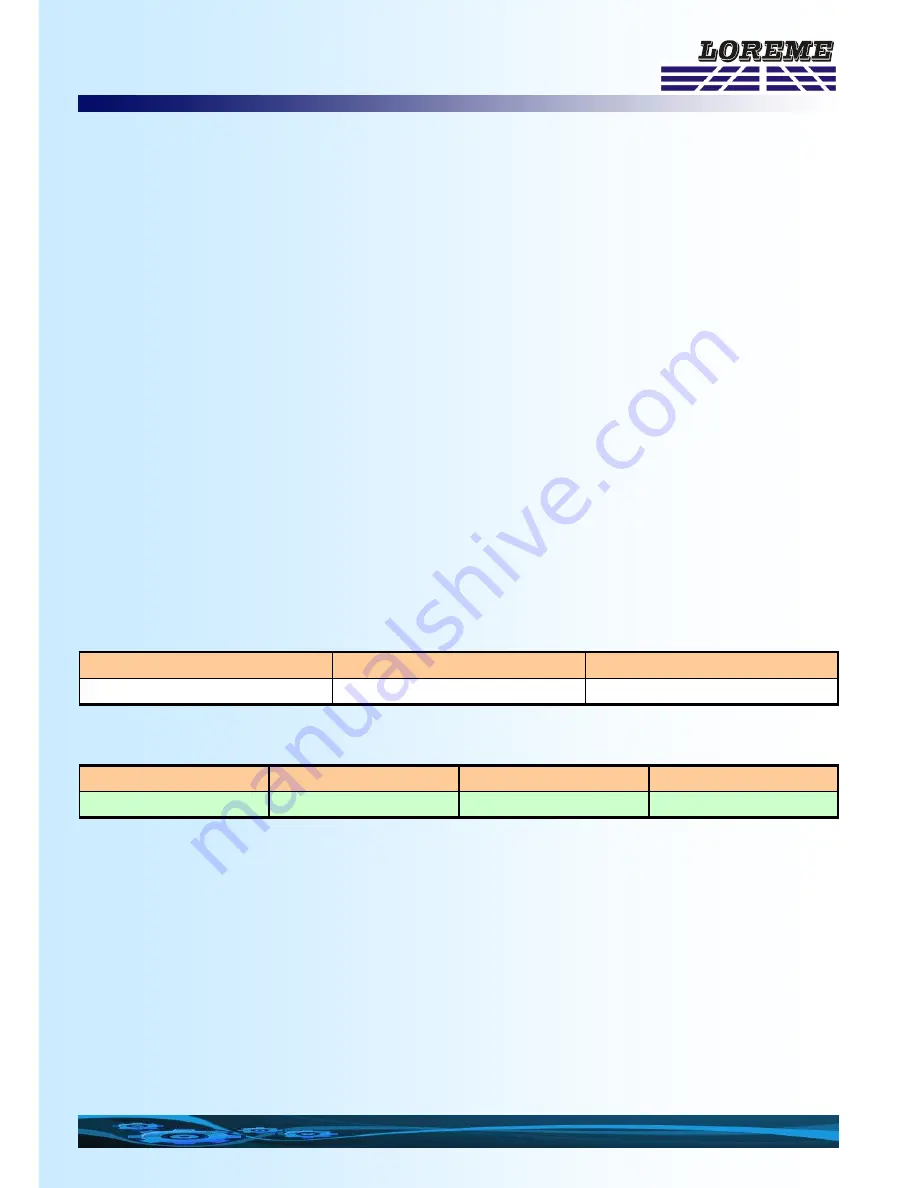
SOMMAIRE
E 7
5.2 proof interval
According table 2 from CEI 61508-1 the PFDavg ,for systems operating in low demand mode,
must be between ≥ 10
-3
and <10
-2
for SIL2 safety functions and between ≥ 10
-4
and <10
-3
for SIL3 safety functions .
T
[Proof]
= 1 year
T
[Proof]
= 5 years
T
[Proof]
= 10 years
T
[Proof]
= 20 years
PFD
avg=7.88E
-06
PFD
avg=3.94E
-05
PFD
avg=7.88E
-05
PFD
avg=1.57E
-04
temperature conditions 45°C
PFD
avg
value depending proof interval
λ
safe
λdangerous = PFH
SFF
305 FIT
1.8 FIT
99.4%
approximation : PFDavg =
λdangerous x T[Proof] /2 (error caused by approximation < 3%)
Fields marked in green means that the calculated values of PFDavg are within the limits allowed for SIL 3
Summary:
Fault probability PFD = 7.88 E
-6
x Tproof [year]
either for : Tproof = 10 years 8 % from SIF and for Tproof = 20 years 16 % from SIF in SIL3
Remarks :
- Test intervals should be determined according to the PFDavg required .
- The SFF , PFDavg and PFH must be determined for the entire safety instrumented function (SIF)
ensuring that the " out of range current values" are detected at system level and they actually lead to the safety position.
5 Commissioning and periodic proof
The periodic test procedure is defined by LOREME and must be followed by the end user to ensure and guarantee the SIL level over
time.
Periodic testing should be performed following the procedure defined below and at the intervals defined
under paragraph
" proof interval "
5.1 control steps
Periodic proof allows detection of possible product internal failure and loop calibration.
environmental conditions and a minimum heating time of 5 minutes must be respected.
Isolator test and complete output Loop control (
the system is unavailable during the test
)
1. If necessary, bypass the security system and / or take appropriate provision to ensure safety during the test.
2. Disconnect the current input transmitter.
3. Using a current simulation device (note 1), set the input current to high alarm value (≥ 21.0 mA).
4. Raise the front cover of device. With the TEST terminals and a milliammeter, check if each output current have this value /-
1%. (the green LED of each output is light off when the milliammeter is connected)
5. Set the input current to the low alarm value (≤ 3.6 mA)
6. Check if the signal from each output reaches this value /-1%
7. Set the output current to a median value (= 12 mA)
8. Check if the signal from each output reaches this value at +/-1% (linearity and transfer function check)
9. Remove the input simulator, close the front panel and connect the transmitter input .
10. Remove the bypass on the safety controller system or return to a normal operating condition
11. After testing, the results should be documented and archived.
Any device that does not satisfy the control needs to be replaced.
Note 1: The current generator must be calibrated (according to the state of the art and practice)
4-20mA signal isolator, signal splitter with 2,3,4 outputs
SIL2 / SIL3
CAL4/100ig CAL4/100igM