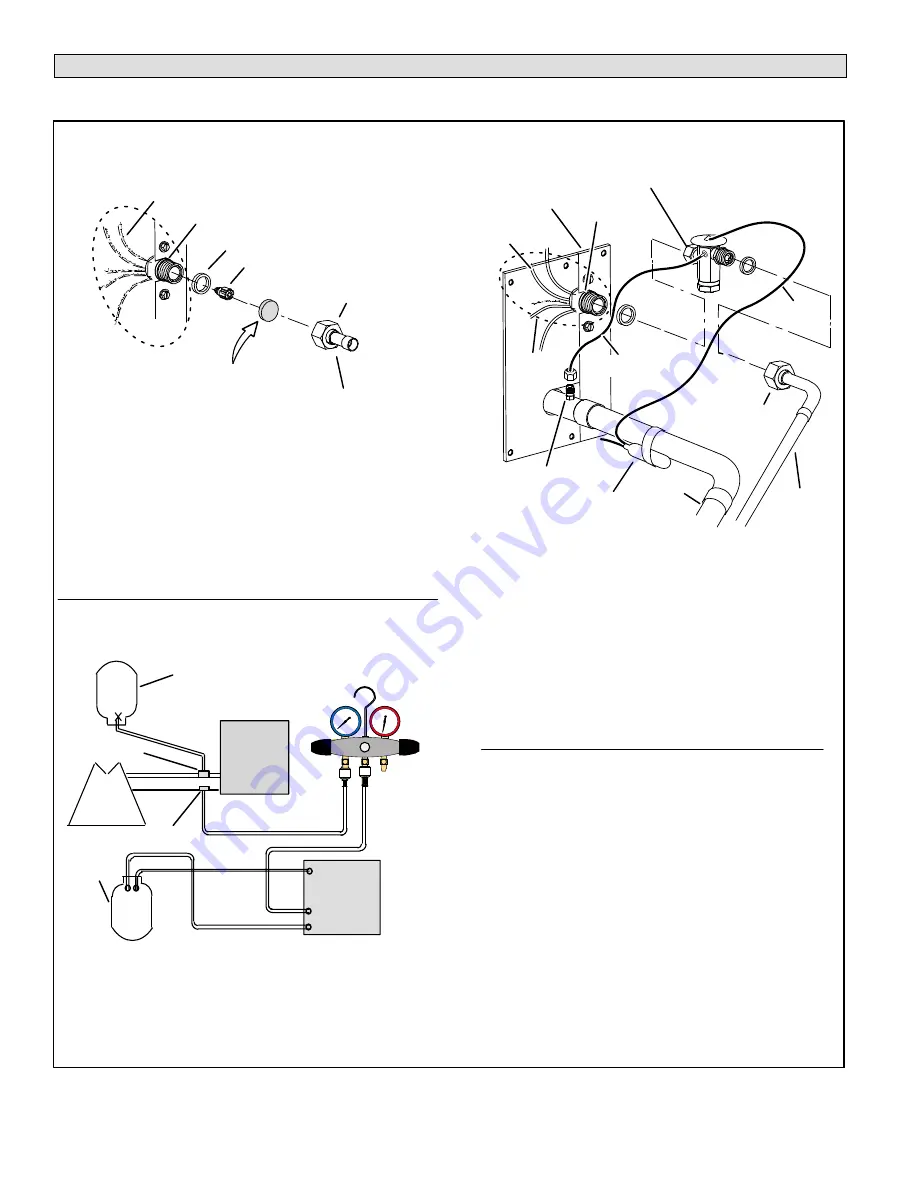
Page 12
506663−01 11/10
Flushing Line Set and Indoor Coil
Flushing is only required if existing indoor coil and line set are to be used. Otherwise proceed to
Installing Indoor Metering
Device
on page 13.
SENSING
LINE
TEFLON
®
RING
FIXED ORIFICE
BRASS NUT
LIQUID LINE ASSEMBLY
(INCLUDES STRAINER)
LIQUID LINE ORIFICE HOUSING
DISTRIBUTOR TUBES
DISTRIBUTOR
ASSEMBLY
REMOVE AND DISCARD
WHITE TEFLON
®
SEAL
(IF PRESENT)
A
On fully cased coils, remove the coil access and plumbing panels.
