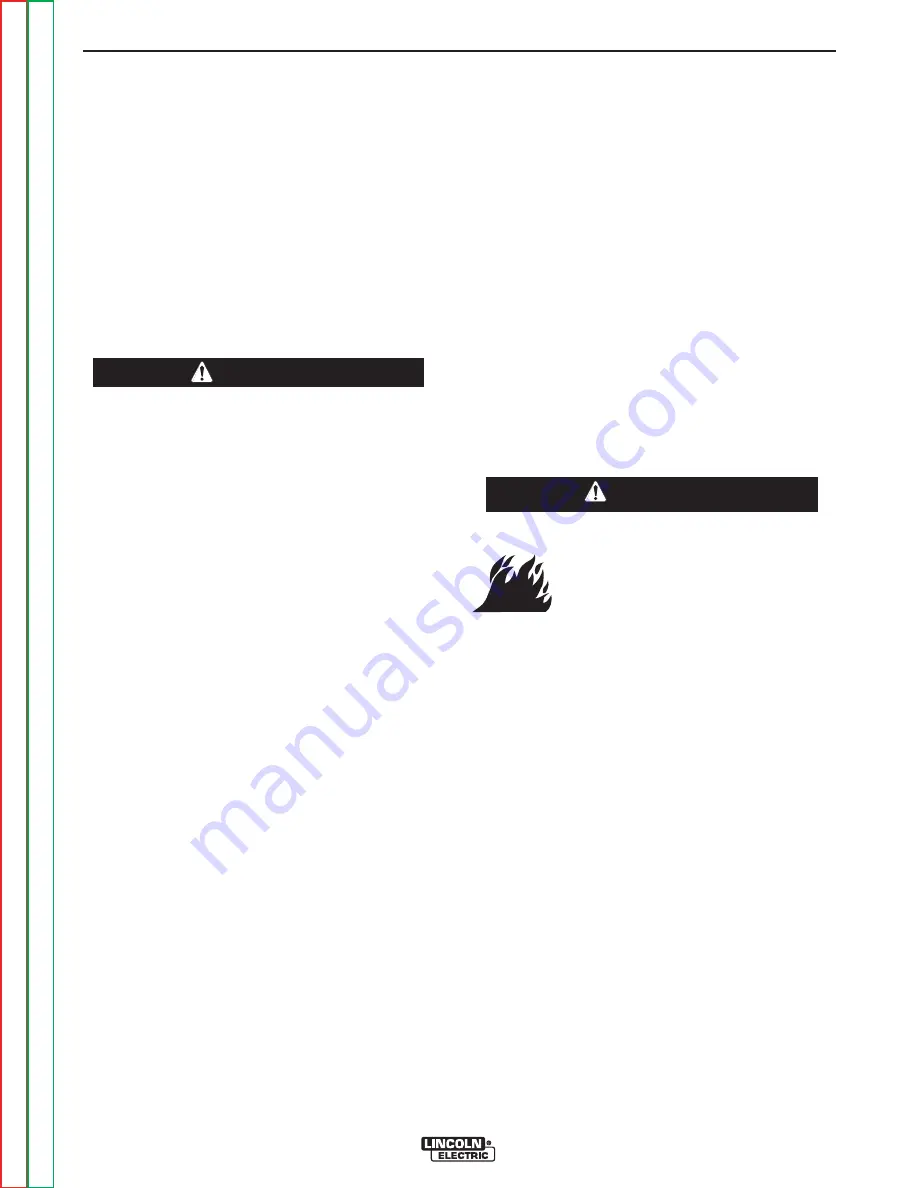
MAINTENANCE
D-3
D-3
SAE-400 SEVERE DUTY
Return to Section
T
OC
Return to Section
T
OC
Return to Section
T
OC
Return to Section
T
OC
Return to Master
T
OC
Return to Master
T
OC
Return to Master
T
OC
Return to Master
T
OC
BEARING MAINTENANCE
This welder is equipped with a double-shielded ball bearing
having sufficient grease to last indefinitely under normal ser-
vice. Where the welder is used constantly or in excessively
dirty locations, it may be necessary to add one-half ounce of
grease per year. A pad of grease one inch wide, one inch
long and one inch high weighs approximately one-half
ounce. Over greasing is far worse than insufficient greasing.
