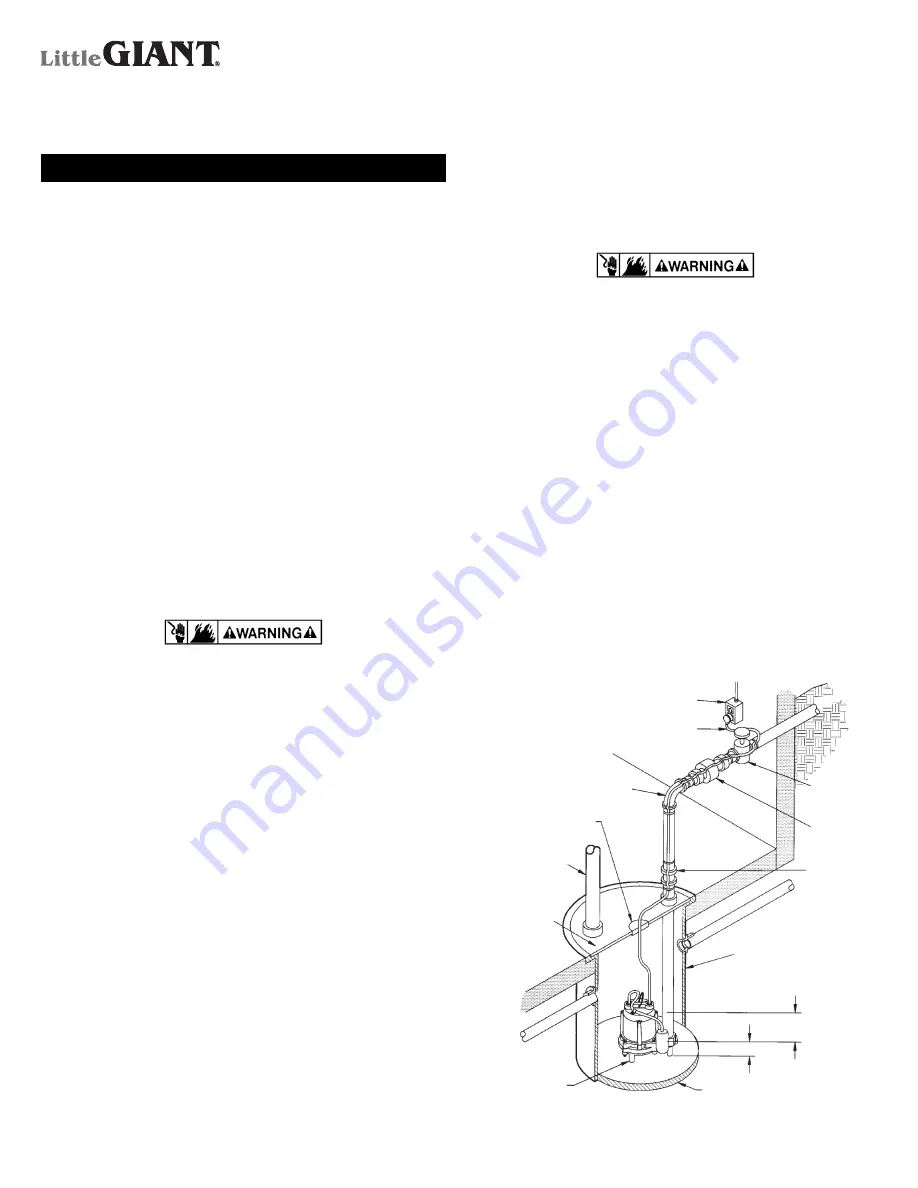
1
HT-6E-CIA-FS
SUBMERSIBLE
EFFLUENT PUMP
INTRODUCTION
This instruction sheet provides you with the information required to
safely own and operate your product. Retain these instructions for
future reference.
The product you have purchased is of the highest quality
workmanship and material, and has been engineered to give you
long and reliable service. This product has been carefully tested,
inspected, and packaged to ensure safe delivery and operation.
Please examine your item(s) carefully to ensure that no damage
occurred during shipment. If damage has occurred, please contact
the place of purchase. They will assist you in replacement or repair,
if required.
