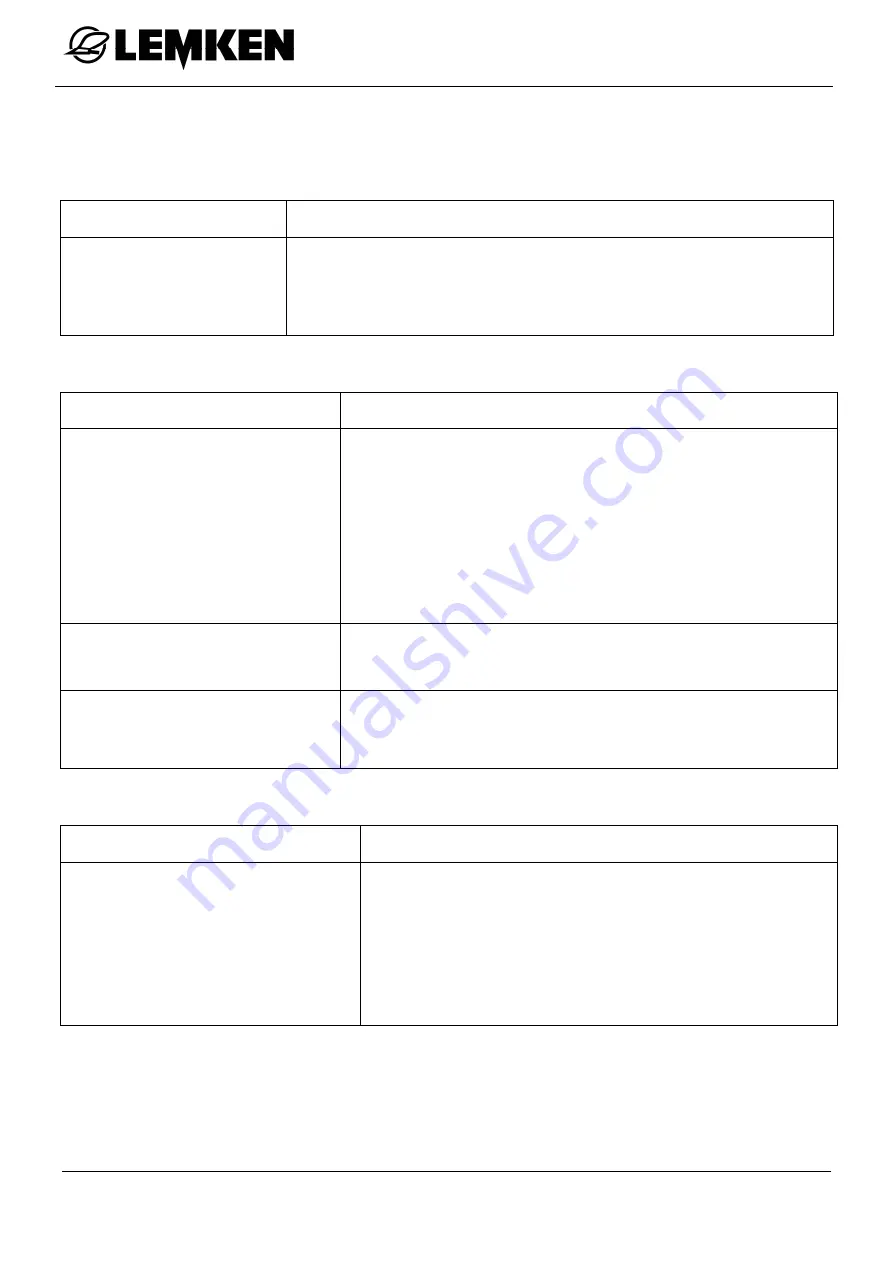
Maintenance and repairs
72
12.3 Maintenance
intervals
12.3.1 After commissioning (within 2 hours)
Check
What to do?
Screw connections
Retighten all bolts and nuts on the device to the ap-
propriate torque. See section entitled “Tightening tor-
ques”.
12.3.2 Daily check
Check
What to do?
Hydraulic hoses
Check hydraulic hoses for damage and leaks.
Replace damaged or defective hydraulic hoses im-
mediately.
The hydraulic hoses must be replaced 6 years after the
date of manufacture at the latest. Only used hydraulic
hoses approved by Lemken.
Safety equipment
Check that all safety equipment is functioning
properly. See "Safety equipment" section.
Soil processing tools
Check all soil processing tools for damage and wear.
Replace damaged or worn components.
12.3.3 Weekly check
Check
What to do?
Screw connections
Tighten all screws and nuts on the implement to
the appropriate tightening torque.
If necessary, secure the screw connections with
screw locking devices.
See section entitled “Tightening torques”.