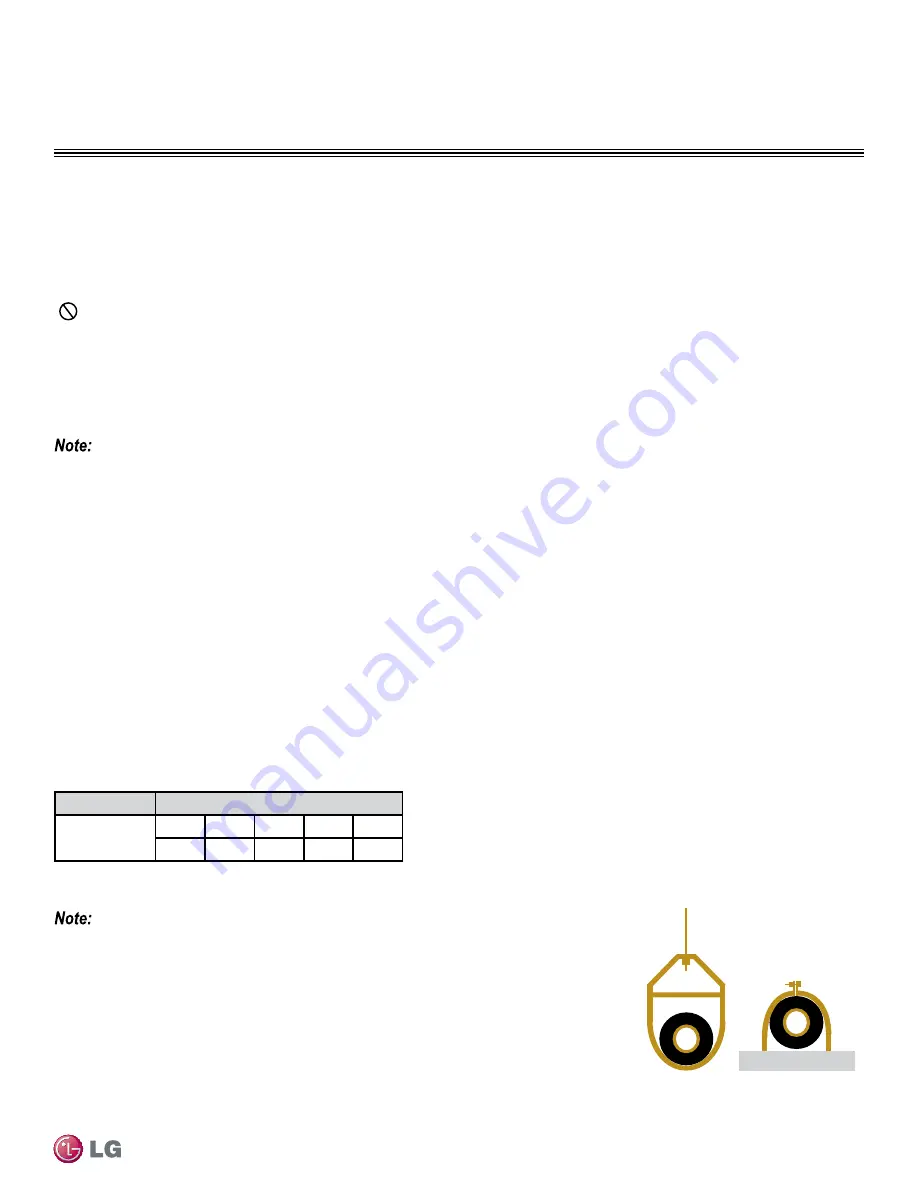
23
General Installation Guidelines
Due to our policy of continuous product innovation, some specifications may change without notification.
©LG Electronics U.S.A., Inc., Englewood Cliffs, NJ. All rights reserved. “LG” is a registered trademark of LG Corp.
GENERAL INSTALLATION GUIDELINES
Piping Materials and Handling / Piping Support
Pipe Bends
When bending soft copper, use long radius bends. Refer to the "Radii of Coiled Expansion Loops and Developed Lengths of Expansion
Offsets” table for minimum radius specifications, as shown on previous page.
In-line Refrigeration Components
Components such as oil traps, solenoid valves, filter-dryers, sight glasses, tee fittings, and other after-market accessories are not permitted on the
refrigerant piping system between the outdoor unit and the indoor unit.
Duct Free Single Zone systems are provided with redundant systems that assure oil is properly returned to the compressor. Sight-glasses
and solenoid valves may cause vapor to form in the liquid stream.
Over time, dryers may deteriorate and introduce debris into the system. The designer and installer should verify the refrigerant piping system is free of
traps, sagging pipes, sight glasses, filter dryers, etc.
Field-provided Isolation Ball Valves
LG allows the installation of field-supplied ball valves with Schrader ports at each indoor unit. Full-port isolation ball valves with Schrader
ports (positioned between valve and indoor unit) rated for use with R410A refrigerant should be used on both the liquid and vapor lines.
If valves are not installed and a single indoor unit needs to be removed or repaired, the entire system must be shut down and evacuated.
Position valves with a minimum distance of three (3) to six (6) inches of pipe on either side of the valve, and placed between six (6) and
twelve (12) inches from the run-out pipe to the upstream main pipe. If ball valves are installed closer to the indoor unit, a section of pipe
becomes a dead zone when the valves are closed where oil may accumulate.
Using Elbows
Field-supplied elbows are allowed as long as they are designed for use with R410A refrigerant. The designer, however, should be cautious
with the quantity and size of fittings used, and must account for the additional pressure losses in equivalent pipe length calculation.
The equivalent pipe length of each elbow must be added to each pipe segment (Table 11).
Component
Size (Inches)
Elbow (ft.)
1/4
3/8
1/2
5/8
3/4
0.5
0.6
0.7
0.8
1.2
Table 11: Equivalent Piping Length for Piping Components
Pipe Supports
A properly installed pipe system should be adequately supported to avoid pipe sagging. Sagging pipes
become oil traps that lead to equipment malfunction.
Pipe supports should never touch the pipe wall; supports shall be installed outside (around) the
primary pipe insulation jacket (see Figure 25). Insulate the pipe first because pipe supports shall
be installed outside (around) the primary pipe insulation jacket. Clevis hangers should be used with
shields between the hangers and insulation. Field provided pipe supports should be designed to
meet local codes. If allowed by code, use fiber straps or split-ring hangers suspended from the ceil
-
ing on all-thread rods (fiber straps or split ring hangers can be used as long as they do not compress
the pipe insulation). Place a second layer of insulation over the pipe insulation jacket to prevent
chafing and compression of the primary insulation within the confines of the support pipe clamp.
Figure 25: Pipe Hanger Details