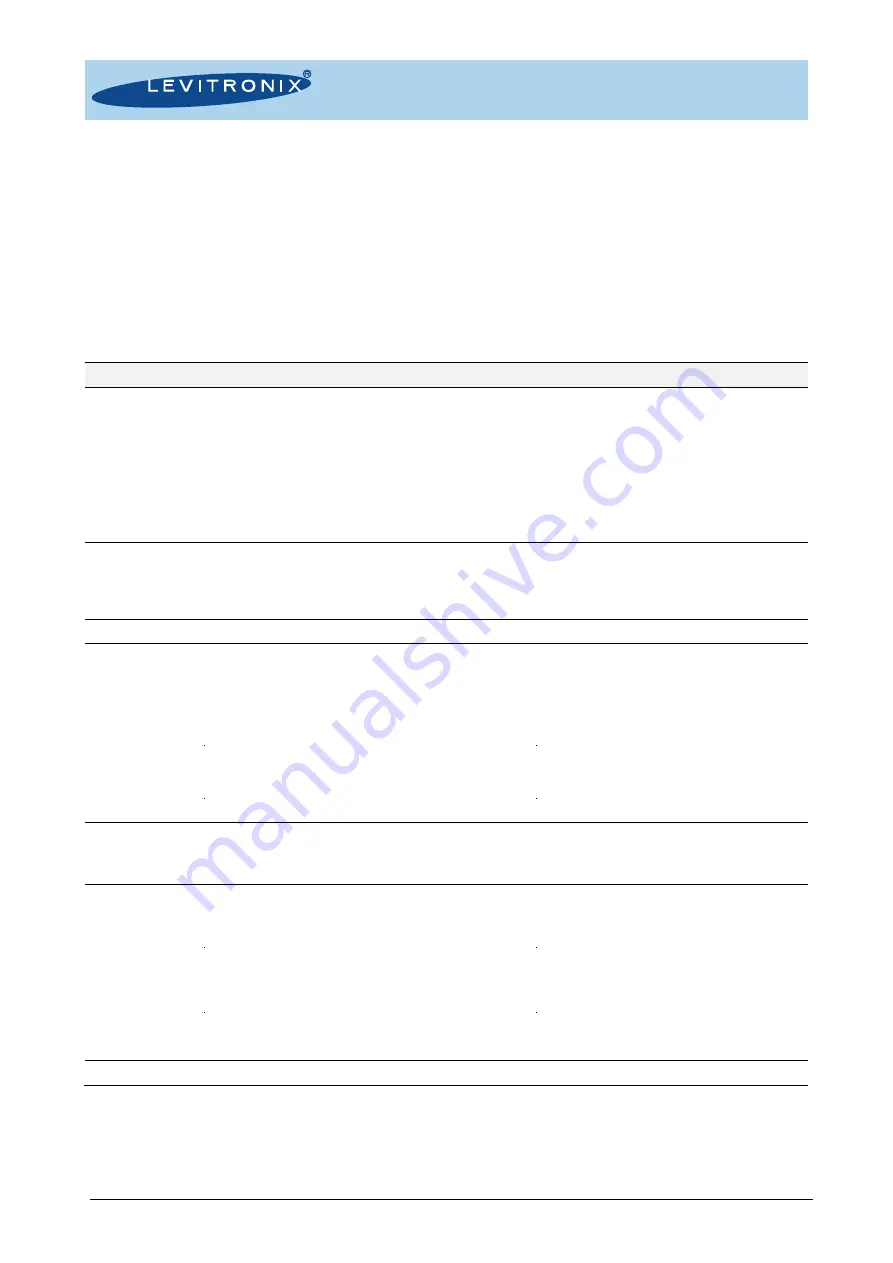
User Manual for BFS-i10
www.levitronix.com
PL-3505-00, Rev00, DCO# 21-249
14
•
RS485 interface:
To use RS485 as a control or service interface, an initialization resistor network
according to
should be used to ensure stable communication and avoid disturbance effects.
For service and debugging purposes with the
Levitronix
®
Service Software
an RS485 to USB converter
cable (initialization network included) can be ordered according to
. Do not use multiple master
devices at the same time.
•
RS485 Fieldbus Multi-System Arrays:
Several systems can be directly connected to the same
RS485 master. Following points and information shall be considered:
a.
Address setting of the fan units can be done with the
Levitronix
®
Service Software
and a
PC.
b.
A termination resistor is recommended for long bus lengths. Do not use closed ring
arrangements. Contact
Levitronix
®
Technical Service
department (see
Section 6.3
) for further
details and support.
Pin
Wire Color
Description
Levels
Notes
B4
Pink
Digital input 1
Enable / reset
5…24 V (min. 30 ms, edge triggered)
SPEED or PROCESS
or RESET
0 V (min. 30 ms, edge triggered)
STANDBY
Positive edge:
- Turns the system ON from state STANDBY
(PROCESS if digital input 2 is on, else SPEED)
- Resets the system from state ERROR
Recommended delay between reset and enable-on
positive edges: 500 ms
Negative edge:
- Turns the system OFF, if it was started by digital in 1
- Else no effect
Input logic may be inverted via
Service Software
or
Modbus protocol.
B5
Gray
Digital input 2
Process mode
5…24 V (min. 30 ms)
PROCESS Control
0 V (min. 30 ms)
SPEED Control
Switch between process control (closed loop pressure
or flow control) and speed control if system was
started by digital in 1 (no effect else)
Input logic may be inverted via
Service Software
or
Modbus protocol.
B3
Yellow
Digital input ground
Reference for digital inputs
B6
Violet
Analog input 1
Setpoint speed or
setpoint process value
Speed mode:
4…20 mA * =
0…7400 rpm *
Process mode:
4…20 mA * =
0…100 % *
Analog input 1 is enabled if the system was started by
a positive edge on digital input 1 and disabled as soon
as the power output is deactivated. Message 80h “PLC
analog input active” indicates that the input is active.
Setpoint speed or process requests over Modbus or
Service Software
will be overridden when analog input
1 is active.
B1
Gray-pink
Analog input 2
Actual process value
(pressure or flow sensor)
4...20 mA * =
0…100% *
Connect to an external pressure or flow sensor to use
process control mode
B2
Blue
Analog input ground
Reference for analog inputs
A2
Brown
Digital output 1
System state signal
Circuit closed
Power output ACTIVE
Circuit open
Power output NOT active
I
ndicates if the system’s power output is ON or OFF
Ground (A4) is reference
A3
White
Digital output 2
Error signal
Circuit closed
NO error present
Circuit open
ERROR(s) present
Indicates if errors are present
Ground (A4) is reference
A1
Blue-red
Analog output
Actual speed or
actual process value
Speed:
4...20 mA * =
0…7400 rpm *
Process value:
4…20 mA * =
0
…100 % *
Assignment (speed / process / mode dependent) can
be changed via
Service Software
or Modbus protocol
Ground (A4) is reference
A5
Brown-green
RS485 +
Modbus protocol
Termination resistors recommended
A6
White-yellow
RS485 -
A4
White-green
Ground
GND / earth
Internally connected to power - and cable shield
Table 6: Configuration of PLC connector for standard firmware
For other PLC configurations refer to alternate firmware documentation.
* Levels configurable in EEPROM editor of Levitronix
®
Service Software or through Modbus protocol.