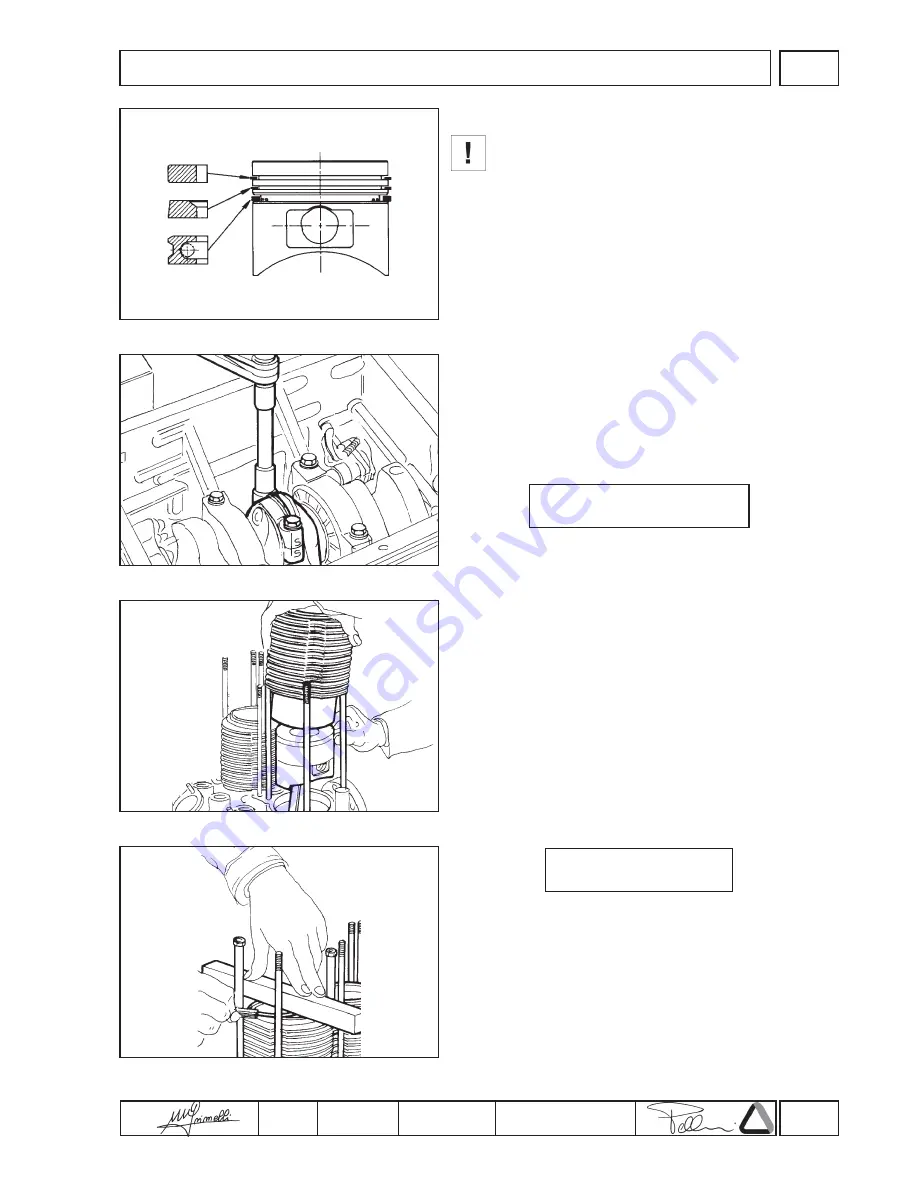
35
COMPILER TECO/ATI
ENDORSED
DATE
23.06.2003
REG. CODE
1-5302-607
MODEL N°
50889
DATE OF ISSUE
06-03
REVISION
00
XIII
73
74
75
76
0,10 ÷ 0,20 mm
kgm 3,6 ÷ 3,8 (Nm 35,3 ÷ 37,3)
ENGINE ASSEMBLY
Pistons
Lubricate the following parts with oil before mounting: the
piston pin, the piston, the cylinder and the big-end bearing
Fit the piston rings onto the pistons (fig.73) in the following order:
1. Chromed compression ring
2. Torsional compression ring (with internal bevel facing upward)
3. Expander oil scraper ring (external bevel facing upward).
Install the piston to the connecting rod, by pushind the wrist pin in,
without heading the piston.
Connecting rods
After having fitted the bearings into the big ends mount the
connecting rods to the crank journals pins; note that the pistons are
marked with an arrow showing the direction of rotation of the
engine. The combustion chamber, which is offset with respect to
the central axis of the piston, must be turned to face the injector
nozzle side. Mount the connecting rod big end cap ensuring that the
reference numbers are aligned with those punched on the
connecting rod itself (fig.74). Torque the bolts to:
Now fit the oil pan after first inserting the appropriate gasket
between the facing surfaces.
Cylinders
Before fitting the cylinders turn the piston rings so that the end gaps
are arranged at intervals of 120° with the end gap of the first
compression ring aligned with the axis of the wrist pin. The lower
face of the cylinders are chamfered to permit the easy insertion of
the piston rings. The operation can be simplified, however, using a
normal piston ring compressor (p.n. 00365R0770) as shown in
figure 75.
Mount the cylinders to the crankcase as shown in figure 76 and then
bring the pistons up to their respective TDC (top dead centre)
positions. The following must now be checked:
1. that the dots punched on the flywheel (TDC) correspond to the
reference mark on the flywheel-housing
2. that the pistons protrude over the top surface of the cylinders
(fig.76) by a distance of:
This distance is adjusted with special shims that are inserted
between the bottom surface of the cylinder and the crankcase
0.1 - 0.2 - 0.3 mm.