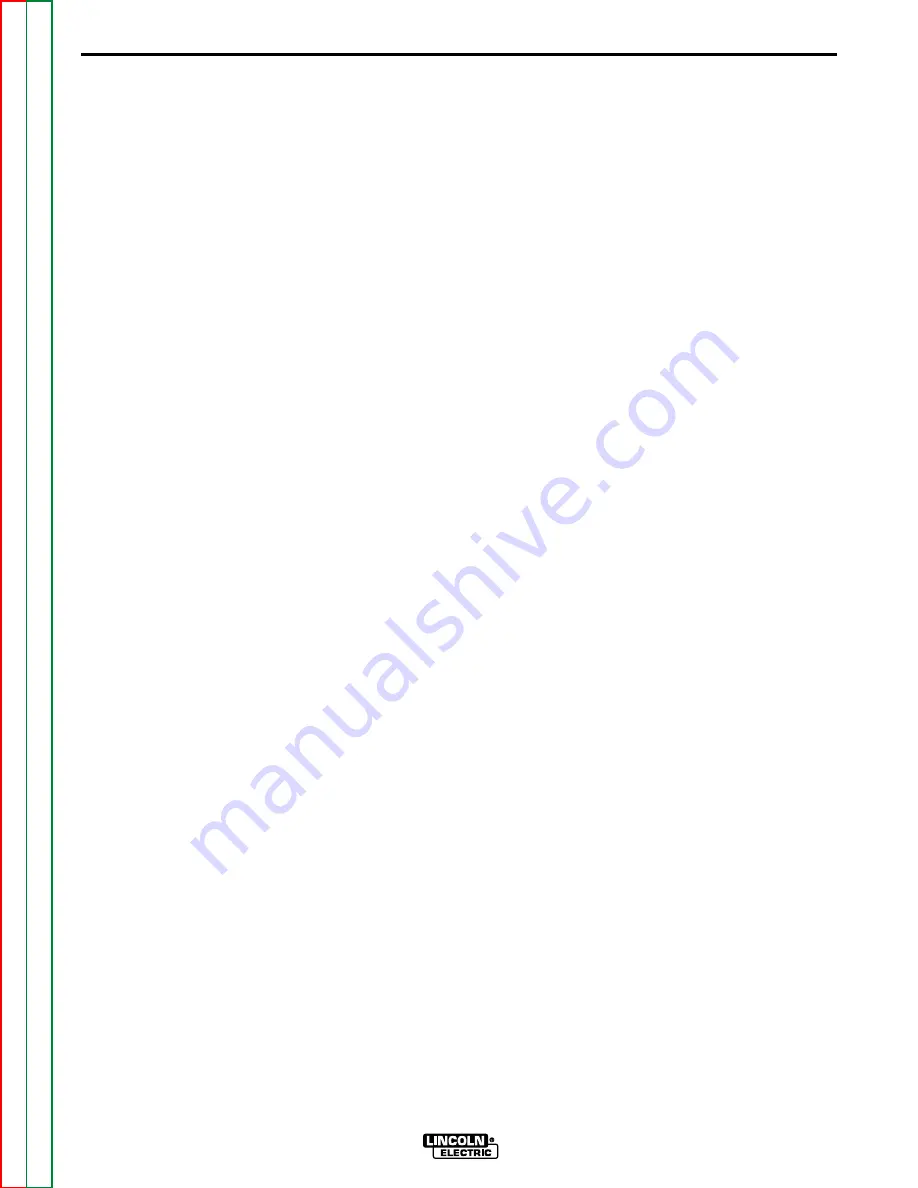
B-9
OPERATION
B-9
LN-10
Maximum and Minimum Limits Setting
Modes
Limits setting modes are available for limiting the
range for setting wire feed speed and voltage. The
limits can be set independently for each procedure.
The following steps should be followed for setting the
maximum and minimum limits:
1. Turn off the power at the power source.
2. Remove the two screws at the top of the LN-10
control box and open the control box door.
3. Put DIP switch S2 switch 5 in the ON position.
4. Close the control box door.
5. Turn on the power at the power source.
6. Set the maximum WFS and voltage limits for pro-
cedure A and procedure B using the two encoder
knobs and the procedure key. The maximum WFS
limit can be set for the entire range of the wire
drive that is being used. The maximum voltage
limit can be set over the range of 10.0 to 60.0 volts.
The maximum limits can be turned off indepen-
dently for each procedure by turning the encoder
knobs clockwise until the appropriate display (WFS
or voltage) reads “OFF” while the correct proce-
dure light is lit. (The limits are set to “OFF” from
the factory.
7. Turn off the power at the power source.
8. Open the control box door.
9. Put DIP switch S2 switch 5 in the OFF position and
DIP switch S2 switch 6 in the ON position.
10. Close the control box door.
11. Turn on the power at the power source.
12. Set the minimum WFS and voltage limits for pro-
cedure A and procedure B using the two encoder
knobs and the procedure key. The minimum WFS
limit can be set from the minimum speed of the
wire drive that is being used to the maximum limit
that has been set for the selected procedure. The
minimum voltage limit can be set over the range of
10.0 to the maximum voltage limit that has been
set for the selected procedure. The minimum lim-
its can be turned off independently for each proce-
dure by turning the encoder knobs counter clock-
wise until the appropriate display (WFS or voltage
reads “OFF” while the correct procedure light is
lit. (The limits are set to “OFF” from the factory).
13. Turn off the power at the power source.
14. Open the control box door.
15. Put DIP switch S2 switch 6 in the OFF position.
16. Close the control box door.
17. Reinstall the two screws that had previously been
removed in step 2.
Return to Section TOC
Return to Section TOC
Return to Section TOC
Return to Section TOC
Return to Master TOC
Return to Master TOC
Return to Master TOC
Return to Master TOC