When greasing the bearings, keep all dirt out of the area.
Wipe the fittings completely clean and use clean equipment.
More bearing failures are caused by dirt introduced during
greasing than from insufficient grease.
COMMUTATOR AND BRUSH MAINTENANCE
Uncovered rotating equipment can be dangerous.
Use care so your hands, hair, clothing or tools do
not catch in the rotating parts. Protect yourself
from particles that may be thrown out by the rotat-
ing armature when stoning the commutator.
------------------------------------------------------------------------
The generator brushes are properly adjusted when the
welder is shipped. They require no particular attention.
DO NOT SHIFT THE BRUSHES or adjust the rocker
setting.
Shifting of the brushes may result in:
- Change in machine output
- Commutator Damage
- Excessive brush wear
Periodically inspect the commutator, slip rings and
brushes by removing the covers. DO NOT remove or
replace these covers while the machine is running.
Commutators and slip rings require little attention.
However, if they are black or appear uneven, have
them cleaned by an experienced maintenance person
using fine sandpaper or a commutator stone. Never
use emery cloth or paper for this purpose.
NOTE:
If the welder is used in dirty or dusty locations,
or if the welder is not used for prolonged peri-
ods of time, it may be necessary to clean the
commutator and slip rings more often.
Replace brushes when they wear within 1/4" of the pig-
tail. A complete set of replacement brushes should be
kept on hand. Lincoln brushes have a curved face to fit
the commutator. Have an experienced maintenance
man seat these brushes by lightly stoning the commu-
tator as the armature rotates at full speed until contact
is made across the full face of the brushes. After ston-
ing, blow out the dust with low pressure air.
To seat the slip ring brushes, position the brushes in
place. Then slide one end of a piece of fine sandpaper
between slip rings and brushes with the coarse side
against the brushes. Pull the sandpaper around the cir-
cumference of the rings, in direction of rotation only -
until brushes seat properly. In addition, stone slip ring
with a fine stone. Brushes must be seated 100%.
Arcing or excessive exciter brush wear indicates a pos-
sible misaligned shaft. Have an authorized Field
Service Shop check and realign the shaft.
COOLING SYSTEM
The SAE-400 SEVERE DUTY is equipped with a pres-
sure radiator. Keep the radiator cap tight to prevent
loss of coolant. Clean and flush the cooling system
periodically to prevent clogging the passage and over-
heating the engine. When antifreeze is needed, always
use the permanent type.
FUEL FILTERS
When working on the fuel system
• Keep ungrounded lights away, do not
smoke !
• Do not spill fuel !
------------------------------------------------------------------------
The SAE-400 SEVERE DUTY is equipped with a
Fuel
Pre-Filter/Water Separator Assembly
located before
the lift pump and a
Secondary Fuel Filter
located after
the lift pump and before the fuel injectors. The Fuel
Pre-Filter/Water Separator is mounted to the engine
block just below the lift pump.
The Secondary Fuel Filter is mounted directly to the
engine just above the oil filter.
FUEL PRE-FILTER/WATER SEPARATOR ASSEMBLY
The pre-filter is a 150 micron screen designed to pro-
tect against gross fuel contamination of the water sep-
arator element and the Secondary Fuel Filter. If the
pre-filter becomes plugged it may be removed, inspect-
ed, cleaned and reinstalled. In general this only needs
to be done with each water separator element change
(about every 1,000 hrs.) However if at any time exces-
sive fuel contamination is suspected or a sudden fall-
off in engine performance is detected the pre-filter
screen should be inspected and cleaned. Follow the
following procedure:
WARNING
WARNING