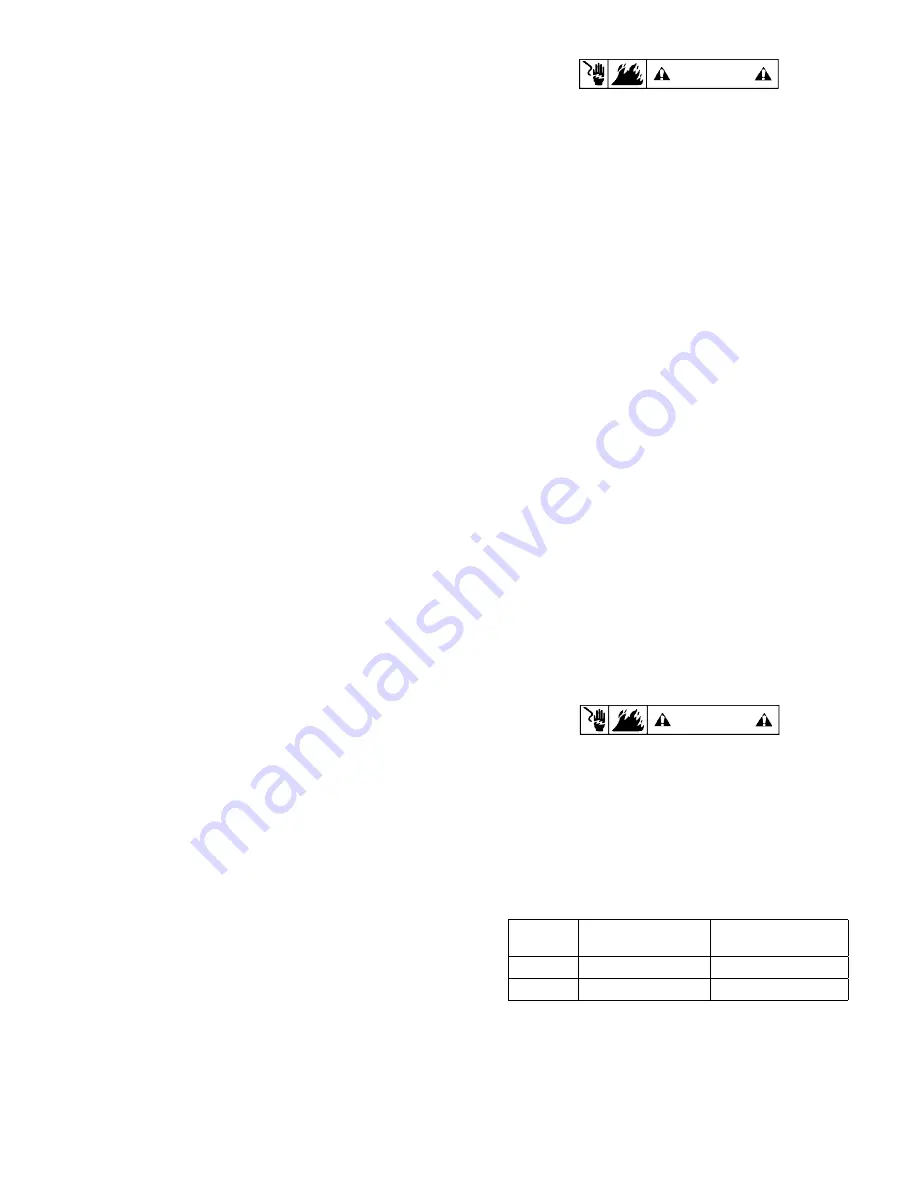
house, or call your local fire department for instructions. Failure to
follow this warning can result in fatal electrical shock.
Do not modify the power cord except to shorten it to fit into a
control panel. Any splice between the pump and the control panel
must be made within a junction box and mounted outside of the
basin, and comply with the National Electrical Code. Do not use
the power cord for lifting the pump.
The pump motor is equipped with an automatic-resetting, thermal
protector and may restart unexpectedly. Protector-tripping is an
indication of motor overloading as a result of operating the pump
at low heads (low discharge restriction), excessively high or low
voltage, inadequate wiring, incorrect motor connections, or a
defective motor or pump.
Do not use to pump flammable or explosive fluids such as
gasoline, fuel oil, kerosene, etc. Failure to follow this warning can
result in personal injury and/or property damage.
