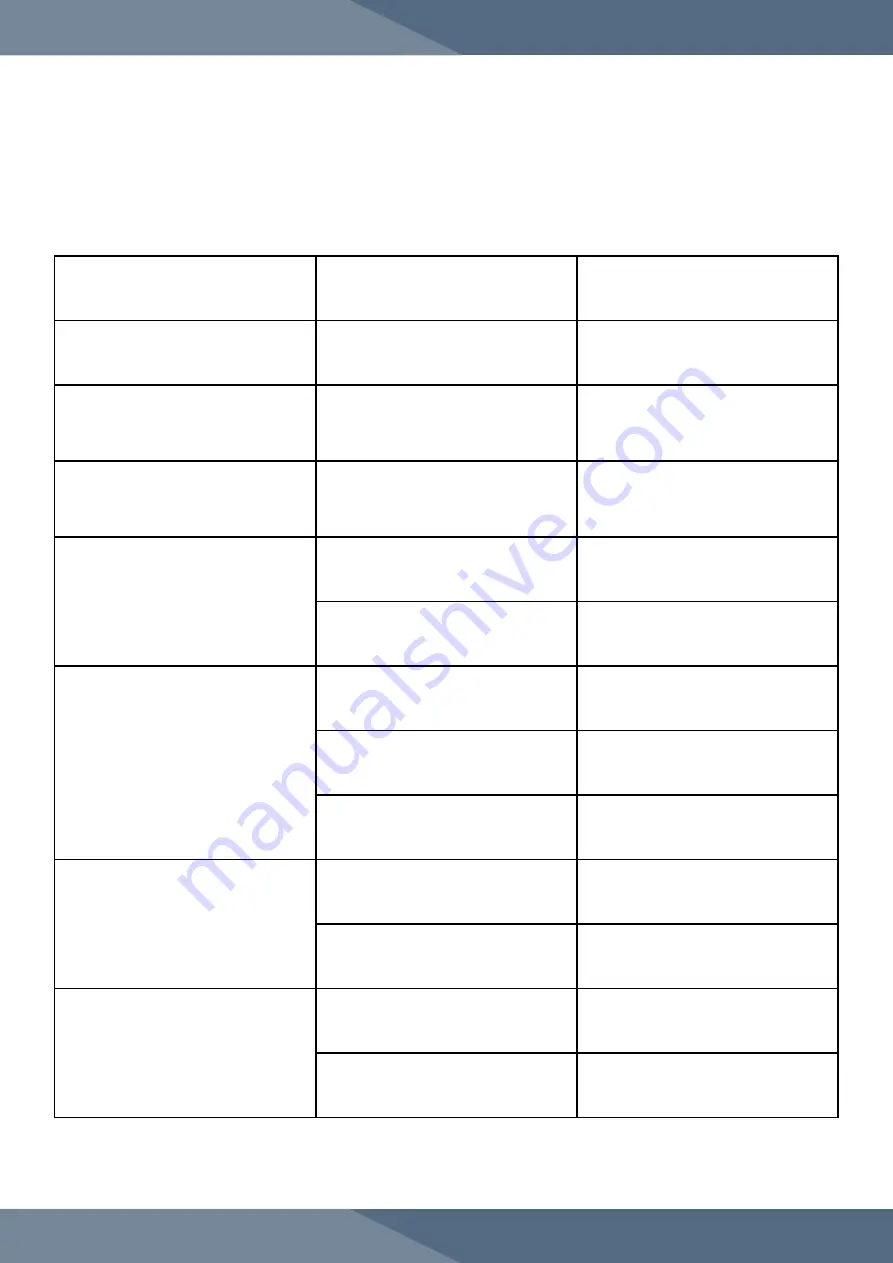
66
Troubleshooting
Sometimes unavoidable issues will occur while operating the SACF 25
®
. Fortunately, there are
several methods to remedy these issues.
Common Issues
Symptom
Possible Cause
Possible Solution
Capsule caps fly from machine
The vacuum pressure is too high.
Adjust the vacuum pressure to
approximately 0.03-0.04 MPa.
Two capsules are inserted into the
Capsule Discs at the same time
The Capsule Sewing Mechanism's
gate opens too early.
Adjust the mounting block so that
the Sewing Section's gate allows the
capsules to be center in the Capsule
Discs' holes.
Capsules are not inserted into the
Capsule Discs
The Capsule Discs' holes and the
Capsule Sewing Mechanism teeth are
not aligned/out of sync.
Use the Alignment Tools that come
in the SACF 25
®
Toolkit to realign the
Capsule Discs and Capsule Sewing
Mechanism teeth.
Capsule caps and bodies do not
separate
The vacuum pump's pressure needs
to be adjusted.
Increase the vacuum pump pressure.
The capsule sizes are inappropriate
for the Tooling and/or capsules are
defective.
Ensure that the capsules are
standard-compliant and an
appropriate size for the Tooling.
The capsules' fill measurements are
inconsistent/uneven
The Capsule Disc is not in the correct
position.
Reinsert the Capsule Disc and ensure
that it is securely on its insert.
There is not enough powder in the
Powder Hopper.
Pour more powder into the Powder
Hopper.
The Tooling is damaged.
Remove and replace the Tooling
(Capsule Discs, Capsule Magazine,
and Capsule Ejection Disc)
The fill dosage is too high or too
low
The speed of the Capsule Disc
rotation and Auger inside of Powder
Hopper is inconsistent.
Adjust the Capsule Disc's rotation
speed and the Auger to until they are
consistent.
The air pressure is not high enough to
make the Capsule Disc rotate.
Check and adjust the air pressure to
be around 0.4-0.7 MPa.
Capsules are locking too tight or
too loose
The air pressure is too high or not
high enough.
Adjust the air pressure to be around
0.4-0.7 MPa.
The water content of the powder is
too high.
Reduce the working environment's
humidity to below 45% and/or dry the
powder.