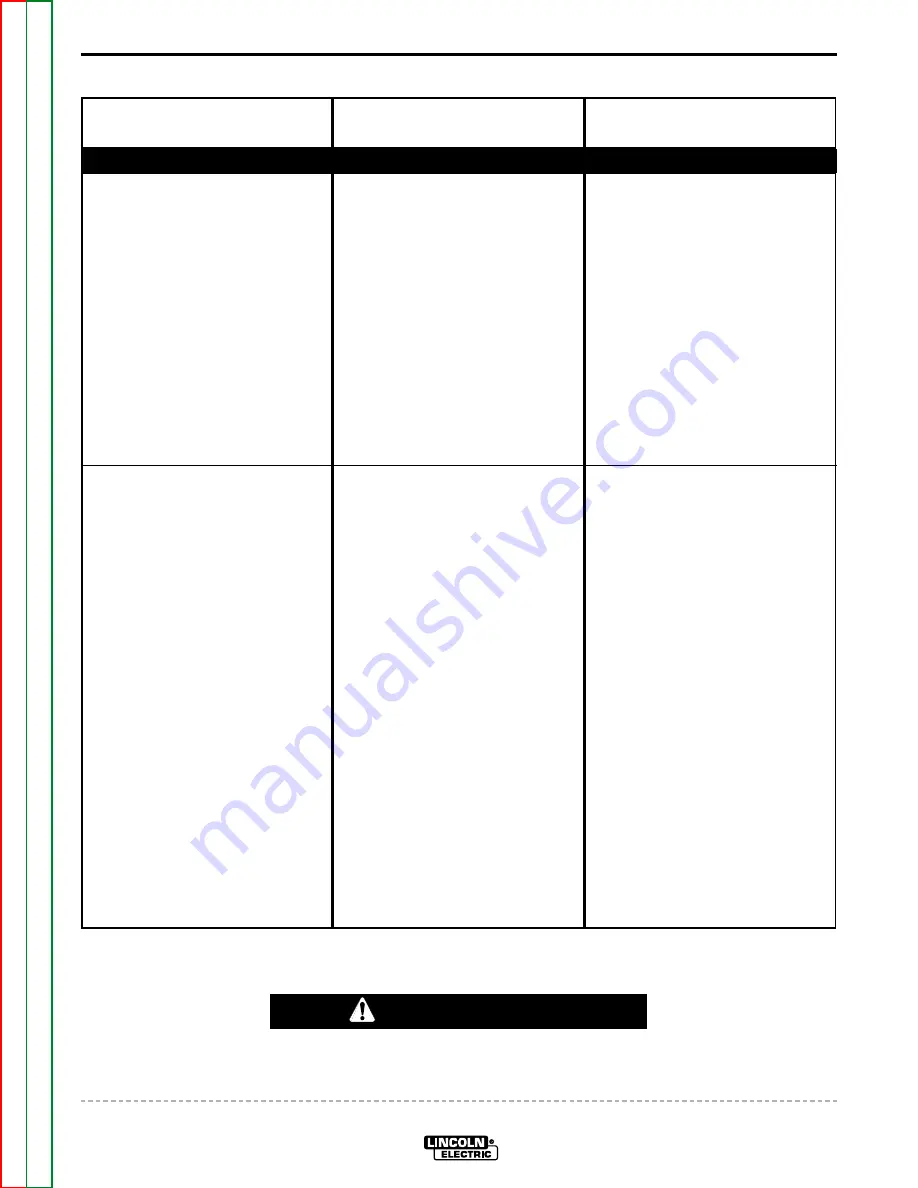
PRECISION TIG 185
TROUBLESHOOTING & REPAIR
F-10
F-10
Retur
n to Section TOC
Retur
n to Section TOC
Retur
n to Section TOC
Retur
n to Section TOC
Retur
n to Master TOC
Retur
n to Master TOC
Retur
n to Master TOC
Retur
n to Master TOC
TROUBLESHOOTING GUIDE
Observe Safety Guidelines
detailed in the beginning of this manual.
CAUTION
If for any reason you do not understand the test procedures or are unable to perform the test/repairs safely, con-
tact the Lincoln Electric Service Department for electrical troubleshooting assistance before you proceed. Call
1-888-935-3877.
TIG WELDING PROBLEMS
PROBLEMS
(SYMPTOMS)
POSSIBLE AREAS OF
MISADJUSTMENT(S)
RECOMMENDED
COURSE OF ACTION
Black areas along weld bead.
Weak high frequency - machine has
normal welding.
1. Clean any oily or organic conta-
mination from the work piece.
2. Tungsten electrode may be cont-
aminated. Replace or sharpen.
3. Check for contaminated gas or
leaks in the gas line, torch, or
associated connections.
4. The gas shielding may be insuffi-
cient. Increase gas flow: reduce
tungsten stickout beyond the gas
cup.
1. Check for loose or faulty connec-
tions at the torch and/or welding
cables.
2. The gas shielding may be insuffi-
cient. Increase gas flow: reduce
tungsten stickout beyond the gas
cup.
3. Check spark gap operation and
setting. Normal is (0.015").
Refer to
Maintenance
section of
this manual.
4. The work and electrode cables
may be in poor condition allowing
the high frequency to "leak off".
Use good quality cables with a
high natural rubber content, such
as Lincoln Stable Arc Cable.
Cables should be as short as
possible.
1. This may be a welding proce-
dure problem.
Contact The Lincoln Electric Service
Department, 1-888-935-3877.
1. Make sure that 115VAC is being
applied to the primary of the high
voltage transformer (T3). See
wiring diagram.
2. Check for any open or arcing
high frequency component.
Replace as required.
(Examples: C3, R3, C4)
3. If spark is weak at the spark gap,
check or replace the high fre-
quency circuit.
(Examples: T3, L3, L4).