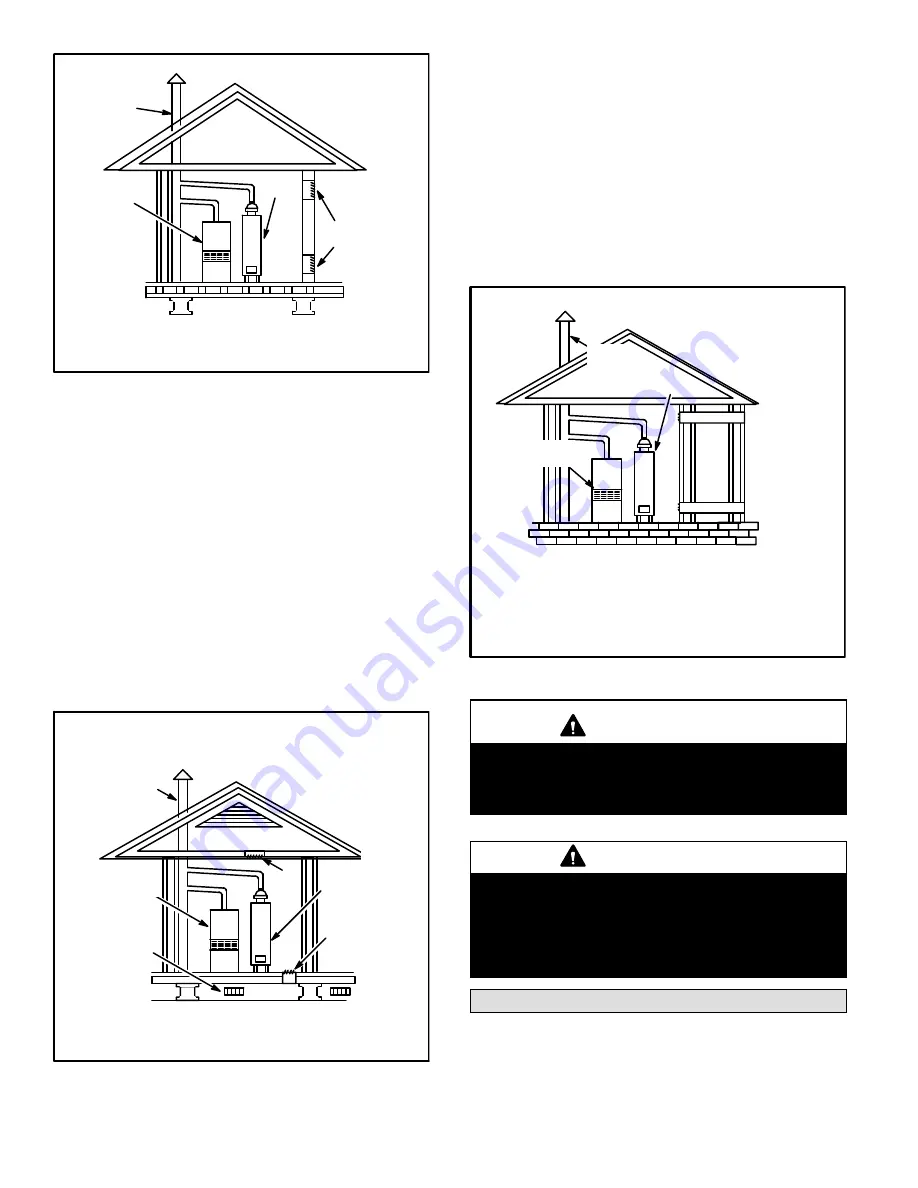
Page 6
Equipment In Confined Space
All Air From Inside
Chimney or
Oil Ven
t
Water
Heater
Openings
(To Adjacent Room)
Figure 4
NOTE-Each opening shall have a free area of at least 1 square inch
(6.4 square centimeters) per 1,000 Btu (293 W) per hour of the total
input rating of all equipment in the enclosure, but not less than 100
square inches
(614.5 square centimeters).
Oil
Furnace
Air from Outside
If air from outside is brought in for combustion and ventila
tion, the confined space shall be provided with two perma
nent openings. One opening shall be within 12” (305 mm)
of the top of the enclosure and one within 12” (305 mm) of
the bottom. These openings must communicate directly or
by ducts with the outdoors or spaces (crawl or attic) that
freely communicate with the outdoors or indirectly through
vertical ducts. Each opening shall have a minimum free
area of 1 square inch (6.4 square centimeters) per 4,000
Btu (1172 W) per hour of total input rating of all equipment
in the enclosure. (See figure 5.) When communicating with
the outdoors through horizontal ducts, each opening shall
have a minimum free area of 1 square inch (6.4 square
centimeters) per 2,000 Btu (586 W) per total input rating of
all equipment in the enclosure (See figure 6).
Ventilation
Louvers
(For unheated
crawl space)
Outlet
Ai
r
Equipment In Confined Space
All Air From Outside
(Inlet Air from Crawl Space and Outlet Air to
Ventilated Attic)
NOTE-The inlet and outlet air openings shall each have a free area of at
least one square inch (6.4 square centimeters) per 4,000 Btu (1172 W)
per hour of the total input rating of all equipment in the enclosure.
Ventilation Louvers
(Each End Of Attic)
Water
Heater
Inlet
Air
Chimney or
Oil Vent
Figure 5
Oil
Furnace
When ducts are used, they shall be of the same cross-sec
tional area as the free area of the openings to which they
connect. The minimum dimension of rectangular air ducts
shall be no less than 3” (76 mm). In calculating free area,
the blocking effect of louvers, grilles, or screens must be
considered. If the design and free area of protective cover
ing is not known for calculating the size opening required, it
may be assumed that wood louvers will have 20 to 25 per
cent free area and metal louvers and grilles will have 60 to
75 percent free area. Louvers and grilles must be fixed in
the open position or interlocked with the equipment so that
they are opened automatically during equipment opera
tion.
Equipment In Confined Space
All Air From Outside
Outlet Ai
r
Inlet A
ir
Water
Heate
r
Chimney
Or Oil
Vent
Figure 6
NOTE-Each air duct opening shall have a free area of at least one
square inch (6.4 square centimeters) per 2,000 Btu (586 W) per hour of
the total input rating of all equipment in the enclosure. If the equipment
room is located against an outside wall and the air openings communi
cate directly with the outdoors, each opening shall have a free area of at
least one square inch (6.4 square centimeters) per 4,000 Btu (1172 W)
per hour of the total input rating of all other equipment in the enclosure.
Oil
Furnace
CAUTION
Combustion air openings in the front of the furnace
must be kept free of obstructions. Any obstruction
will cause improper burner operation and may re
sult in a fire hazard or injury.
WARNING
The barometric draft control must be removed from
the vent pipe when using a combustion air adapter.
Deviation from this practice will cause improper
burner operation and may allow flue products into
the living space which may result in personal injury
or death.
Locate & Level the Unit
Set the unit in desired location keeping in mind the clear
ances listed in table 2. Also keep in mind oil supply connec
tions, electrical supply, flue connections and sufficient clear
ance for installing and servicing unit.