READ THESE INSTRUCTIONS CAREFULLY BEFORE
ATTEMPTING TO INSTALL, OPERATE, OR SERVICE
YOUR PRODUCT. KNOW THE PRODUCT’S APPLICATION,
LIMITATIONS, AND POTENTIAL HAZARDS. PROTECT
YOURSELF AND OTHERS BY OBSERVING ALL SAFETY
INFORMATION. FAILURE TO COMPLY WITH THESE
INSTRUCTIONS COULD RESULT IN PERSONAL INJURY AND/
OR PROPERTY DAMAGE!
DESCRIPTION
This is a submersible effluent pump for use in basins or lift stations,
and is suitable for pumping effluent, wastewater, and other non-
explosive, non-corrosive liquids with up to 1/2” spherical solids and
temperatures up to 200°F.
SAFETY GUIDELINES
CAUTION: INTENDED FOR COMMERCIAL AND INDUSTRIAL
USE ONLY. READ SAFETY GUIDELINES AND INSTRUCTIONS
CAREFULLY.
1. Do not use to pump flammable or explosive fluids such as
gasoline, fuel oil, kerosene, etc. Do not use in explosive
atmospheres or hazardous locations as classified by NEC,
ANSI/NFPAT. Pump should only be used with liquids compatible
with pump component materials.
2. Do not handle pump with wet hands or when standing on a wet
or damp surface, or in water.
3. Do not pull the pump out of the water by the power cord when
the pump is operating or connected to power source.
4. This pump is supplied with a grounding conductor and/or
grounding type attachment plug. To reduce the risk of electric
shock, be certain that it is connected to a properly grounded
grounding type receptacle.
5. The National Electric Code requires a ground fault circuit
interrupter (GFCI) be installed in the branch circuit supplying
fountain equipment, pools, etc.
6. In any installations where property damage and/or personal
injury might result from an inoperative or leaking pump due to
power outages, discharge line blockage, or any other reason, a
backup system(s) and/or alarm should be used.
7. Support pump and piping when assembling and when installed,
failure to do so may cause piping to break, pump to fail, motor
bearing failures, etc.
8. This pump’s motor housing is filled with a dielectric oil for motor
heat transfer and life-time lubrication of the bearings. This oil is
non-toxic to aquatic life, however, suffocation can occur if oil is
left on the water surface. If oil escapes the motor housing, it can
be removed from the surface quickly by placing newspapers on
the water surface to soak up the oil.
9. The pump motor is equipped with an automatic resetting thermal
protector and may restart unexpectedly. Protector tripping is an
indication of motor overloading as a result of excessively high or
low voltage, inadequate wiring, incorrect motor connections, or
a defective motor or pump.
ELECTRICAL CONNECTIONS
1. Check the pump label for proper voltage required. Do not
connect to voltage other than that shown.
2. If pump is supplied with a 3-prong electrical plug, the third
prong is to ground the pump to prevent possible electrical
shock hazard. DO NOT REMOVE the third prong from the plug.
A separate branch circuit is recommended. Do not use an
extension cord.
3. If the cord is equipped with stripped lead wires, such as on 230V
models, be sure that the lead wires are connected to a power
source correctly. The green/yellow wire is the ground, the other
two are live.
4. Check local electrical and building codes before installation.
The installation must be in accordance with their regulations as
well as the most recent National Electrical Code (NEC).
5. To conform to the National Electrical Code, all pumps must be
wired with 14 AWG or larger wire. For runs to 250 feet, 14 AWG
wire is sufficient. For longer runs, consult a qualified electrician
or the factory.
6. Pump should be connected or wired to its own circuit with no
other outlets or equipment in the circuit line. Fuses and circuit
breaker should be of ample capacity in the electrical circuit.
Franklin Electric Co., Inc.
P. O. Box 12010
Oklahoma City, OK 73157-2010
405.947.2511 • Fax: 405.947.8720
www.LittleGiantPump.com
Discharge pipe no smaller than pump outlet
Power Cord Grommet
2" or 3" Vent Pipe
Basin Cover
Pump
Union
Check Valve
Gate Valve
Place pump on hard level surface. Never place
directly on clay, earth or gravel surface.
11"–14" on level
3"–6" off level
Gas Tight Basin 18" dia. x 24" deep min.
Separate protected and grounded service outlet 4' from floor min.
Pump Power Cord
Figure 1