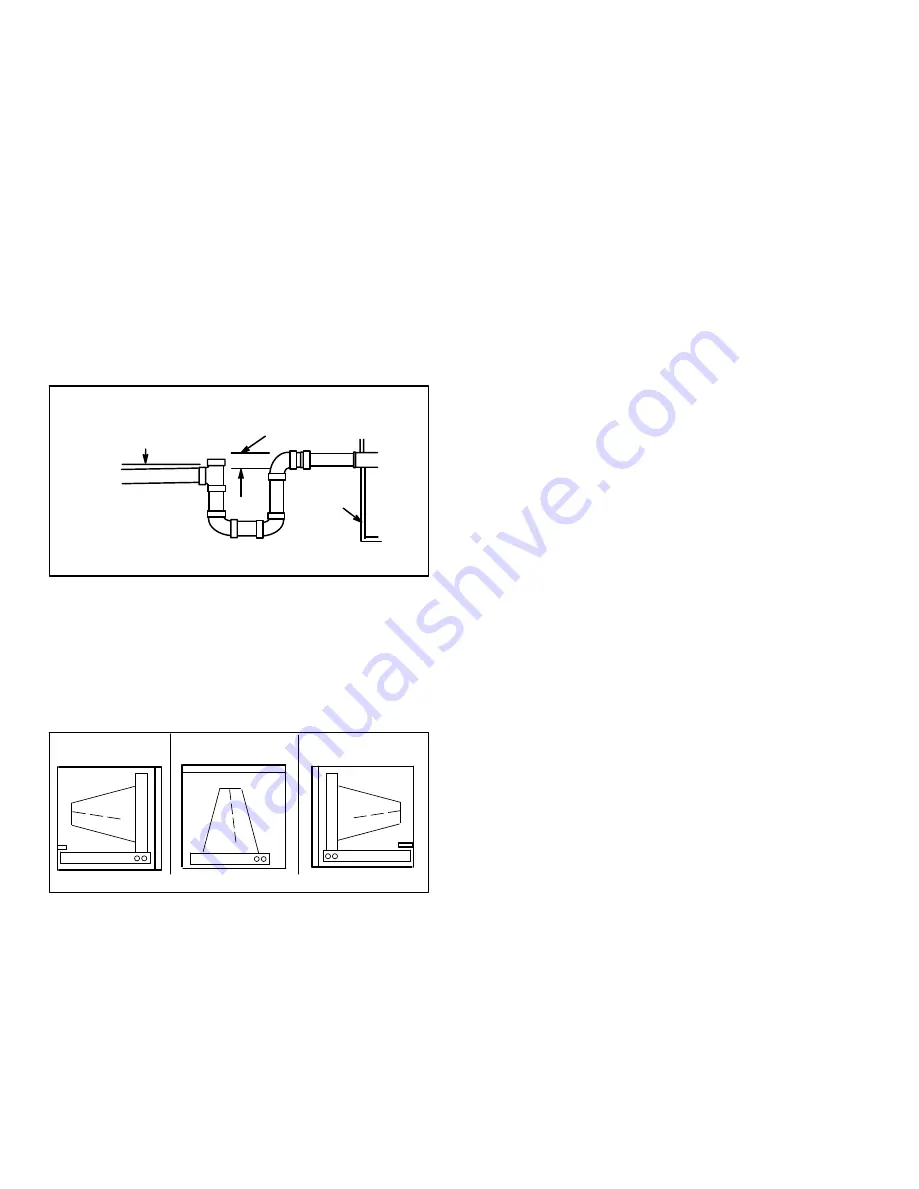
Page 32
12− Set unit so it is sloped toward the drain pan (1/4"
[6mm]). Connect return and supply air plenums as
required using sheet metal screws.
13− If hanging the unit, it must be supported along the entire
length of the cabinet. If using chain or strap, use a piece
of angle iron or sheet metal attached to the unit (either
above or below) so that the full length of the cabinet is
supported. Use securing screws no longer than 1/2"
(13mm) to avoid damage to coil or filter. See figure 25.
Connect return and supply air plenums as required
using sheet metal screws.
F−Condensate Drain
A 5" (127mm) section of PVC pipe is provided with the unit. Cut
the pipe in half and use to route the auxiliary and main drains.
Connect main condensate drain and route downward to an
open drain or sump. Do not connect drain to a closed waste
system. Refer to figure 30 for typical condensate trap
configuration.
FIGURE 30
MINIMUM 1 INCH (25 mm)
PITCH PER 10 FEET
(3048 mm) OF LINE
COIL
DRAIN
PAN
PIPE DIAMETER
DIFFERENCE
Trap must be deep enough to offset maximum static
difference (Generally, 2 inches [51mm] minimum).
TYPICAL CONDENSATE DRAIN CONNECTION
It is recommended that the auxiliary drain be connected to a
drain line for all units. If auxiliary drain is not connected,
it must be plugged with provided cap.
For downflow
units, the auxiliary drain MUST be connected and
routed to a drain.
See figure 31 for auxiliary and main
drain locations.
FIGURE 31
LEFT−HAND
DISCHARGE
MAIN DRAIN ON RIGHT
AUXILIARY DRAIN ON LEFT
UPFLOW OR
DOWNFLOW
RIGHT−HAND
DISCHARGE
The following practices are recommended to ensure
condensate removal:
1− Drain piping should not be smaller than the drain
connections at drain pan.
2− A trap must be installed in the main drain line.
3− The trap must be deep enough to offset the difference in
static pressure between drain pan and atmosphere.
Generally, two inches is satisfactory for medium static
applications.
4− Horizontal runs must be sloped 1" (25mm) per 10 feet
(3.1m) of drain line to offset friction.
5− An open vent in drain line will sometimes be required due
to line length, friction and static pressure.
6− Drains should be constructed in a manner to facilitate
future cleaning and not to interfere with filter access. See
figure 30.
7− Auxiliary drain should run to an area where homeowner
will notice it draining. Refer to local codes.
VII−START-UP − OPERATION
A−Preliminary and Seasonal Checks
1− Make sure the unit is installed in accordance with the
installation instructions.
2− Inspect electrical wiring, both field and factory installed for
loose connections. Tighten as required.
3−
Check voltage at disconnect switch. Voltage must be
within range listed on the nameplate. If not, consult the
power company and have voltage condition
corrected before starting unit.
4− Check to ensure that refrigerant lines are in good
condition and pipe insulation is intact.
5− Inspect condition of condensate drain pan and piping
assembly. Disassemble and clean seasonally.
B−Cooling Start-Up
NOTE−The following is a generalized procedure and
does not apply to all thermostat control systems. Electronic
thermostat control systems may operate differently.
1− Set fan switch to AUTO or ON and move the system
selection switch to COOL. Adjust the thermostat to a
setting far enough below room temperature to bring on the
compressor. Compressor will start and cycle on demand
from the thermostat.
2− The refrigerant circuit is charged with R410A
refrigerant. See condensing unit rating plate for
correct charge amount.
3− Refer to the correct condensing unit service manual for
more information.
C−Heating Start-Up
1− Set the fan switch to AUTO or ON and move the
system selection switch to HEAT. Adjust the
thermostat setting above room temperature.
2− The indoor blower immediately starts and the electric heat
will stage on based on sequence timing.
D−Safety or Emergency Shutdown
Turn off unit power at circuit breaker.
E−Extended Period Shutdown
Turn off thermostat or set to UNOCCUPIED" mode. Turn
off power to unit. All access panels and covers must be in
place and secured. The condensate assembly should be
clean and dry for extended period shutdown.