During normal operation the pump is immersed in water. Also,
during rain storms, water may be present in the surrounding area
of the pump. Use caution to prevent bodily injury when working
near the pump:
Remove the plug from the receptacle before touching, servicing,
or repairing the pump.
To minimize possible fatal electrical shock hazard, use extreme
care when changing fuses. Do not stand in water while changing
fuses or insert your fingers into the fuse socket.
Do not operate the pump in a dry basin. This will cause the
pump to become extremely hot, causing burns if touched and/or
damage to the pump.
Do not oil the motor. The pump housing is sealed. A high grade
dielectric oil devoid of water has been put into the motor housing
at the factory. Use of other oil could cause serious electric shock
and/or permanent damage to the pump.
Do not install the pump in locations classified as hazardous in
accordance with the National Electrical Code, ANSI/NFPA 70.
In any installation where property damage and/or personal injury
might result from inoperative or leaking pump due to power
outages, discharge line blockage, or any other reason, use a
backup system(s) and/or alarm.
SPECIFICATIONS
DISCHARGE:
14EH and 16EH – 2”, 14S – 2” or 3”, 16S – 3”
HANDLING CAPABILITIES:
EH Series – 3/4” spherical solids,
S Series – 2” spherical solids
HOUSING:
Cast iron
VOLUTE:
Cast iron
IMPELLER:
Non-clog, cast iron with pressure relief vanes
MOTOR:
PSC, 3450 RPM (EH Series), 1625 RPM (S Series), with
automatic overload protection
HARDWARE:
300-series stainless steel
BEARING:
Ball
SHAFT SEAL:
Mechanical, spring-loaded, rotating carbon with
Nitrile boot and stationary ceramic seat, with secondary Nitrile
exclusion seal
POWER CORD:
16 AWG, 3-conductor, copper stranded; 18 AWG
(208-240V models)
COOLING:
The motor housing contains oil to cool the motor
and to lubricate the bearings and seals. For the best cooling and
longest motor life, however, the level of the liquid being pumped
should be above the top of the motor housing.
INSTALLATION
WARNING
For automatic operation, plug or wire the pump into a float switch
or liquid level controller. Installation instructions are included with
all Little Giant switches and controllers and should be referred to
for installation.
The pump will run continuously when plugged directly into an
electrical outlet. Take care to prevent the pump from running in
a dry sump.
Install the pump in a suitable, gas-tight basin that is at least 18”
in diameter and 30” deep, and vented in accordance with local
plumbing codes.
Place the pump on a hard, level surface. Never place the pump
directly onto clay, earth, or gravel surfaces.
The pump can be installed with ABS, PVC, polyethylene, or
galvanized steel pipe. Proper adapters are required to connect
plastic pipe to the pump.
To facilitate pump removal (if necessary), install a union just
above the cover.
Use a check valve in the discharge line to prevent backflow of
liquid into the basin. This should be a free-flow valve that will easily
pass solids.
CAUTION:
For best performance of check valves, when handling
solids install the valve horizontally or at an angle of no more than
45°. Do not install the valve vertically, as solids may settle in the
valve and prevent opening on start-up.
A gate valve should follow the check valve to allow periodic
cleaning of the check valve or removal of the pump.
The remainder of the discharge line should be as short as
possible with a minimum of turns to minimize friction head loss.
Do not restrict the discharge to sizes below 2”.
Sewage and effluent applications require a separate sump
vent. A connection is provided on top of the sump or cover.
This connection must be piped to the existing building vent or
extended outside with its own standpipe.
WIRING
WARNING
Check local electrical and building codes before installation. The
installation must be in accordance with their regulations as well as
the most recent National Electrical Code (NEC).
To conform to the National Electrical Code, all pumps must be
wired with 14 AWG or larger wire. For runs to 250 feet, 14 AWG
wire is sufficient. For longer runs, consult a qualified electrician
or the factory.
Connect or wire the pump to its own circuit, with no other outlets
or equipment in the circuit line. Fuses and circuit breaker should
be of ample capacity in the electrical circuit. See Table 1.
H.P.
VOLTAGE
FUSE OR CIRCUIT
BREAKER AMPS
½, 1
115
20
½, 1
230
15
TABLE 1
2
PumpAgents.com - Click here for Pricing/Ordering
PumpAgents.com - Click here for Pricing/Ordering