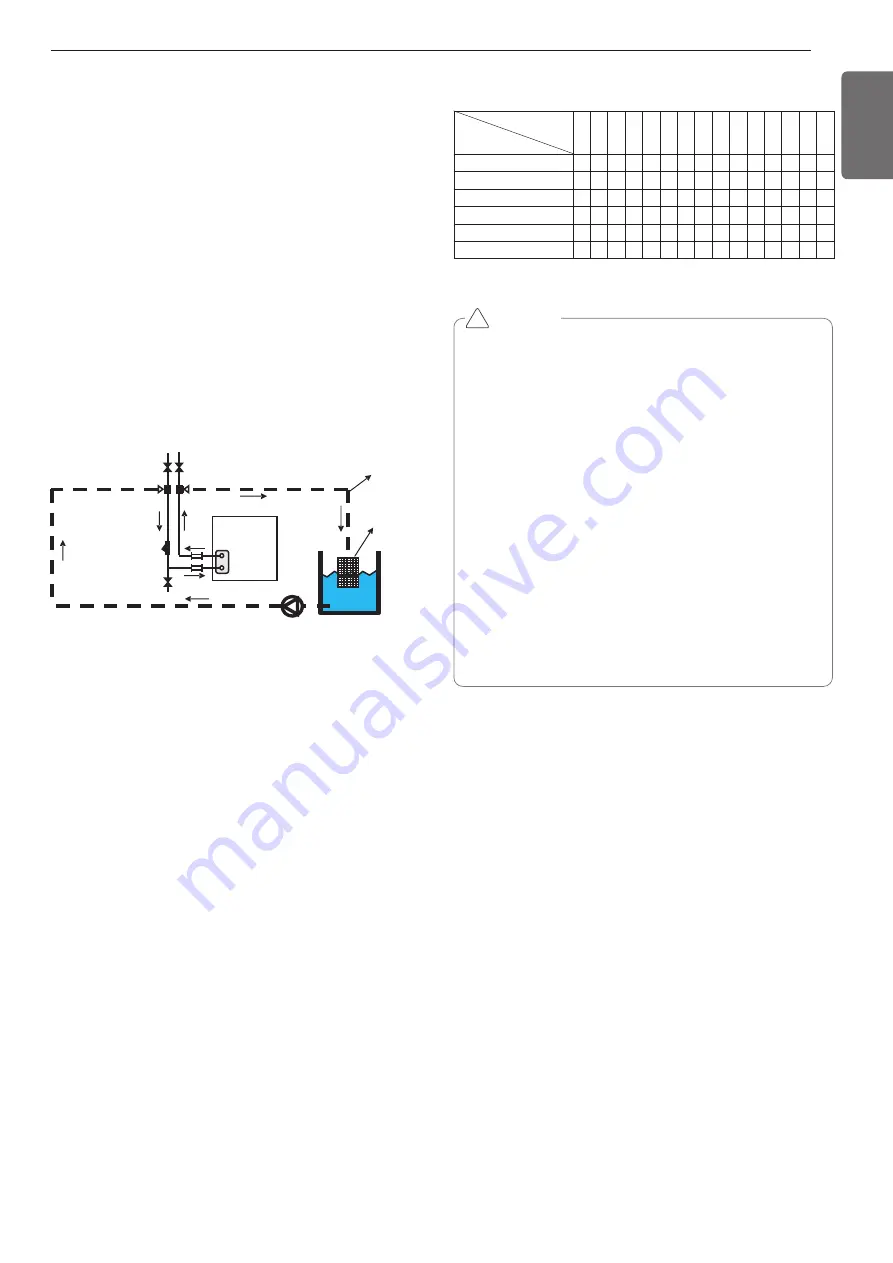
3
9
ENGLISH
Daily check/management
1
Water quality control
The plate type heat exchanger is not structured to be disassem-
bled, cleaned or replaced with parts. To prevent corrosion or scaling
on the plate type heat exchanger, special care must be taken to
control the water quality. Water quality must satisfy the minimum
criteria of the reference water quality items. When anti-corrosion
agent or corrosion inhibitor is added, the substance must not have
any corrosive effect on stainless steel and copper. Even if the circu-
lating water is not contaminated by the external air, it is recom-
mended to empty the water flowing in the pipe and to resupply the
water.
