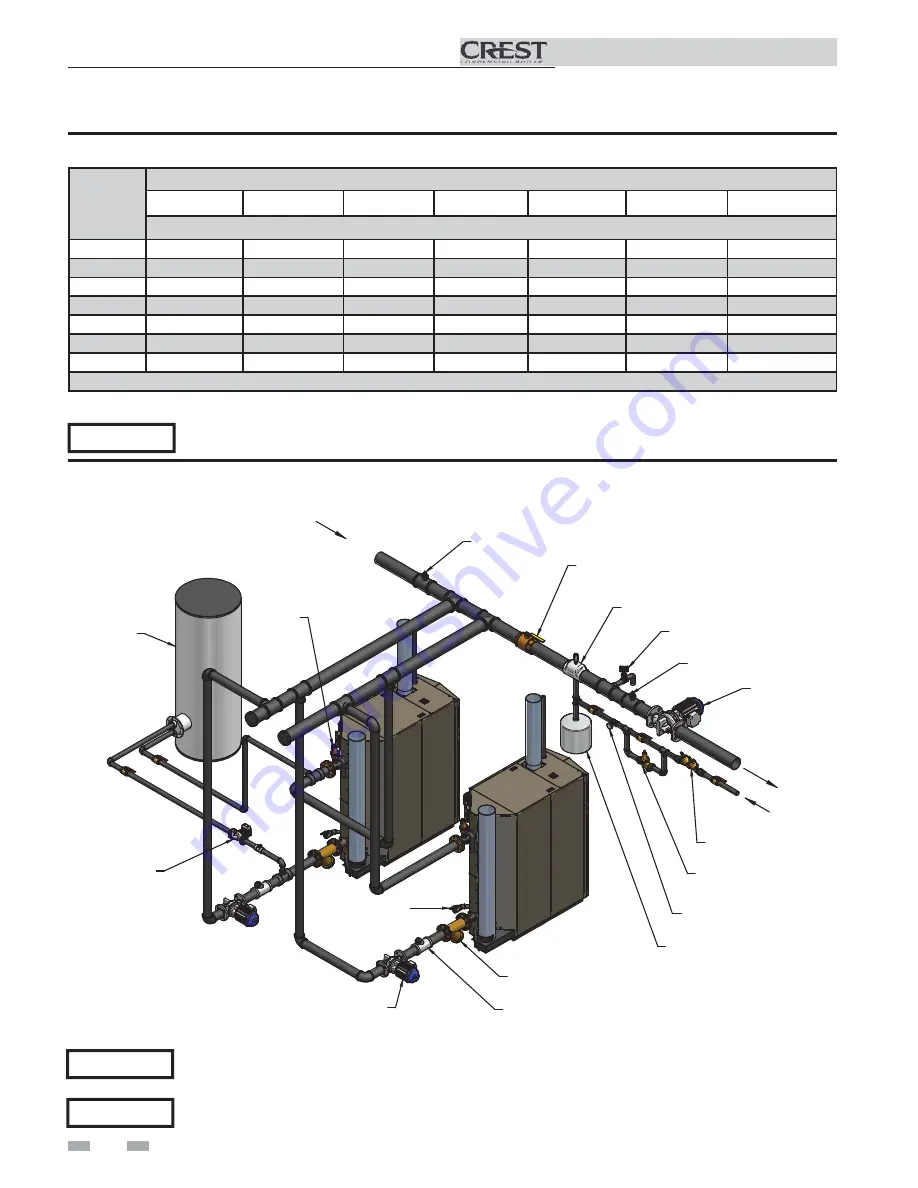
28
Installation & Operation Manual
5
Hydronic piping
Please note that these illustrations are meant to show system piping concept only, the installer is responsible
for all equipment. The installer must follow all manufacturer’s instructions for each system component. The
installer is responsible for compliance with local codes.
NOTICE
HOT WATER
GENERATOR
WATER
GENERATOR
CIRCULATOR
BOILER PUMP
(TYPICAL)
FLOW CHECK
VALVE (TYPICAL)
Y-STRAINER
(RECOMMENDED)
RELIEF
VALVE
BALL VALVE
(TYPICAL)
AIR SEPARATOR
DRAIN PORT
(TYPICAL)
SYSTEM
CIRCULATOR
BACK FLOW
PREVENTER
PRESSURE
REDUCING VALVE
PRESSURE
GAUGE
EXPANSION
TANK
FROM SYSTEM
TO SYSTEM
MAKE UP
WATER
BOILER DRAIN
(TYPICAL)
SYSTEM RETURN
SENSOR
SYSTEM SUPPLY
SENSOR
Figure 5-3 Multiple Boilers - Common Header - Recommended - Primary / Secondary Flow
Model
Number of Units
2
3
4
5
6
7
8
Recommended Common Header Pipe Sizes in Inches
FB 1500
4
4
5
5
6
6
7
FB 2000
4
5
5
6
7
7
8
FB 2500
5
5
6
7
7
8
10
FB 3000
5
6
7
7
8
10
10
FB 3500
5
6
7
8
10
10
10
FB 4000
6
6
8
8
10
10
12
FB 5000
6
8
8
10
10
12
12
NOTICE
A system supply sensor (factory supplied) MUST BE installed for proper boiler operation.
Table 5C Multiple Boilers - Common Header - Primary / Secondary Flow
System flow should always remain higher than the required flow for the boiler(s) when the boiler(s) is in
operation to prevent short cycling and high limit issues.
NOTICE
[Based on a boiler
Δ
T of 30°F.]
*
* See page 18 for special instructions when
common venting Crest boilers.