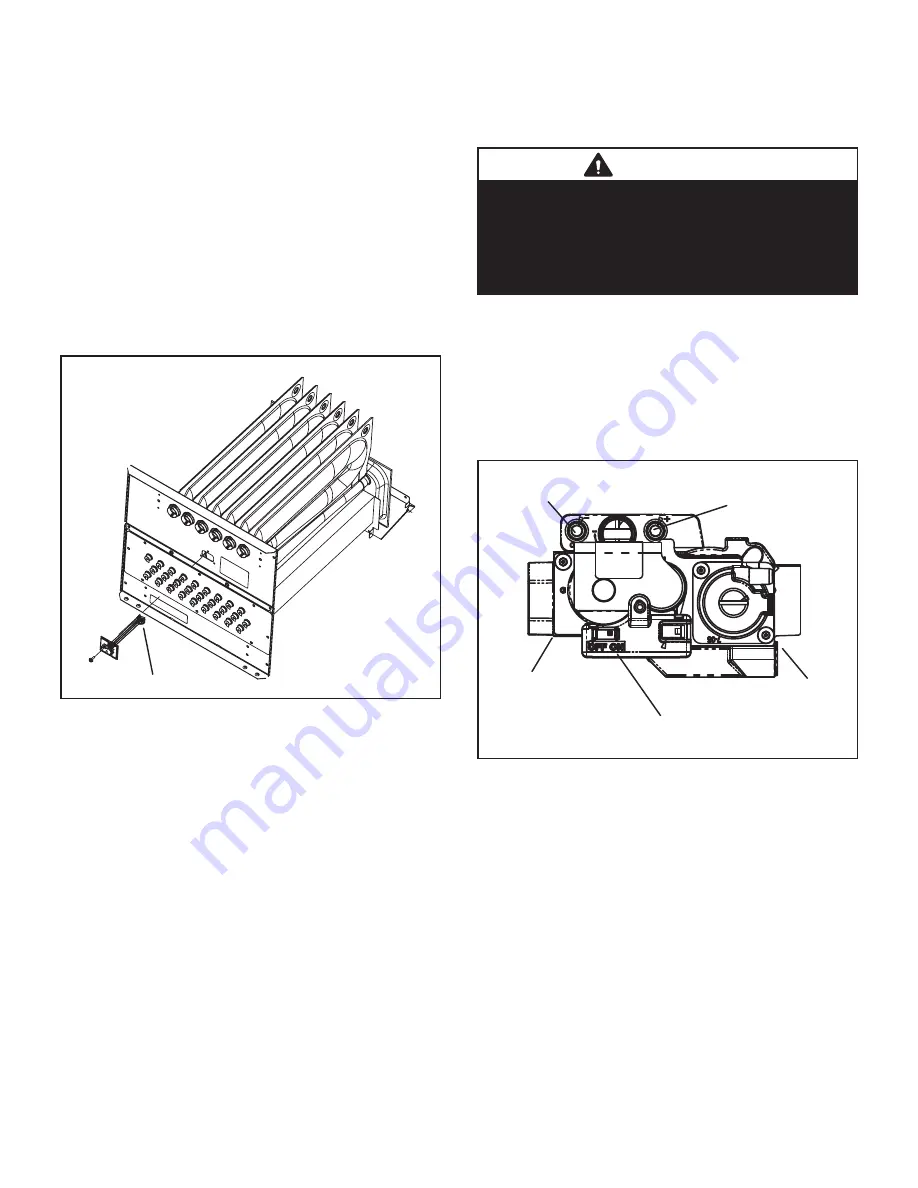
Page 31
6. Primary Limit Control (S10)
FIGURE 15 shows the primary limit (S10) used on
SLP99DFV units located in the heating vestibule panel.
When excess heat is sensed in the heat exchanger, the
limit will open. Once the limit opens, the furnace control
energizes the supply air blower and de-energizes the
gas valve. The limit automatically resets when unit tem-
perature returns to normal. The switch is factory set and
cannot be adjusted. In the event of restricted air flow, the
integrated control will reduce firing rate and indoor blower
airflow in 10% increments until a sustainable air flow is
reached. If the furnace reaches 35% firing rate, and ade
-
quate air flow is not available, the furnace will shutdown
and enter one hour watchguard. For limit replacement re-
move wires from limit terminals and rotate limit switch 90
degrees. Slowly remove from the vestibule panel.
Primary Limit Location and Heat Exchanger
install limit face down
FIGURE 15
7. Gas Valve (GV1)
Units use a variable capacity gas valve (figure 16) and
is applicable for two-stage or variable capacity settings.
See “Thermostat selection modes” in the integrated con-
trol section (section A- subsection 4.) for more details The
valve is internally redundant to assure safety shut-off. If
the gas valve must be replaced, the same type valve must
be used.
A 24VAC 2-pin plug and gas control switch are located on
the valve. 24V applied to the pins enables valve operation.
Inlet and outlet pressure taps are located on the valve.
LPG change over kits are available from Lennox. Kits in-
clude burner orifices and an LP gas valve.
DANGER
Danger of explosion.
There are circumstances in which odorant used
with LP/propane gas can lose its scent. In case of
a leak, LP/propane gas will settle close to the floor
and may be difficult to smell. An LP/propane leak
detector should be installed in all LP applications.
The burner box is sealed and operates under a negative
pressure. A pressure hose is connected from the burner
box to the gas valve. The gas valve senses the pressure in
the burner box and uses that to set the maximum manifold
pressure while the pressure switch with pressure condi-
tioning device adjusts the gas flow. This will compensate
for different vent configurations which can greatly affect
the rate of the unit.
GAS VALVE
NEGATIVE AIR
PRESSURE PORT
POSITIVE AIR
PRESSURE PORT
MANIFOLD
PRESSURE TAP
INLET
OUTLET
SUPPLY
PRESSURE
TAP
GAS VALVE SHOWN IN THE ON POSITION
FIGURE 16