2
Flow rate control
If the flow rate is insufficient, it can cause freezing on the plate type
heat exchanger. Check whether the strainer is clogged or whether
the pipe is filled with air and then check the temperature and pres-
sure difference of the inlet and outlet pipe to check whether the
flow rate is insufficient. If the temperature and pressure difference
is above the appropriate level, it means that the flow rate is re-
duced. In this case, the operation must immediately be stopped
and re-operated when the root cause is resolved. (*If air is trapped
in the pipe, the air must be purged. Air inside the water pipe inter-
feres with the circulation of the heat water supply and can cause in-
sufficient flow rate or freezing.)
3
Brine density management
When using the brine (Anti-freeze) in the heat water supply, desig-
nated type and density must be used. Calcium chloride brine can
cause corrosion on the plate type heat exchanger and must not be
used. If the anti-freeze liquid is left as is, it absorbs the moisture
from the air to cause a drop in the density, leading to freezing of
plate type heat exchanger. Therefore minimize the contact surface
with the atmosphere and periodically measure the density of the
brine to supplement the brine as needed to maintain the density.
Maintenance/Repair checklist
1 2 3 4 5 6 7 8 9 10 11 12 13 14 15
● ● ● ● ● ● ● ● ● ● ● ● ● ● ●
●
●
●
● ● ● ● ● ● ● ● ● ● ● ● ● ● ●
● ● ● ● ● ● ● ● ● ● ● ● ● ● ●
●
●
● ● ● ● ● ● ● ● ● ● ● ● ● ● ●
Period (Year)
Checkpoint
Product operating condition
Heat exchanger cleaning (Wash)
Strainer cleaning
Water quality check
Refrigerant leakage check
Indoor unit filter cleaning
CAUTION
• The above checklist is set based on the minimum period and
more frequent checking can be required depending on the oper-
ating condition/water quality condition.
• When cleaning the heat exchanger, make sure to take parts out
or lock the value so that chemical detergent does not penetrate
into the pressure gauge etc.
• When cleaning the heat exchanger, check the connecting part of
the water pipes prior to cleaning so that the chemical detergent
does not leak.
• After sufficiently mixing the chemical detergent with water, start
cleaning.
• Cleaning the heat exchanger is easier at the initial stage and be-
comes difficult after the scaling has accumulated.
• In areas where the water quality is poor, cleaning is required pe-
riodically.
Because chemical detergent has strong acidity, it must be
washed off thoroughly with water.
• To check whether it is cleaned well inside, remove the hose and
check the inside.
• Purge the air to remove any air inside the water pipe.
• After checking, always check whether the heat water supply is
flowing normally flowing before operating the product.
!
2) Be sure to check if the gate valve of inflow/outflow pipe and the
valve for outflow pipe are properly closed when cleaning.
3) Connect the water pipe for cleaning with the chemical solvent
through the service plug of the pipe and fill up the panel heat ex-
changer with 50°C~60°C(122°F~140°F) of cleaning solvent and
circulate it with the pump for 2~5 hours. The circulation time
may depend on the temperature of the cleaning solvent or the
creation of the scales. Therefore, observe change in the color of
the chemical solvent to set the circulation time for removing the
scales.
4) After the circulation of the solvent, extract the solvent inside of
the panel heat exchanger and fill up 1~2% of NaOH or NaHCO3
and then, circulate it for 15~20 minutes to neutralize the heat ex-
changer.
5) Once the neutralization is completed, clean the inside of the
panel heat exchanger with clean water.
Measure the water Ph to check if the chemical solvent is prop-
erly removed or not.
6) When using a different kind of chemical solvent in the market, be
sure to check if there is any corrosive action to stainless or cop-
per in advance or not.
7) For details on the cleaning chemical solvent, be sure to consult
the specialists of the related corporation.
3
After cleaning, operate the device to see if it works properly once
again.
Gate valve(locked)
Service plug
Strainer
Outflow water
valve(locked)
Gate valve(locked)
Water-cooling
type Multi V
Hose
Pump
[Cleaning the panel heat exchanger]
Screening net
Содержание multi V ARWB Series
Страница 44: ...44 ENGLISH ...