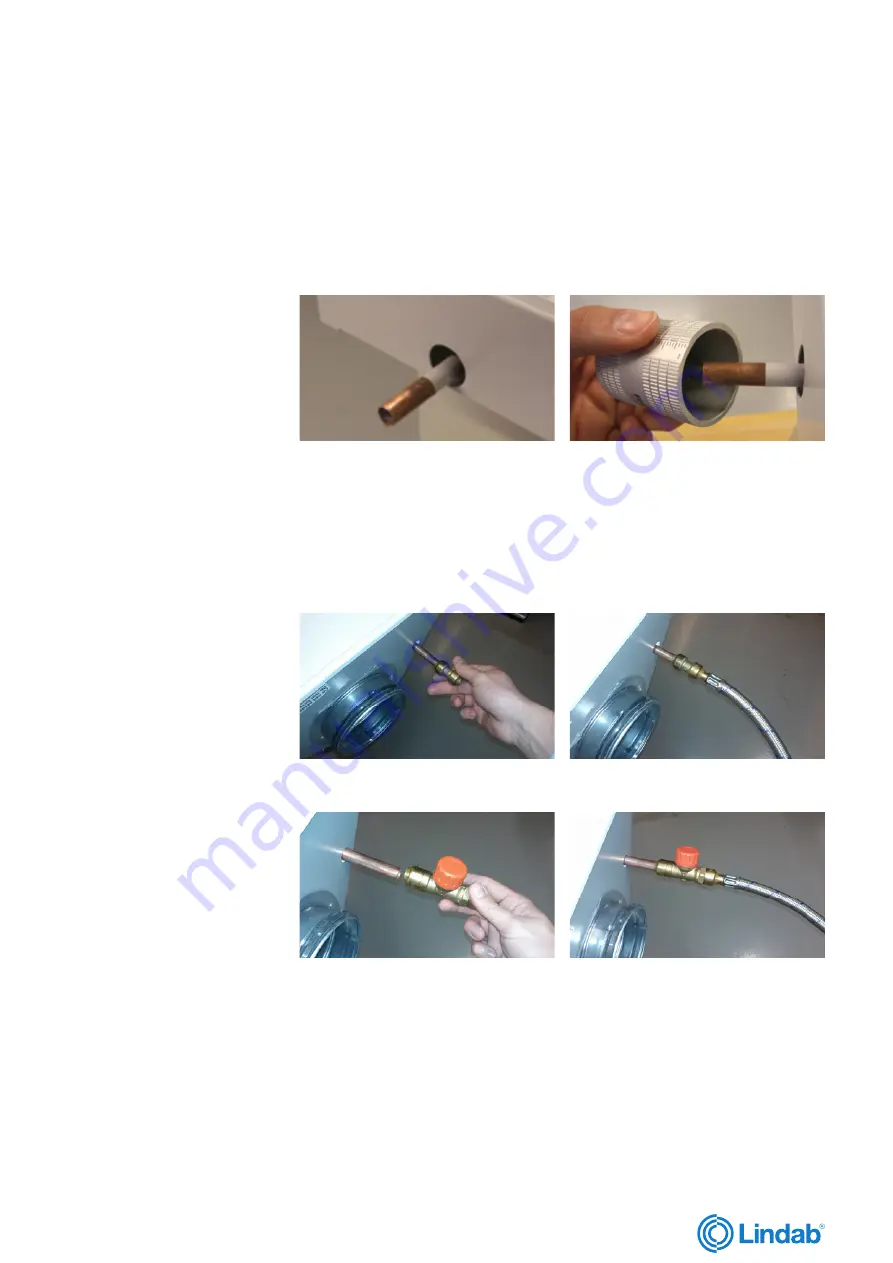
6
lindab | we simplify construction
Service & maintenance Celo
Lindab reserves the right to make changes without prior notice
2021-04-15
Lindab reserves the right to make changes without prior notice
2021-04-15
After removing the protection cover, make sure that the pipe is intact and undam-
aged, especially at the pipe end. Crocked or in other ways imperfect pipe ends will
result in leaks. Deburr the pipe on the inside and the outside, using a deburring tool
before installation
– Mount a push-on fitting to the pipe. Make sure to press the fitting all the way onto
the pipe. After mounting the push-on fitting, mount the flexible hose. Make sure
that the flexible hose is pushed fully into the fitting. Consult the installation guide
for the specific fitting for further details on proper installation.
Push-on fitting
Push-on valve
Notice!
The connection pipes are internally soft-welded why it’s not allowed to
solder the beam to the pipes.