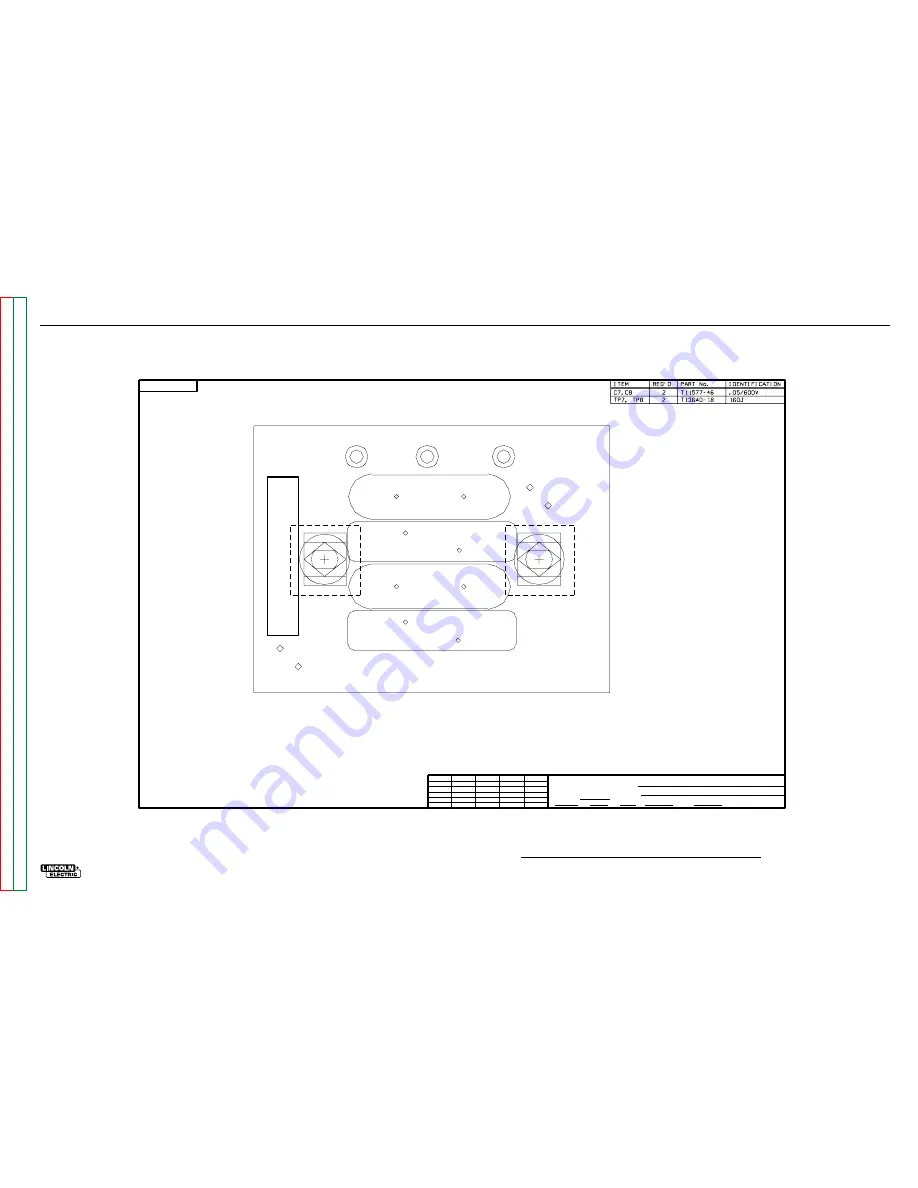
NOTE:
Lincoln Electric assumes no responsibility for liablilities resulting from board level troubleshooting. PC Board repairs will invalidate your factory warranty. Individual Printed Circuit Board Components are not available from Lincoln Electric. This information is pro-
vided for reference only. Lincoln Electric discourages board level troubleshooting and repair since it may compromise the quality of the design and may result in danger to the Machine Operator or Technician. Improper PC board repairs could result in damage to the
machine.
ELECTRICAL DIAGRAMS
G-7
PC BOARD ASSEMBLY - SNUBBER
Ch'ge. Sht. No.
2-19-93G
7-23-93C
TRANSFORMER WELDERS
OUTPUT SNUBBER P.C. BD. ASSEMBLY
C.S.
FULL
8-18-92
THE LINCOLN ELECTRIC CO.
CLEVELAND, OHIO U.S.A.
EQUIP.
TYPE
SCALE
SUBJECT
DR
DATE
CHK
REF.
SUP'S'D'G
SHT.
NO.
M
M
CAD
14312-1
14312-1
C7
TP7
C8
TP8
OUTPUT SNUBBER
GND
NEG
POS
M14312-1
G-7
Retur
n to Section TOC
Retur
n to Section TOC
Retur
n to Section TOC
Retur
n to Section TOC
Retur
n to Master TOC
Retur
n to Master TOC
Retur
n to Master TOC
Retur
n to Master TOC