B
Remove any shipping clamps holding the liquid line and distributor as-
sembly.
C
Using two wrenches, disconnect liquid line from liquid line orifice hous-
ing. Take care not to twist or damage distributor tubes during this pro-
cess.
D
Remove and discard fixed orifice, valve stem assembly if present and
Teflon
®
washer as illustrated above.
E
Use a field−provided fitting to temporary reconnect the liquid line to the
indoor unit’s liquid line orifice housing.
TYPICAL EXISTING FIXED ORIFICE
REMOVAL PROCEDURE
(UNCASED COIL SHOWN)
TYPICAL EXISTING EXPANSION VALVE
REMOVAL PROCEDURE (UNCASED COIL
SHOWN)
TWO PIECE PATCH PLATE
(UNCASED COIL ONLY)
VAPOR
LINE
DISTRIBUTOR
ASSEMBLY
DISTRIBUTOR
TUBES
LIQUID
LINE
MALE EQUALIZER
LINE FITTING
EQUALIZER
LINE
CHECK
EXPANSION
VALVE
TEFLON®
RING
STUB END
TEFLON
®
RING
SENSING BULB
LIQUID LINE
ORIFICE
HOUSING
LIQUID LINE
ASSEMBLY WITH
BRASS NUT
A
On fully cased coils, remove the coil access and plumbing panels.
B
Remove any shipping clamps holding the liquid line and distributor
assembly.
C
Disconnect the equalizer line from the check expansion valve
equalizer line fitting on the vapor line.
D
Remove the vapor line sensing bulb.
E
Disconnect the liquid line from the check expansion valve at the liquid
line assembly.
F
Disconnect the check expansion valve from the liquid line orifice
housing. Take care not to twist or damage distributor tubes during this
process.
G
Remove and discard check expansion valve and the two Teflon
®
rings.
H
Use a field−provided fitting to temporary reconnect the liquid line to the
indoor unit’s liquid line orifice housing.
LOW
HIGH
EXISTING
INDOOR
UNIT
GAUGE
MANIFOLD
INVERTED CYLINDER
CONTAINS CLEAN TO
BE USED FOR
FLUSHING.
LIQUID LINE SERVICE
VALVE
INLET
DISCHARGE
TANK
RETURN
CLOSED
OPENED
RECOVERY
CYLINDER
RECOVERY MACHINE
NEW
OUTDOOR
UNIT
VAPOR LINE
SERVICE VALVE
V
APOR
LIQUID
1
A
Inverted cylinder with clean refrigerant to the vapor service valve.
B
gauge set (low side) to the liquid line valve.
C
gauge set center port to inlet on the recovery machine with an empty
recovery tank to the gauge set.
D
Connect recovery tank to recovery machines per machine instructions.
CONNECT GAUGES AND EQUIPMENT FOR
FLUSHING PROCEDURE
A
B
C
D
B
OR
FLUSHING LINE SET
A
Set the recovery machine for liquid recovery and start the
recovery machine. Open the gauge set valves to allow the
recovery machine to pull a vacuum on the existing system line
set and indoor unit coil.
B
Invert the cylinder of clean and open its valve to allow liquid
refrigerant to flow into the system through the vapor line valve.
Allow the refrigerant to pass from the cylinder and through the
line set and the indoor unit coil before it enters the recovery
machine.
C
After all of the liquid refrigerant has been recovered, switch the
recovery machine to vapor recovery so that all of the vapor is
recovered. Allow the recovery machine to pull down to 0 the
system.
D
Close the valve on the inverted drum and the gauge set valves.
Pump the remaining refrigerant out of the recovery machine and
turn the machine off.
The line set and indoor unit coil must be flushed with at least the
same amount of clean refrigerant that previously charged the
system. Check the charge in the flushing cylinder before
proceeding.
1A
2
3
1B
Figure 10. Removing Metering Device and Flushing