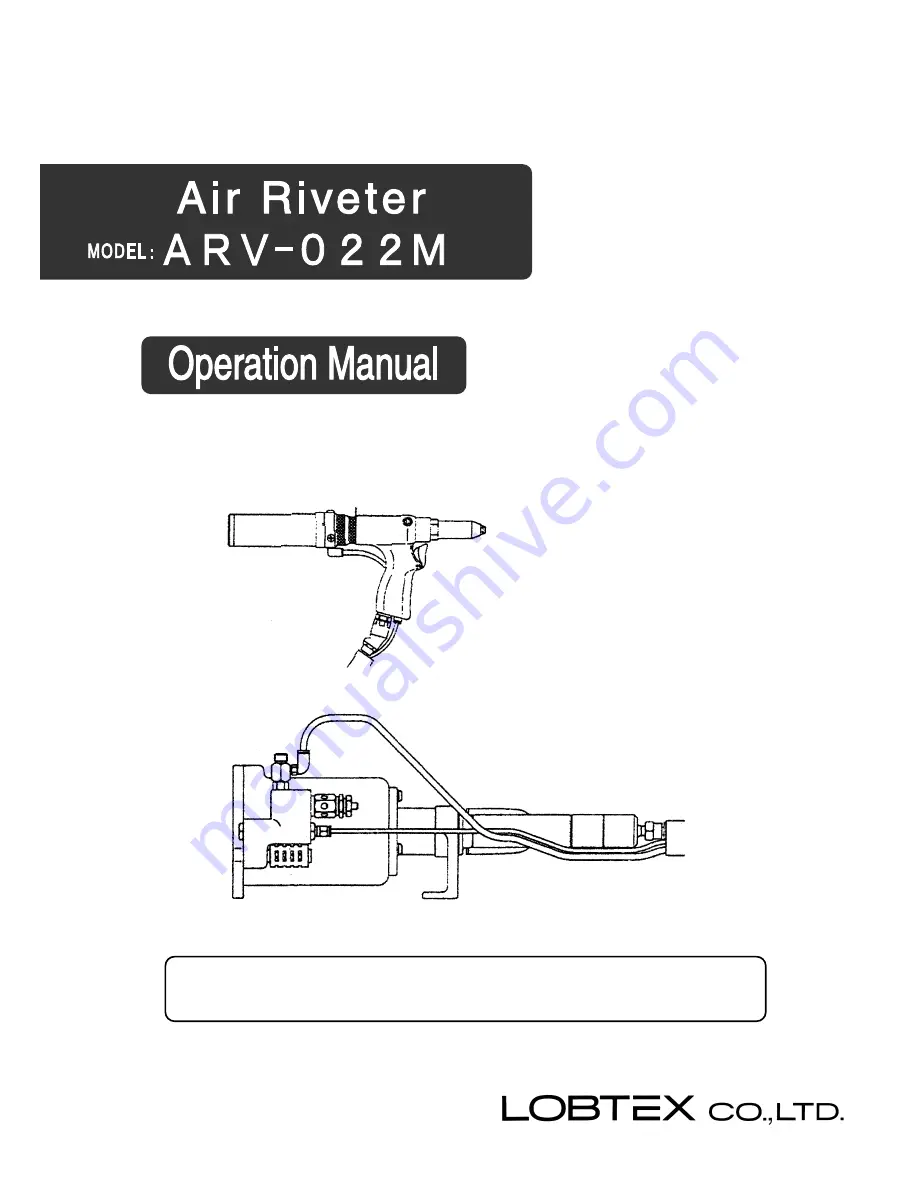
1
Be sure to read this manual before use.
Store this manual with care so that you can refer to it whenever necessary.
- CONTENTS -
1.
SAFETY
............................................... 3
1.1 WARNING SIGN ...................................... 3
1.2 SAFETY CONCERNS ............................... 3
1.3 SAFETY VALVE ....................................... 5
2.
NAME AND SPECIFICATION OF EACH PART
..... 6
3.
PREPARATION BEFORE USE
.............. 7
4.
HOW TO RIVET
.................................... 9
5.
CLEANING AND MAINTENANCE
..........10
5.1 FRAME HEAD AND JAW CASE UNIT ............10
5.2 SPOOL UNIT ..........................................11
5.3 CYLINDER UNIT ......................................12
5.4 CHECKING HYDRAULIC OIL ......................13
5.4 DISCONNECTING HYDRAULIC COUPLER ....1 4
5.5 NOZZLE UNIT .........................................15
6.
TROUBLESHOOTING
...........................16
7.
PART DRAWINGS
.................................17
7.1 HEAD AREA ...........................................17
7.2 SWIVEL UNIT AND BOOSTER UNIT .............19
8.
STORAGE / ORDERING PARTS
...........20