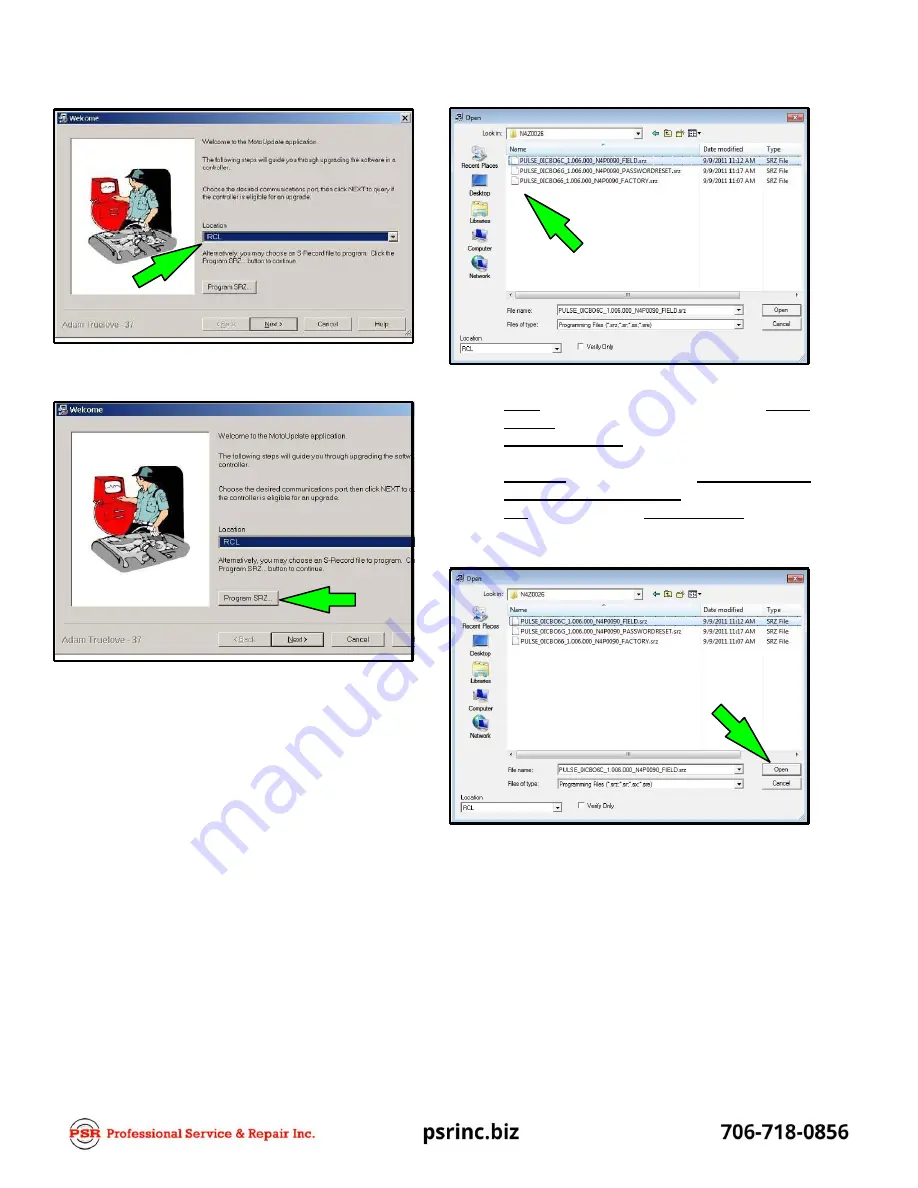
24.
Select the programming location for “RCL”.
26.
Select the file to be programmed.
a.
FIELD – use this file to update software. No cal-
ibration required.
b.
PASSWORDRESET – use this file to reset the
default factory passwords.
c.
FACTORY – use this file when directed to do so
by the version description. This file will erase
ALL calibration data. Full calibration will be re-
quired.
25.
Click the “Program SRZ” button.
27.
Click “Open”.
Содержание PULSE
Страница 2: ......
Страница 3: ......
Страница 4: ...Link Belt Pulse Calibration Manual ...
Страница 21: ...beams ...
Страница 48: ...piston pressures and the number on the right for ...
Страница 61: ...22 Use the left mouse button to click on the Start button ...