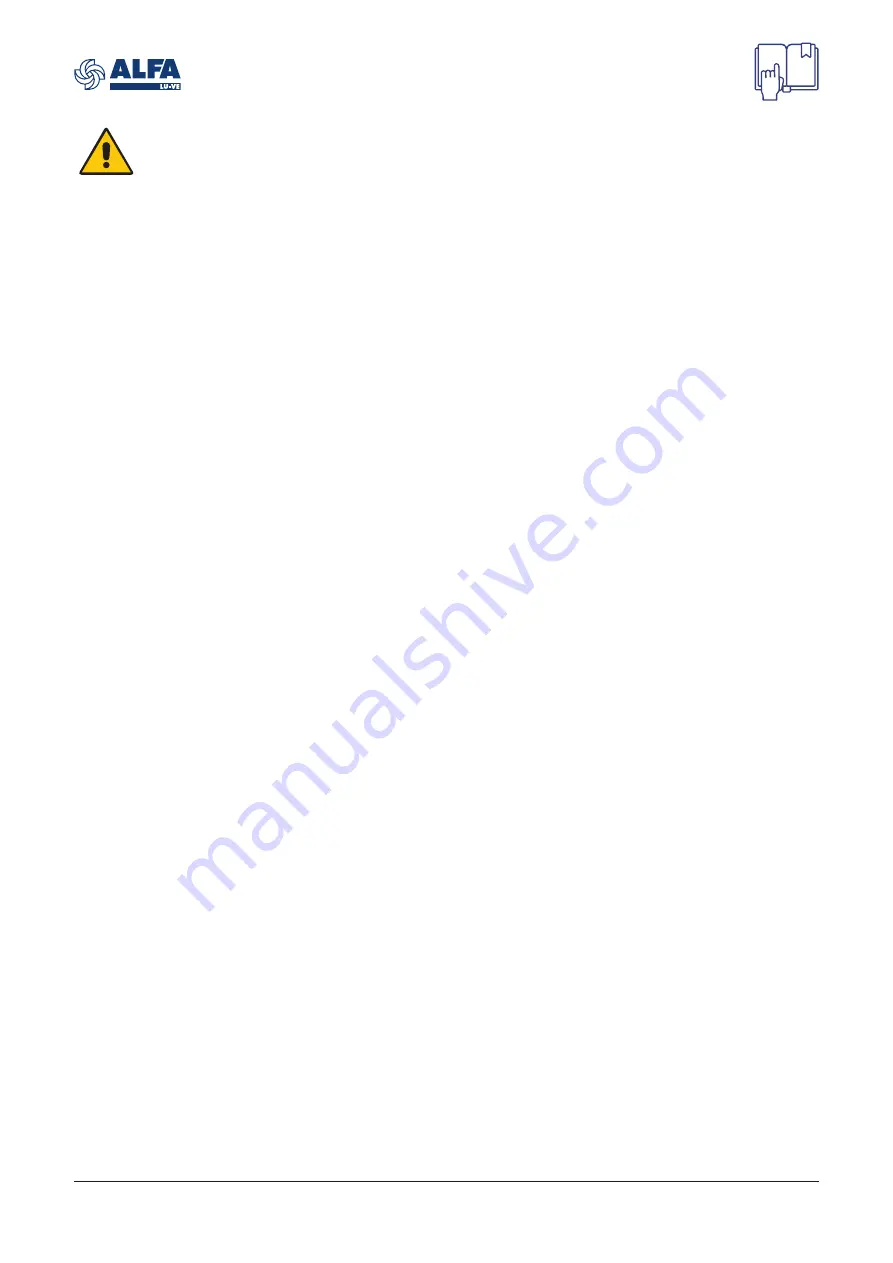
31515694EN-02
19
Alfa LU-VE is a trademark registered and owned by LU-VE Group.
Alfa LU-VE reserves the right to change specifications without prior notification.
7 Maintenance
It is essential after delivery that adequate protection and inspection are carried out on the equip-
ment. This is especially important if there is any delay in installing or commissioning the equipment.
After commissioning and setting up the defrost systems, the heat exchanger will require mainte-
nance. Regular checks and good maintenance will ensure trouble free operation. The frequency
of checks will depend on site location and the specific operating conditions. Equipment installed
in industrial or coastal areas, or in any kind of aggressive environment, generally requires more
frequent inspections than the same equipment in rural, unpolluted areas. Damage can occur during
site installation and during the period prior to commissioning. Inspections and remedial work should
take place during this period. On sites where building work is in progress, it is strongly advised that
finned block, headers and return bends are covered up to keep them clean and protected from
damage until the time of commissioning.
Header and cooler tubes can be extremely cold! Take precautions when maintenance is carried out
near the header and cooler tubes.
Ensure complete electrical isolation before performing any maintenance activity.
7.1 Shut down periods
Even during prolonged shut down periods, maintenance should be carried out. If the shut down
period is extended, all electric motors should be run once every four weeks for a minimum of 4
hours. EC fans must be kept powered during shut down periods.
7.2 Moisture in the refrigeration system
Moisture in a refrigeration system is undesirable. Moisture can cause malfunctioning in the refrig-
eration operation. A lesser known problem is that small amounts of moisture in the refrigeration sys-
tem can after a time cause leakage through the formation of frost clumps. These frost clumps are
the result of moisture seeping from the refrigeration system during defrost, as water seeps into the
soldering seams and then freezes, resulting in a volume increase. This process repeats itself during
each freeze/defrost cycle, as a result of which the cavities (potholes) thus formed become steadily
larger and ultimately burst, causing leakage.
7.3 Cleaning and disinfecting
A coil block should be kept clean to guarantee it works well. The user of the heat exchanger should
ensure that the cleaning and disinfecting agents that are used do not have a corrosive effect on the
materials used by Alfa LU-VE.
7.4 Casing
Casework checks should be carried out at least every 3 months. In doing so, inspect for any dete-
rioration of coating and/or corrosion. If such flaws are noted, take immediately remedial action.
Should any damage occur during installation, this should be repaired immediately to prevent further
deterioration.
7.5 Coil and drip tray
The heat exchanger coil should be checked at least every 3 months, with close inspection being
carried out for such things as leaks or chafing of tubes. In addition, any unusual vibration of the
fans should be checked. The unit should be cleaned as instructed when necessary using low pres-
sure compressed air, and/or low pressure water hose or a mild detergent wash. Care must be taken
not to hose directly onto fan motors or electric control panels or the electrical connection boxes of
the heaters. It should be noted that abnormal atmospheric conditions can greatly harm the lifetime
of the finned coil.
Please ensure the drip tray is empty before it is disassembled. The weight of any leftover water
could injure the operator if the drip tray fell open accidentally.
When opening/closing the drip tray, pay attention in order to avoid interference between impellers
and fan collars.
Содержание ALFA Optigo SFMD
Страница 24: ...alfa luvegroup com ...