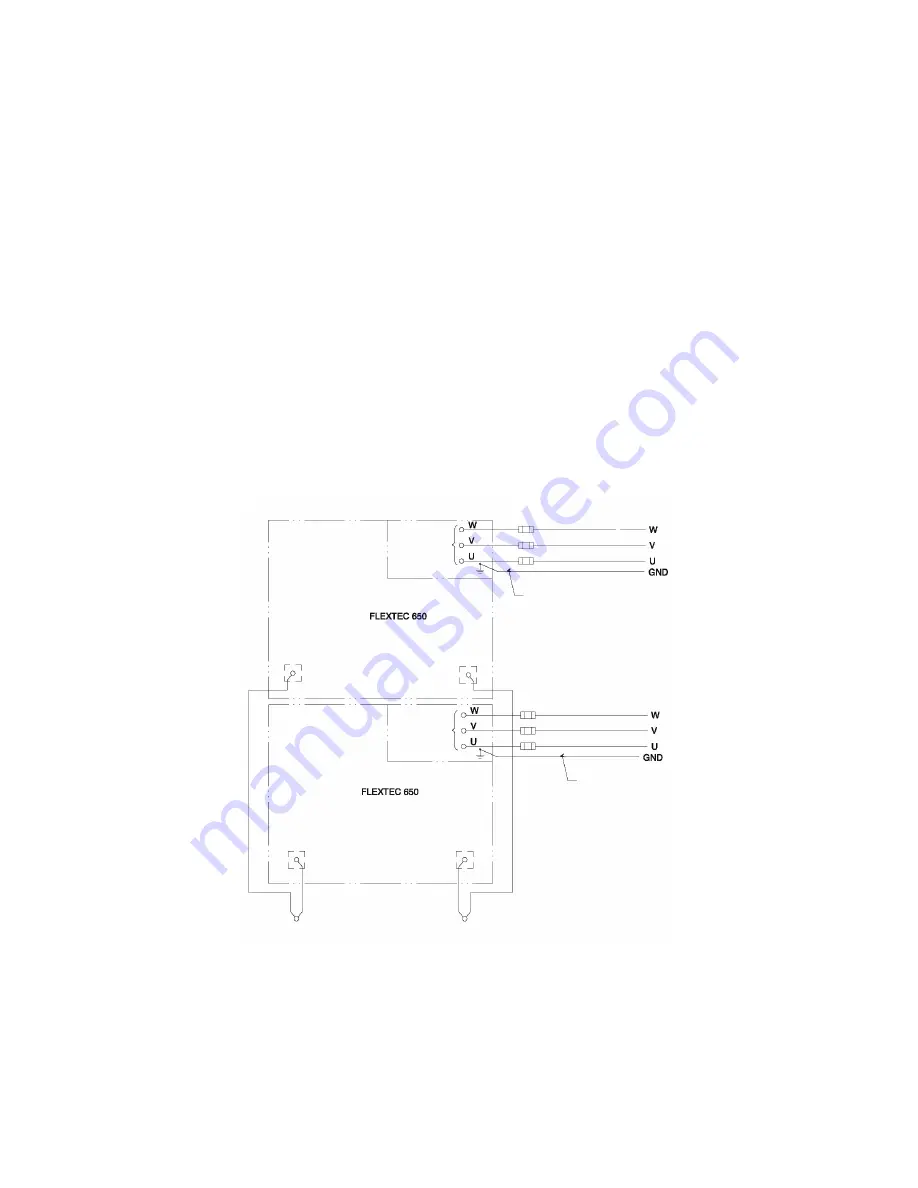
English
English
8
Control Cable Connections
General guidelines
Genuine Lincoln control cables should be used at all
times (except where noted otherwise). Generally, it is
recommended that the total length not exceed 100 feet
(30.5 m). The use of non-standard cables, especially in
lengths greater than 25 feet, can lead to communication
problems (system shutdowns), poor motor acceleration
(poor arc starting), and low wire driving force (wire
feeding problems). Always use the shortest length of
control cable possible, and DO NOT coil excess cable.
Regarding cable placement, best results will be obtained
when control cables are routed separate from the weld
cables. This minimizes the possibility of interference
between the high currents flowing through the weld
cables, and the low level signals in the control cables.
Paralleling (only for Flextec™ 650)
FLEXTEC™ 650 power sources may be paralleled for
increased output requirements. No kit is required for
paralleling of FLEXTEC™ 650 power sources. The
FLEXTEC™ 650 can only be paralleled for constant
current processes (mode switch must be in the SMAW
position). Connect the power sources as shown, and set
the output control of each power source to one half of
the desired arc current. (See Figure #3)
Figure #3: Paralleling Diagram
INPUT
TERMINAL
BLOCK
INPUT
TERMINAL
BLOCK
(MACHINE #1)
(MACHINE #2)
NEGATIVE
POSITIVE
NEGATIVE
AT WORK PIECE
POSITIVE
AT WORK PIECE
NEGATIVE POSITIVE
INPUT LINES
INPUT LINES
TO GROUND PER
NATIONAL ELECTRICAL
CODE
TO GROUND PER
NATIONAL ELECTRICAL
CODE