16”
turnbuckles till just one thread shows inside the body of the turnbuckle. Add a thimble to each
turnbuckle eye and secure the cable at each turnbuckle with two clips.
6. Element #1 is last and requires the most attention. SEE LINEAR LOADED ELEMENT ASSEMBLY
drawing. This element is almost the same as #2 except for the linear loading. Prepare the element
as shown except for the linear loading (3/16” dia. Rods). Now place the element on a level surface
with the support post up. FROM THE ELEMENT BUTT SIDE, feed a 3/16” LINEAR LOADING
RODS through the flat, support insulator and into the LL ARMS until 1/2” extends beyond each
arm. Tighten the 8-32 x 1/4" set screws. Using the 3/8 x 3” “Push tube”, Install two SHAFT
RETAINERS, one at a time, onto this rod tip and snug up against each linear loading arm.
NOTE: to start the RETAINER, hold the 3/8 x 3" PUSH TUBE in your hand with one end between
your thumb and forefinger. Now center retainer on this end, “dish” into tube, and hold in place with
the same thumb and forefinger. Grasp the linear loading rod near the end with your other hand and
firmly push the retainer onto the rod.
Next, cut two 9 foot (108”) lengths of HPTG 1200 Philistran. Note that one of the two center
grooves in the pre-assembled LINEAR LOADING CLAMP assemblies is “on center”. Slip about 4”
of the HPTG 1200 through the center groove and back through the other so about 2” of cable is
there for the 1/8” cable clip. Now slide this assembly on the rods to the dimension shown. Tighten
the center screw enough to hold the assembly together. Align it so it is parallel with the ground and
tighten all screws. Double check you dimension to make sure nothing has slipped. Correct if
necessary. Repeat for the other element half.
Now attach the other end of the HPTG 1200 cables to center 5/16” turnbuckles. Open the
turnbuckle first and install a cable eye in each turnbuckle. Pull the lines tight and tighten the clips.
Final tensioning of the linear loading rods is done with the turnbuckles. Adjust until each element
droops 10 to 16 inches at the tip. NOTE: The element is most stable in wind with a small amount of
droop.
8-30LP9 ASSEMBLY MANUAL
Содержание 8-30LP9
Страница 5: ...8 30LP9 DIMENSION SHEET ...
Страница 6: ...8 30LP9 ELEMENT ASSEMBLY ...
Страница 8: ...LINEAR LOADED ELEMENT ASSEMBLY ...