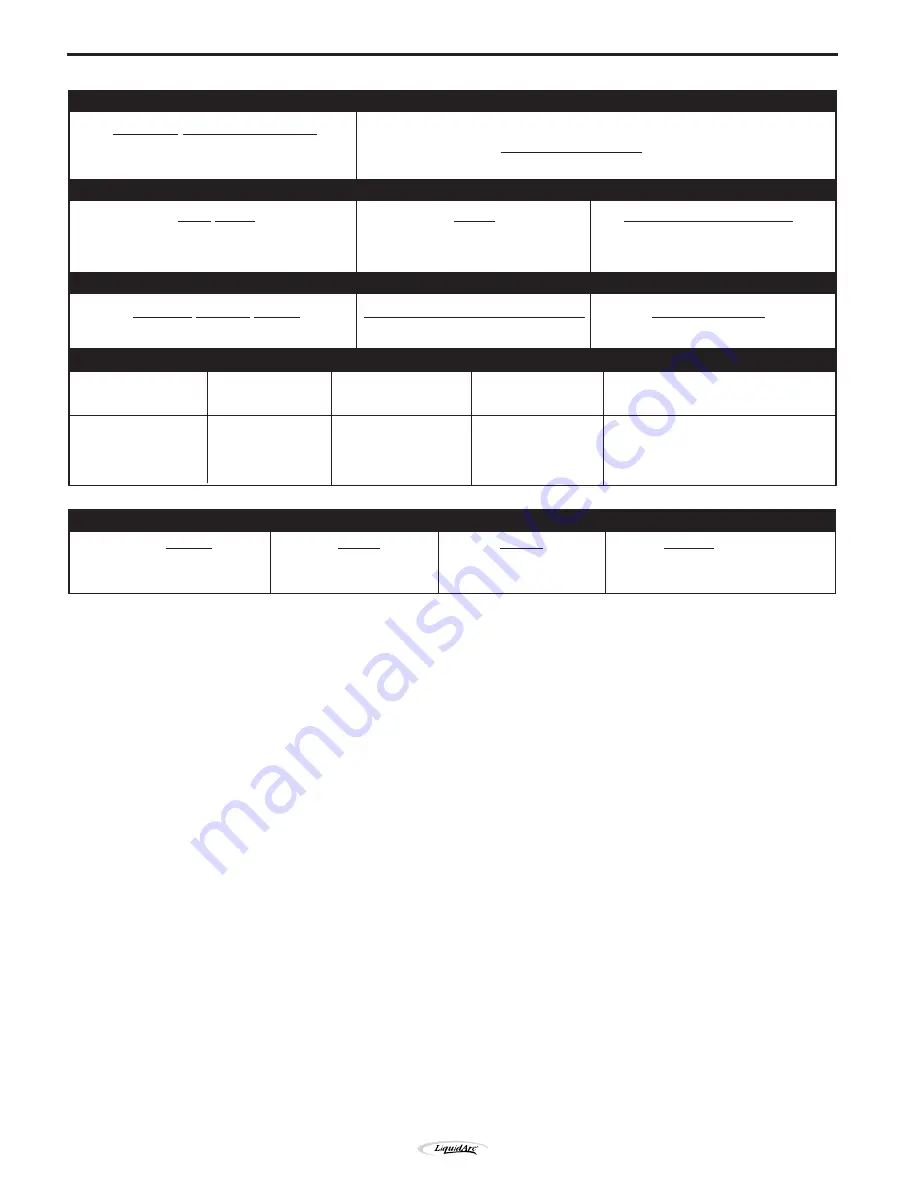
A-1
A-1
INSTALLATION
Fuse or
Output Mode
Input Voltage
Breaker Size
Input Amps
Power Cord
RATED
240V/50Hz
25 Super Lag
12.7
15Amp, 240V,
Three Pin Plug
TECHNICAL SPECIFICATIONS – Handymig 170i
INPUT – SINGLE PHASE ONLY
RATED OUTPUT
OUTPUT
RECOMMENDED INPUT CABLE AND FUSE SIZES
Height
Width
Depth
Weight
305 mm
248 mm
419 mm
25.9 kg
PHYSICAL DIMENSIONS
Standard Voltage/Frequency
AS
1966.1
240V/50Hz
Rated Input Current
12.7 Amps
Duty Cycle
Amps
Volts at Rated Amperes
20%
130
20
Welding Current Range
Maximum Open Circuit Voltage
Auxiliary Power
Rated DC Output: 30 – 170 amps
33
N/A
Handymig 170i
Содержание Handymig 170i
Страница 22: ...B 7 B 7 APPLICATION CHART Handymig 170i ...
Страница 32: ...NOTES ...
Страница 33: ...NOTES ...