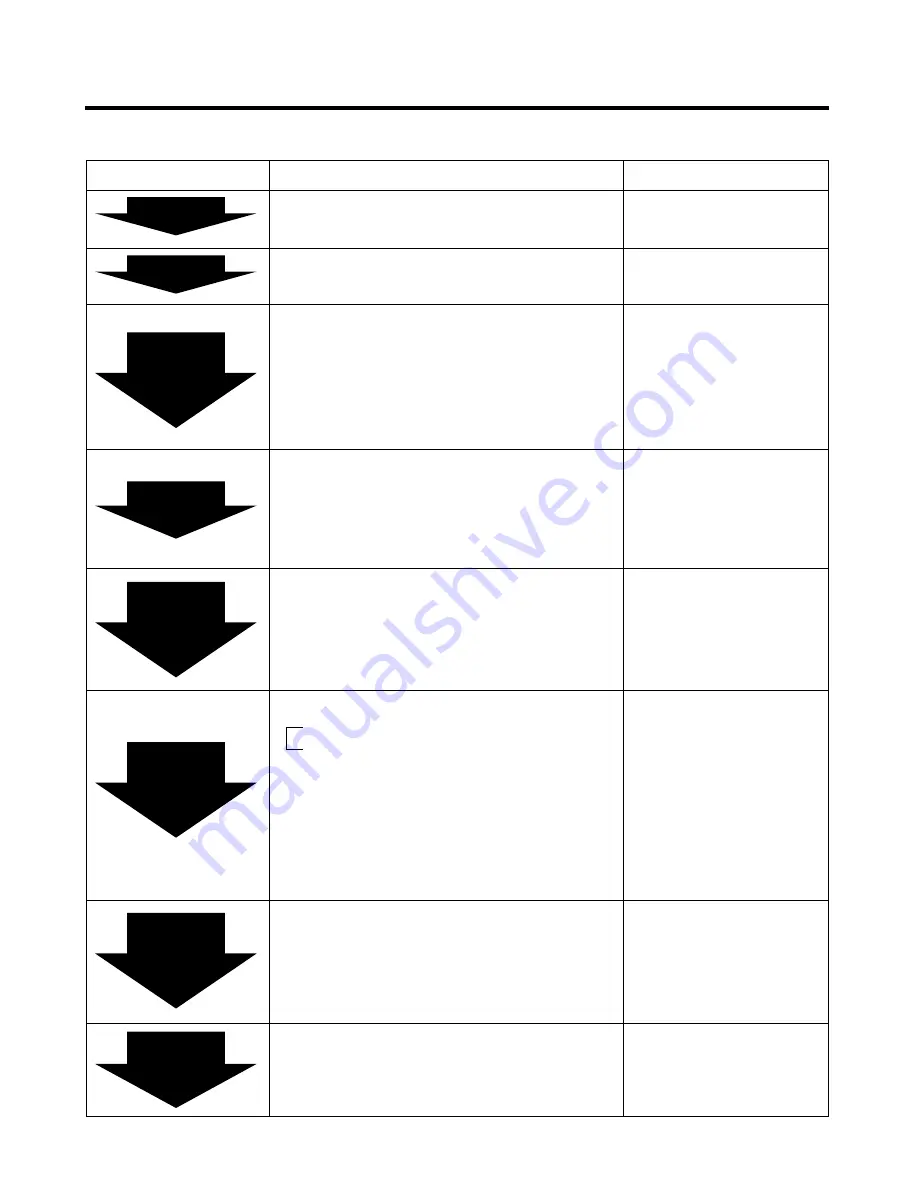
3-2. Summary Of Heavy Repair
TROUBLE DIAGNOSIS
- 101 -
Process
Contents
Tools
- Cut charging pipe ends and discharge refrigerant from
Filter, side cutters
drier and compressor.
- Use R134a oil and refrigerant for compressor and drier
Pipe Cutter, Gas welder, N
2
gas
- Confirm N
2
sealing and packing conditions before use.
Use good one for welding and assembly.
- Weld under nitrogen gas atmosphere.(N
2
gas pressure:
0.1-0.2kg/cm
2
).
- Repair in a clean and dry place.
- Evacuate for more than forty minutes after connecting
Vacuum pump(R134a
manifold gauge hose and vacuum pump to high (drier)
exclusively), Manifold gauge.
and low (compressor refrigerant discharging parts)
pressure sides.
- Evacuation Speed:113
l
/min.
- Weigh and control the allowance of R134a bombe in a
R134a exclusive bombe(mass
vacuum conditions to be ±5 g with electronic scales and cylinder), refrigerant(R134a)
charge through compressor inlet
manifold gauge, electronic
(Charge while refrigerator operates).
scales, punching off flier,
- Weld carefully after inlet pinching.
gas welding machine
- Check leak at weld joints.
Electronic Leak Detector,
Minute leak: Use electronic leak detector
Driver(Ruler).
Big leak: Check visually or fingers.
Note:Do not use soapy water for check.
- Check cooling capacity
➀
Check radiator manually to see if warm.
➁
Check hot line pipe manually to see if warm.
➂
Check frost formation on the whole surface of the
evaporator.
- Remove flux from the silver weld joints with soft brush
Copper brush, Rag, Tool box
or wet rag.(Flux may be the cause of corrosion and
leaks.)
- Clean R134a exclusive tools and store them in a clean
tool box or in their place.
- Installation should be conducted in accordance with the
standard installation procedure.(Leave space of more
than 5 cm from the wall for compressor compartment
cooling fan mounted model.)
Trouble
diagnosis
Remove refrigerant
Residuals
Parts
replacement
and welding
Compressor
compartment
and tools
arrangement
Transportation
and
installation
Check
refrigerant leak
and cooling
capacity
Vacuum
Refrigerant
charging and
charging
inlet welding
Содержание SxS GR-L207MSU
Страница 44: ...2 GR C247 B247 C207 B207 EXPLATION FOR MICOM CIRCUIT 44 a b c d ...
Страница 52: ...2 GR C247 B247 C207 B207 EXPLATION FOR MICOM CIRCUIT 52 ...
Страница 53: ...3 2 Parts list 1 GR P247 L247 P207 L207 EXPLATION FOR MICOM CIRCUIT 53 ...
Страница 54: ...EXPLATION FOR MICOM CIRCUIT 54 ...
Страница 55: ...2 GR C247 B247 C207 B207 EXPLATION FOR MICOM CIRCUIT 55 ...
Страница 56: ...EXPLATION FOR MICOM CIRCUIT 56 ...
Страница 58: ...2 GR C247 B247 C207 B207 EXPLATION FOR MICOM CIRCUIT 58 DOUBLE SIDE TAPE SPREAD SHEET ...
Страница 60: ...2 GR C247 B247 C207 B207 60 Reception Transmission Parts without mark means SMD parts ...
Страница 62: ...EXPLATION FOR MICOM CIRCUIT 62 PCB ASSEMBLY DISPLAY PCB ASSEMBLY MAGIC DISPLAY ...
Страница 63: ...2 GR C247 B247 C207 B207 EXPLATION FOR MICOM CIRCUIT 63 ...
Страница 64: ...EXPLATION FOR MICOM CIRCUIT 64 PCB ASSEMBLY DISPLAY PCB ASSEMBLY MAGIC DISPLAY ...
Страница 71: ...CIRCUIT 71 ...
Страница 72: ...CIRCUIT 72 ...
Страница 126: ...P No 3828JD8694A JUL 2004 Printed in Korea ...