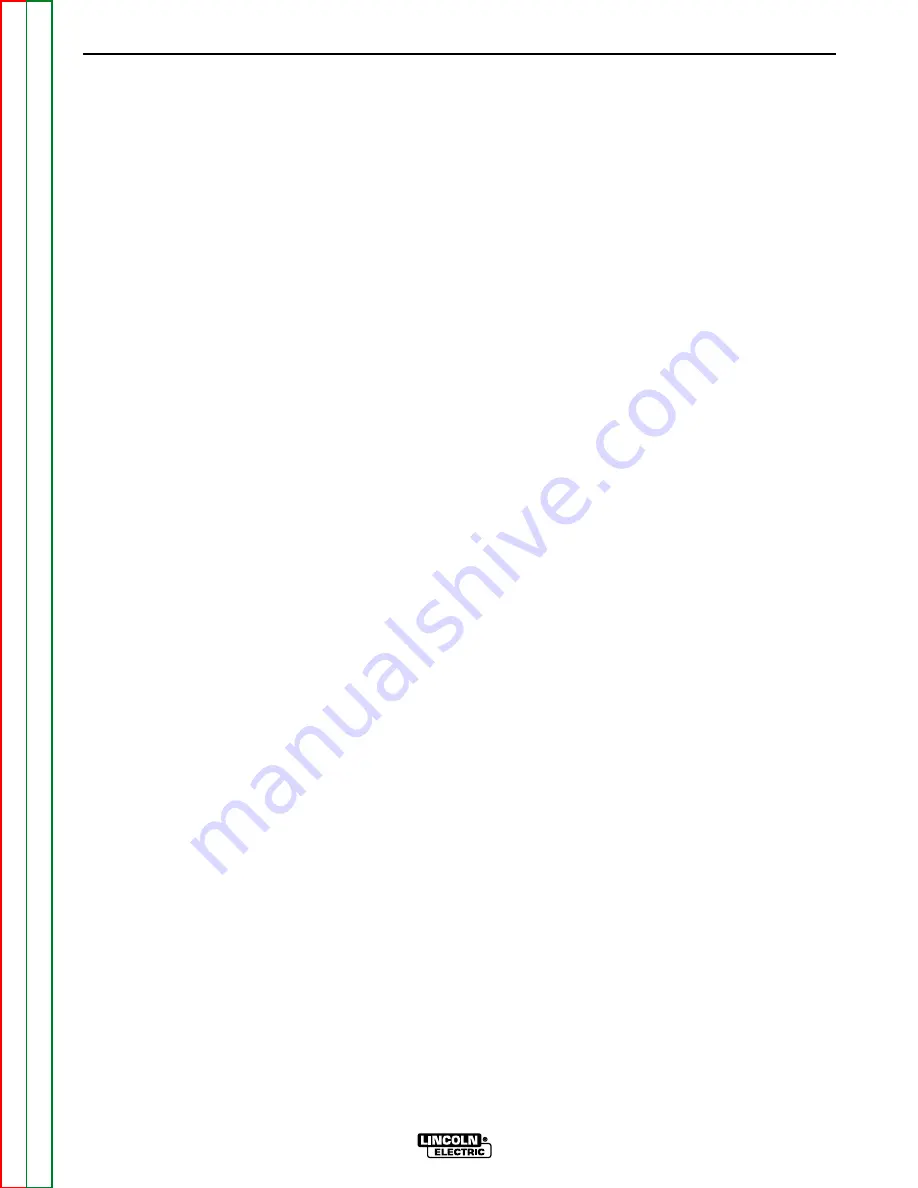
9. With the torch trigger activated check the
voltage at plug J32 pin-3 (lead#344) (posi-
tive) to plug J32 pin-14 (lead#312) (nega-
tive). Normal is less than 1 VDC. If more
than 1 VDC is indicated, the power output
board may be faulty. Release (deactivate)
the torch trigger and remove input power to
the Pro-Cut 55.
10. Perform the
Input Filter Capacitor
Discharge Procedure.
11. Check the continuity of leads #344 and
#312 between the output board and the
control board. See
Figure F.9,
the
Simplified Trigger Circuit Diagram,
and
Figure F.10
.
12. If all of the above checks are OK, the con-
trol board may be faulty. Replace.
TROUBLESHOOTING & REPAIR
F-40
F-40
PRO-CUT 55
Retur
n to Section TOC
Retur
n to Section TOC
Retur
n to Section TOC
Retur
n to Section TOC
Retur
n to Master TOC
Retur
n to Master TOC
Retur
n to Master TOC
Retur
n to Master TOC
TRIGGER CIRCUIT TEST
(continued)