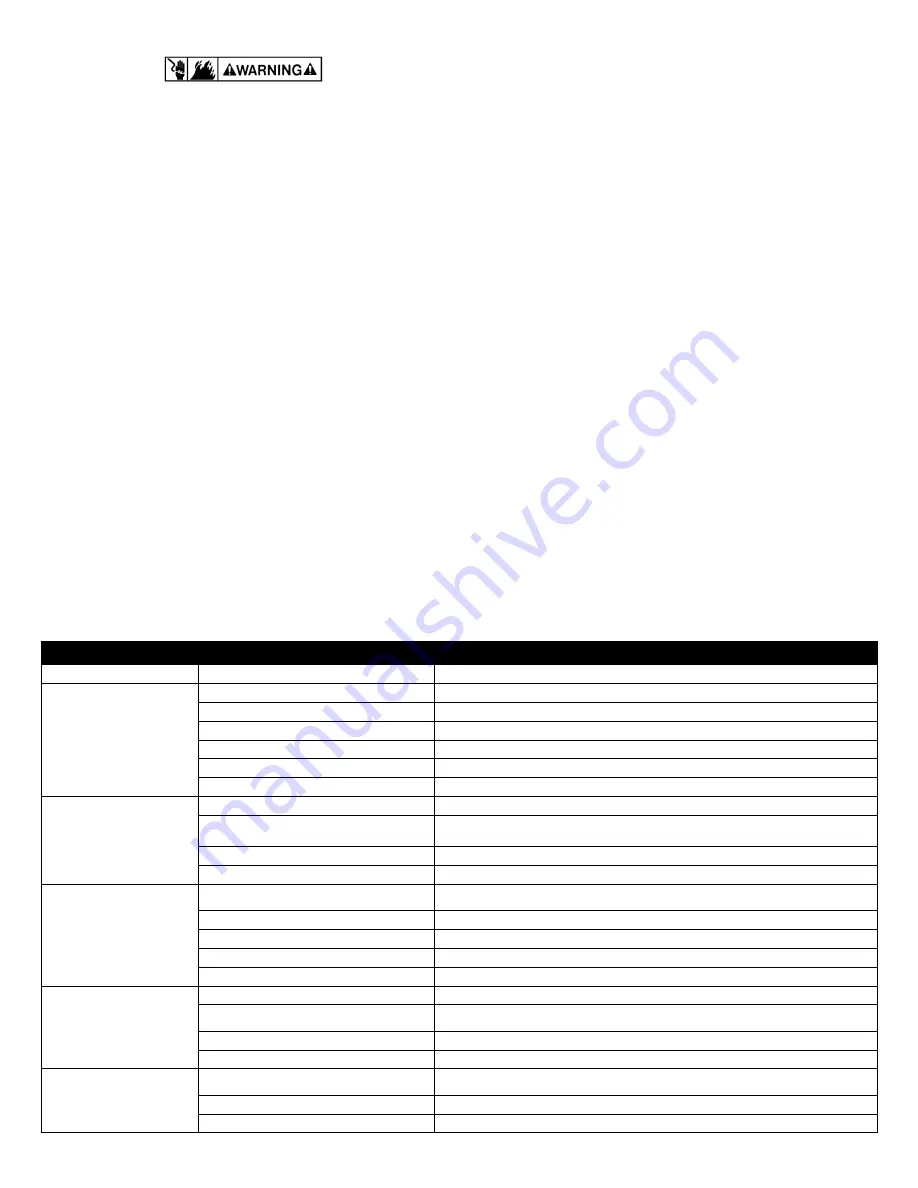
3
TROUBLESHOOTING
PROBLEM
PROBABLE CAUSES
CORRECTIVE ACTION
Pump does not turn on.
Pump not plugged in.
Plug in pump.
Circuit breaker shut off or fuse removed.
Turn on circuit breaker or replace fuse.
Accumulation of trash on float.
Clean float.
Float obstruction.
Check float path and provide clearance.
Defective switch.
Have pump serviced by authorized service center.
Defective motor.
Have pump serviced by authorized service center.
Pump will not shut off.
Float or float rod obstruction.
Check float and float rod path and provide clearance.
Pump is air locked.
Shut power off for approximately 1 minute, then restart. Repeat several times to
clear air from pump.
Liquid inflow matches pump capacity.
Larger pump required.
Defective switch.
Disconnect switch, check w/ohmmeter, Open-infinitive resistance, closed-zero.
Pump runs but does not
discharge liquid.
Check valve installed backwards.
Check flow indicating arrow on check valve body to ensure it is installed
properly.
Check valve stuck or plugged.
Remove check valve and inspect for proper operation.
Lift too high for pump.
Check rating table.
Inlet to impeller plugged.
Pull pump and clean.
Pump is air locked.
(See corrective action above.)
Pump does not deliver
rated capacity.
Lift too high for pump.
Check rated pump performance.
Low voltage, speed too slow.
Check for proper supply voltage to make certain it corresponds to nameplate
voltage.
Impeller or discharge pipe is clogged.
Pull pump and clean. Check pipe for scale or corrosion.
Impeller wear due to abrasives.
Replace worn impeller.
Pump cycles continually.
No check valve in long discharge pipe
allowing liquid to drain back into basin.
Install a check valve in discharge line.
Check valve leaking.
Inspect check valve for correct operation.
Basin too small for inflow.
Install larger basin.
MAINTENANCE
WARNING:
DISCONNECT THE PUMP FROM THE POWER SOURCE
BEFORE ATTEMPTING TO SERVICE OR REMOVE ANY
COMPONENT!
1. This unit is permanently lubricated. Oiling is not required. Do
not, in any case, open the sealed portion of the unit or remove
housing screws.
2. Periodic cleaning of the pump parts will prolong the LIFE and
EFFICIENCY of the pump.
3. Remove screws that hold base to volute and clean impeller and
volute passage. Do not use strong solvents on impeller.
4. Be sure impeller turns freely after cleaning.
5.
CAUTION:
DO NOT REMOVE IMPELLER. THIS REQUIRES
SPECIAL TOOLS AND IS TO BE DONE ONLY BY AN
AUTHORIZED SERVICE CENTER. DO NOT REMOVE MOTOR
HOUSING COVER. WARRANTY IS VOID IF MOTOR HOUSING
COVER, IMPELLER OR SEALS HAVE BEEN REMOVED. ANY
REPAIR ON MOTOR MUST BE DONE BY AN AUTHORIZED
LITTLE GIANT SERVICE CENTER.
6. Be certain power cord is in good condition and contains no
nicks or cuts.