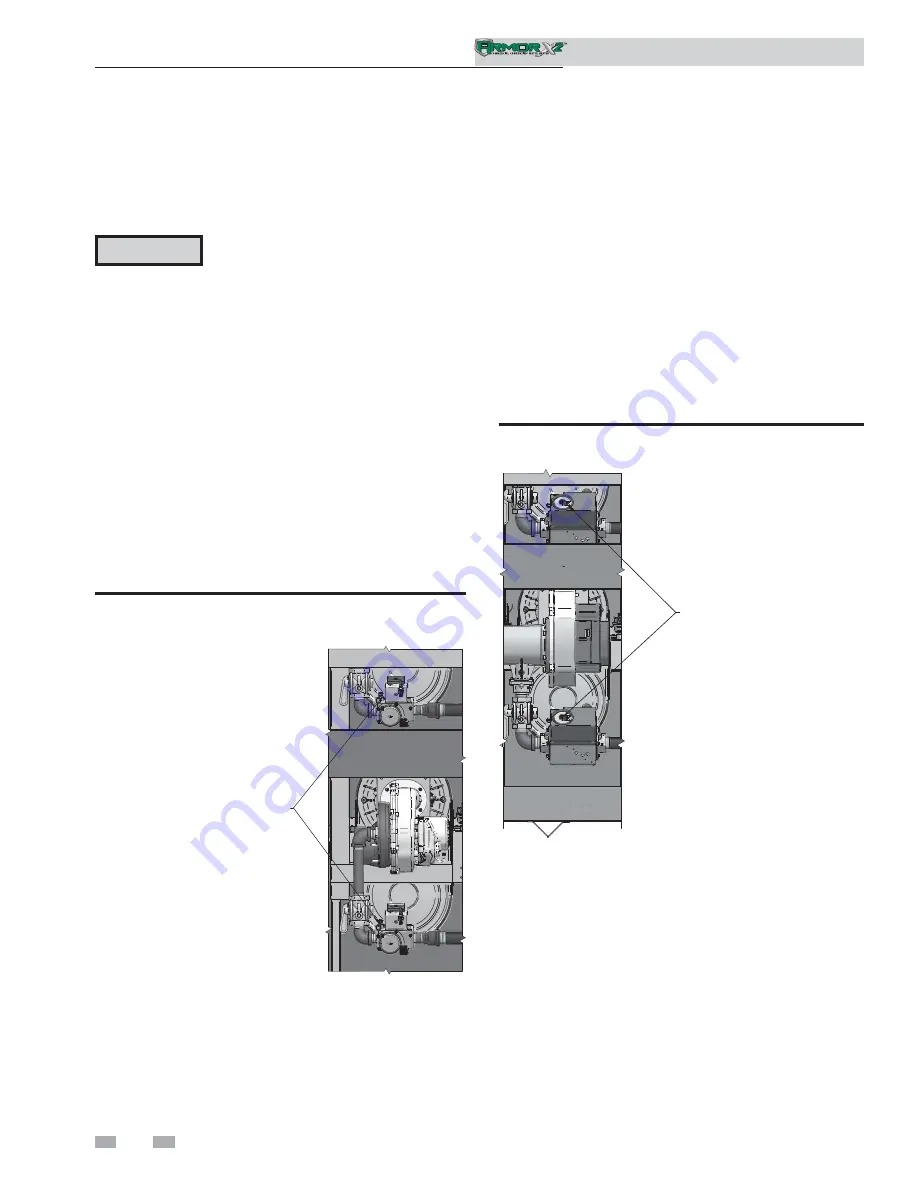
50
3
Troubleshooting
Gas valve adjustment procedure
If adjustment of the gas valve is deemed necessary, use the
following procedures: (
Note:
The procedures below are
model specific.)
THROTTLE ADJUSTMENT SCREW
Figure 3-2 Gas Valve Adjustment: Model 1.0
Model 1.0
Locate the throttle adjustment screw on top of the gas valve,
see FIG. 3-2. Using a screwdriver, turn the screw a 1/4 turn
counterclockwise
to increase CO
2
levels or a 1/4 turn
clockwise
to decrease CO
2
levels. After one adjustment on
the valve, follow the Combustion Analysis Procedure on
page 49 of this manual to measure the combustion.
If combustion is still not within the specified range,
repeat the procedure. This procedure SHOULD NOT
be performed more than four (4) times. If after four (4)
adjustments and the combustion is still not within the
specified range, revisit the possible causes in Table 3F on
page 49 or replace the gas valve.
CAUTION
Under normal operating conditions this
valve should not need adjusting.
Models 1.3 - 1.5
Locate the throttle adjustment screw on top of the gas valve,
see FIG. 3-3. Using an Allen wrench, turn the screw a 1/4
turn
counterclockwise
to increase CO
2
levels or a 1/4 turn
clockwise
to decrease CO
2
levels. After one adjustment on
the valve, follow the Combustion Analysis Procedure on page
49 of this manual to measure the combustion.
If combustion is still not within the specified range, repeat
the procedure. This procedure SHOULD NOT be performed
more than four (4) times. If after four (4) adjustments and
the combustion is still not within the specified range, revisit
the possible causes in Table 3F on page 49 or replace the gas
valve.
THROTTLE ADJUSTMENT
SCREW (REMOVE BLUE COVER)
Figure 3-3 Gas Valve Adjustment: Models 1.3 - 1.5
Service Manual
Содержание ArmorX2 1.0
Страница 5: ...1 Service The Armor X2 display 5 Service Manual...
Страница 51: ...Notes 51...
Страница 52: ...Revision Notes Revision A ECO C09645 initial release AWX2 SER Rev A 1 12...