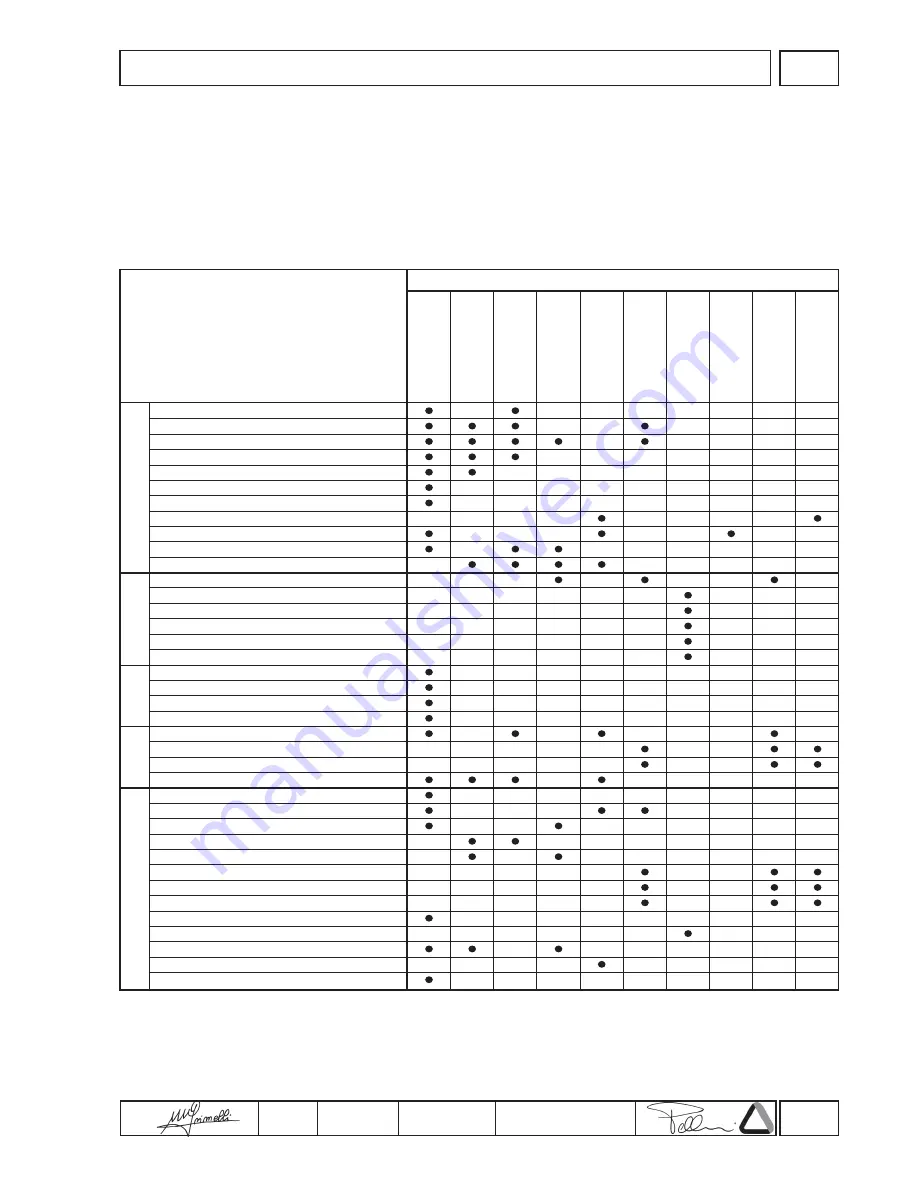
7
COMPILER TECO/ATI
ENDORSED
DATE
23.06.2003
REG. CODE
1-5302-607
MODEL N°
50889
DATE OF ISSUE
06-03
REVISION
00
I
TROUBLE SHOOTING
Clogged pipes
Clogged fuel filter
Air inside fuel circuit
Clogged tank breather hole
Faulty fuel pump
Injector jammed
Jammed injection pump delivery valve
Wrong injector setting
Excessive plunger blow-by
Jammed injection pump delivery control
Wrong injection pump setting
Oil level too high
Jammed pressure relief valve
Worn oil pump
Air inside oil suction pipe
Faulty pressure gauge or switch
Clogged oil suction pipe
Battery discharged
Wrong or inefficient cable connection
Defective ignition switch
Defective starter motor
Clogged air filter
Excessive idle operation
Incomplete running-in
Engine overloaded
Advanced injection
Delayed injection
Incorrect governor linkage adjustment
Broken or loose governor spring
Idle speed too low
Worn or jammed piston rings
Worn or scored cylinders
Worn valve guides
Jammed valves
Worn bearings
Governor linkage not free to slide
Drive shaft not free to slide
Damaged cylinder head gasket
TROUBLE
LUBRICATION
POSSIBLE CAUSE
FUEL CIRCUIT
ELECTRIC
SYSTEM
MAINTE- NANCE
SETTINGS/REPAIRS
POSSIBLE CAUSES AND TROUBLE SHOOTING
The following table contains the possible causes of some failures which may occur during operation. Always perform these
simple checks before removing or replacing any part.
Engine does not
start
No acceleration
Black smoke
Excessive oil
consumption
Too low oil
pressure
Engine starts but
stops
Non-uniform speed
White smoke
Oil and fuel
dripping from
exhaust
Increase oil level