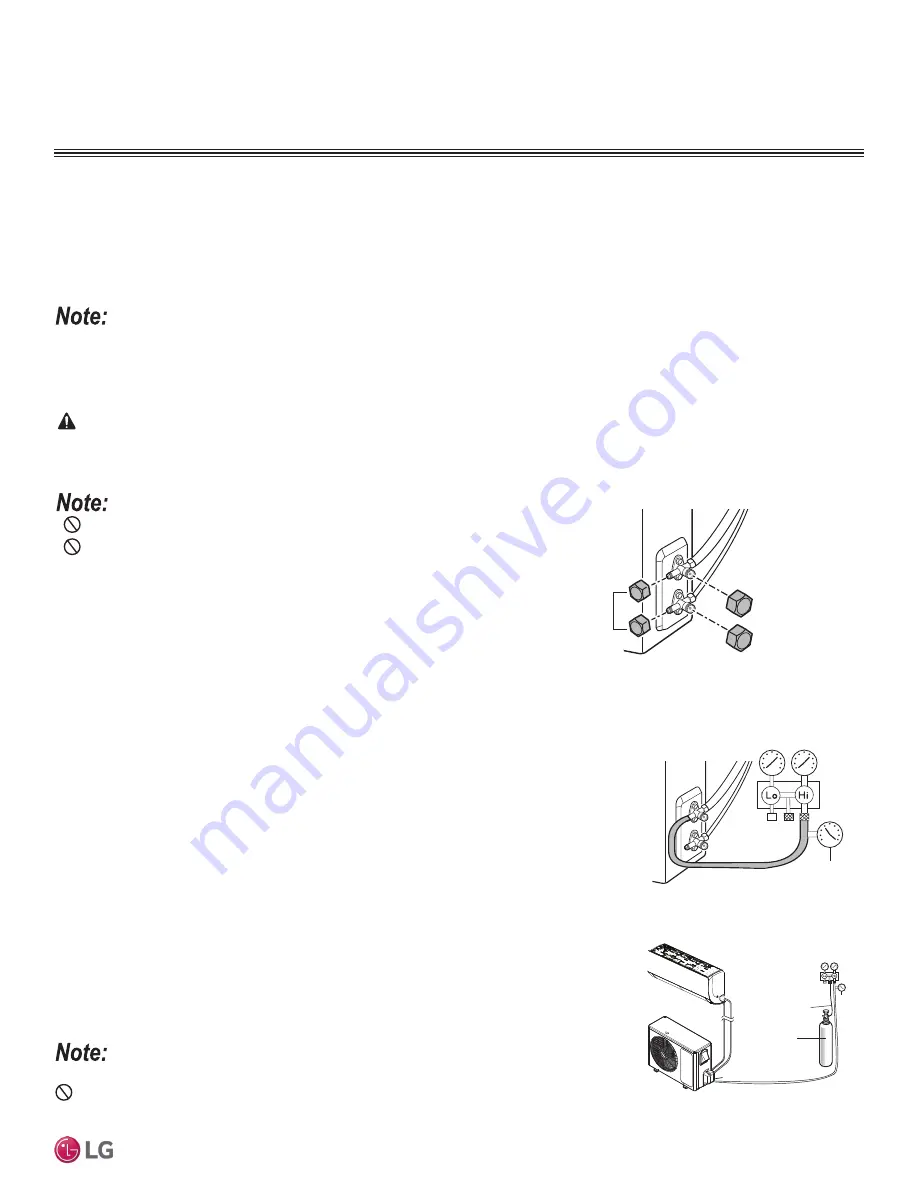
59
Final Installation Procedures
Due to our policy of continuous product innovation, some specifications may change without notification.
©LG Electronics U.S.A., Inc., Englewood Cliffs, NJ. All rights reserved. “LG” is a registered trademark of LG Corp.
FINAL INSTALLATION PROCEDURES
Triple Leak / Pressure Test
After the refrigerant piping installation is complete, perform a triple leak / pressure test. Triple leak / pressure test is performed between the
outdoor unit and indoor unit to verify that refrigerant can flow through the system without danger of leaks or pressure losses. Air and moisture
that is left in the piping can lead to undesirable results and can cause damage to the system. It is important to go through a complete leak /
pressure cycle to be sure that the refrigerant piping is cleared out. This process may have to be repeated if any air or moisture be is found to
remain in the piping.
• Pressure in the system can rise.
• Operating current can rise.
• Inefficient cooling or heating mode capability.
• Moisture in the refrigerant circuit will freeze and block capillary
tubing.
• Water can lead to corrosion of parts in the system.
Figure 105: Outdoor Unit Service Valves.
,QVXI¿FLHQWRULQFRUUHFWO\GRQHDLUSXUJLQJZLOOOHDGWRWKHIROORZLQJ
DANGER
8VLQJFRPEXVWLEOHJDVHVLQFOXGLQJR[\JHQZLOOUHVXOWLQ¿UHRUH[SORVLRQUHVXOWLQJLQSHUVRQDOLQMXU\RUGHDWK8VHLQHUWJDVPHGLFDOJUDGHGU\
nitrogen) when checking leaks, cleaning, installing/repairing pipes, etc. The use of an 800 psig or higher nitrogen regulator is required for safety.
•
Never perform the leak test using refrigerant.
•
To avoid nitrogen entering the refrigerant system in a liquid state, the top
of the cylinder must be higher than its bottom (used in a vertical standing
position) when the system is pressurized.
• Use only a leak-free gauge manifold set.
• Piping system must not be pressured to more than 550 psi. Pressures greater
than 550 psi will damage the piping system and cause unit malfunction.
Triple Leak / Pressure Check Procedure
1. After the refrigerant piping installation is complete, open the isolation ball valves, if any, that may
have been included in the piping system.
2. Verify that both the liquid and gas (vapor) suction line outdoor unit service ports are closed, and
the stem head access caps are tight. The leak / pressure check is to be performed only to the
refrigerant piping system and the connected indoor unit.
3. Remove the cap on the gas (vapor) suction line Schrader port. Connect the (medical-grade dry)
nitrogen cylinder regulator to a gauge manifold, then connect the gauge manifold to the gas
(vapor) suction Schrader port on the service port.
4. Perform the leak / pressure check at 150 psig for fifteen (15) minutes (standing pressure check).
5. Perform the leak / pressure check at 300 psig for thirty (30) minutes (standing pressure check).
6. Perform the leak / pressure check at 550 psig for one (1) hour to make sure the piping system is
leak-free. After the gauge reading reaches 550 psig, isolate the system by first closing the gauge
manifold, then close the nitrogen cylinder valve. Check the flared (and any brazed connections)
for leaks by applying a bubble solution to all joints.
The bubble solution must be a solution designed for refrigerant leak testing. Common soap solution must
never be used on refrigerant piping as those contain chemicals that could corrode copper and brass,
and cause product malfunction.
Triple Leak / Pressure Test
Figure 106: Gauge Manifold Hose Con-
nected to the Schrader Valve on the Gas
(Vapor) Service Port.
Gas (Vapor)
Service Valve
Cap
Liquid Service
Valve Cap
Schrader
Valve
Caps
Figure 107: Triple Leak / Pressure Test
Diagram (Outdoor Unit Appearance Will
Differ Depending on Model).
Indoor Unit
Outdoor Unit
Gauge Manifold
Charge Hose
Nitrogen Gas
Tank (Upright
Position)
Refrigerant
Piping
Micron
Gauge
Connected to Shrader Valve
on Gas (Vapor) Service Port
Gauge Manifold
Micron
Gauge