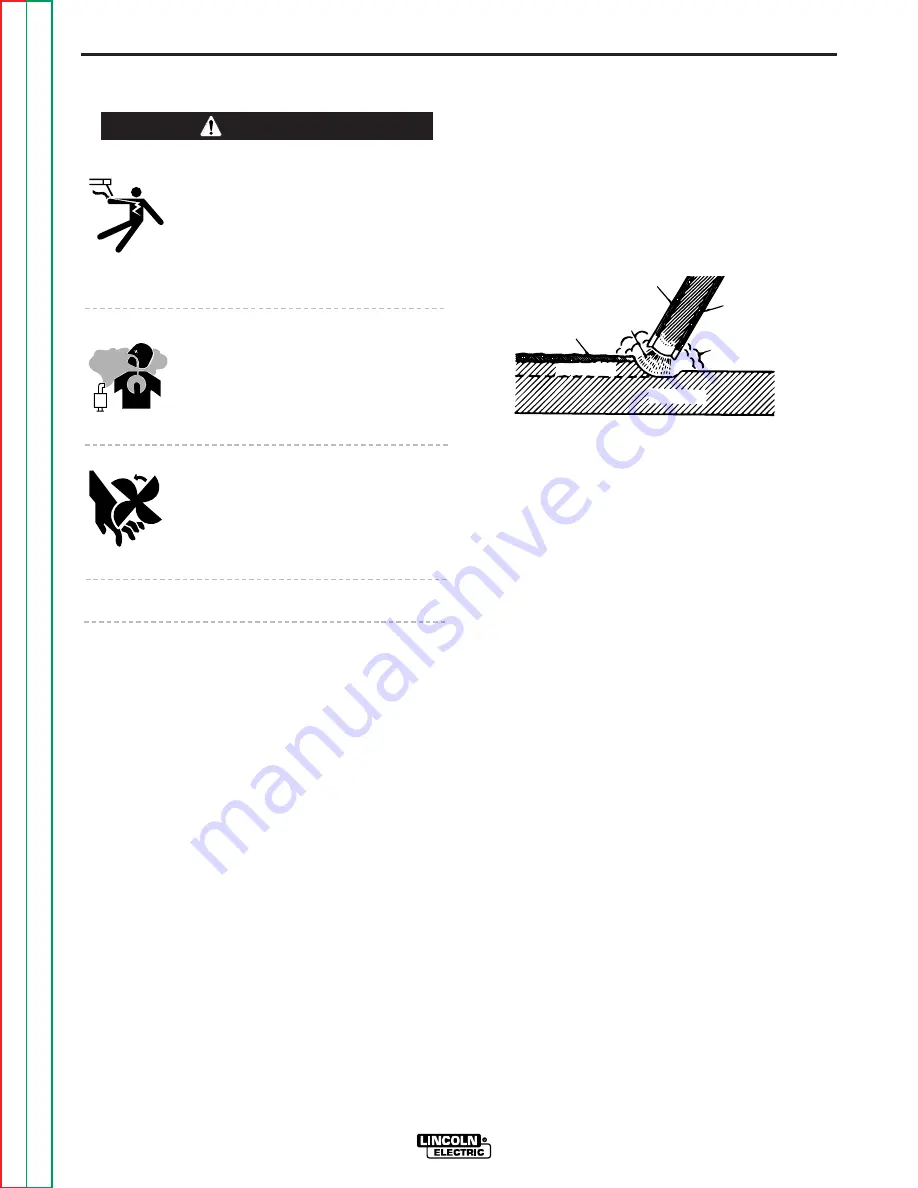
Return to Section TOC
Return to Section TOC
Return to Section TOC
Return to Section TOC
Return to Master TOC
Return to Master TOC
Return to Master TOC
Return to Master TOC
B-13
OPERATION
B-13
POWER-ARC 4000
The Power-Arc 4000 has a voltage output of up to 62
volts which can shock.
The electric arc is made between the work and the tip
end of a small metal wire, the electrode, which is
clamped in a holder that is held by the welder. A gap
is made in the welding circuit by holding the tip of the
electrode 1/16 - 1/8” (1.6-3.2mm) away from the work
or base metal being welded. The electric arc is
established in this gap and is held and moved along
the joint to be welded, melting the metal as it is
moved.
Arc welding is a manual skill requiring a steady hand,
good physical condition, and good eyesight. The
operator controls the welding arc and, therefore, the
quality of the weld made.
What Happens in the Arc?
Figure 4 illustrates the action that takes place in the
electric arc. It closely resembles what is actually
seen during welding.
The “arc stream” is seen in the middle of the picture.
This is the electric arc created by the electric current
flowing through the space between the end of the
electrode and the work. The temperature of this arc
is about 6000°F (3316°C) which is more than enough
to melt metal. The arc is very bright, as well as hot,
and cannot be looked at with the naked eye without
risking painful and possibly permanent injury. A very
dark lens, specifically designed for arc welding must
be used with the handshield or headshield whenever
viewing the arc.
The arc melts the base metal and actually digs into it,
much like water through a garden hose nozzle digs
into the earth. The molten metal forms a pool or
crater and tends to flow away from the arc. As it
moves away from the arc, it cools and solidifies. Slag
forms on top of the weld to protect it during cooling.
The function of the covered electrode is much more
than simply to carry current to the arc. The electrode
is composed of a core metal wire around which has
been extruded and baked a chemical covering. The
core wire melts into the arc and tiny droplets of
molten metal shoot across the arc into the molten
pool. The electrode provides additional filler metal for
the joint to fill the groove or gap between the two
pieces of the base metal. The covering also melts or
burns in the arc. It has several functions. It makes
the arc steadier, provides a shield of smoke-like gas
around the arc to keep oxygen and nitrogen in the air
away from the molten metal, and provides a flux for
the molten pool. The flux picks up impurities and
forms a protective slag. The principle differences
between the various types of electrodes are in their
coatings. By varying the coating, it is possible to
greatly alter the operating characteristics of elec-
trodes. By understanding the differences in the vari-
ous coatings, you will gain a better understanding of
selecting the best electrode for the job you have at
hand. In selecting an electrode, you should consider:
1. The type of deposit you want, e.g., mild steel,
stainless, low alloy, hardfacing.
2. The thickness of the plate you want to weld.
3. The position it must be welded in (downhand,
out-of-position).
4. The surface condition of the metal to be welded.
5. Your ability to handle and obtain the desired
electrode.
Four simple manipulations are of prime importance.
Without
complete mastery of these four, further
attempts at welding are futile.
With
complete
mastery of the four, welding will be easy.
ELECTRIC SHOCK can kill.
• Do not touch electrically live parts
or electrode with skin or wet cloth-
ing.
• Insulate yourself from work and
ground.
• Always wear dry insulating gloves.
WARNING
ENGINE EXHAUST can kill.
• Use in open, well ventilated areas
or vent exhaust outside.
• Do not stack anything on or near
the engine.
MOVING PARTS can injure.
• Do not operate with doors open or
guards off.
• Stop engine before servicing.
• Keep away from moving parts.
Only qualified personnel should install, use, or
service this equipment.
Covering
Electrode
Shielding Gases
Arc
Solidified Slag
Weld Metal
Base Metal
FIGURE 4. -The welding arc.