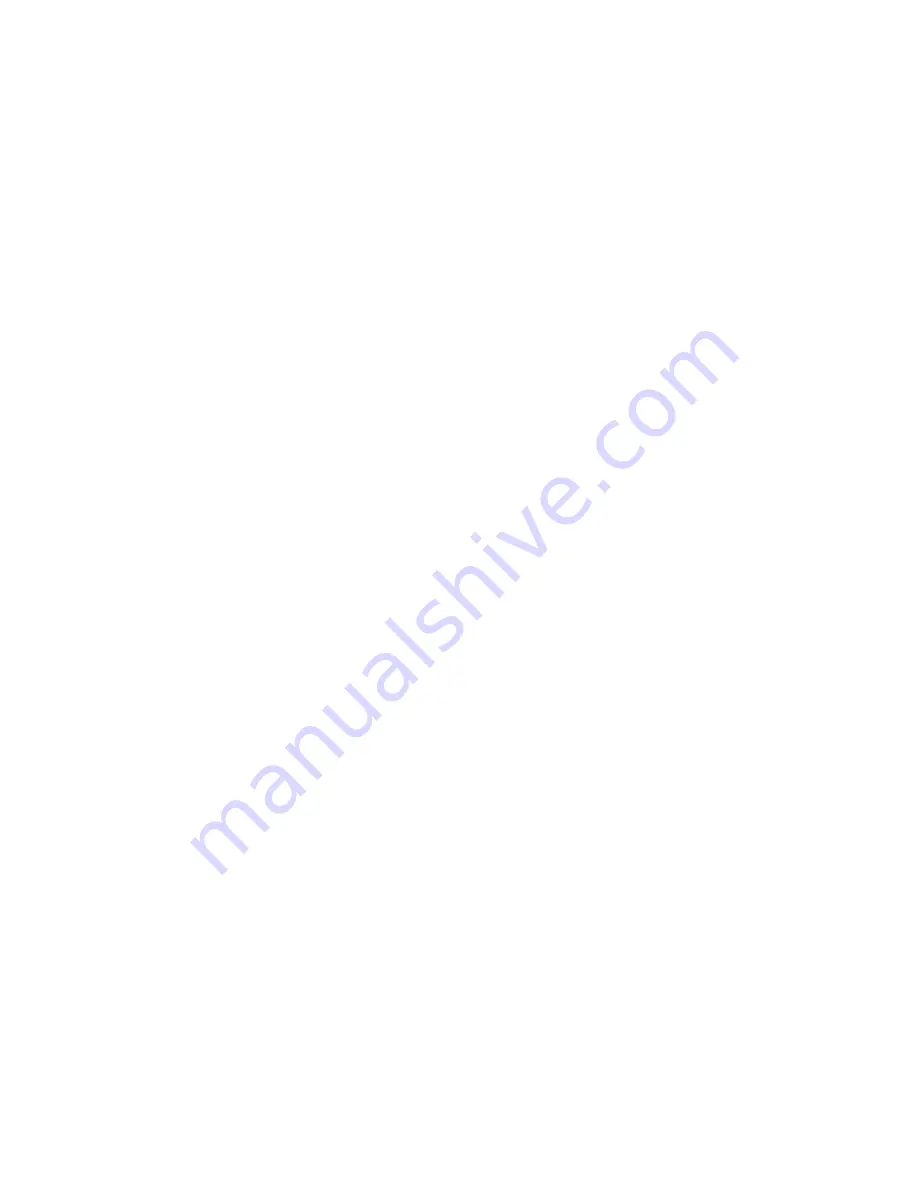
6
secure the heat shoes to the inside side panels near the
feed tray.Next,using a 9/64 allen wrench,loosen and remove
the two cap head screws and sleeves that secure the heat
shoe through the side panel near the center of the machine.
Cut the small white wire tie that secures the heater and heat
sensor wires to the side panel(they are covered with
black,heat shrink tubing).Now you can carefully lift out the
top heat shoe/threading guide/idler assembly to gain greater
access to the individual components.Using a phillips head
screw driver, remove the four flat head screws(and phenolic
spacers) that secure the heat shoe to the left and right heat
shoe brackets.This will allow you to swing the heat shoe
free to take a 5/64 allen wrench and loosen the set screw
that secures the heat sensor and bullet to the inside of the
heat shoe.This set screw is located in the center of the back
of the heat shoe,in line with the round head phillips screws
that hold the rubber roll heater in place.Extract the faulty
heat sensor/bullet from the inside of the shoe and replace
with new(part #’s PRC212S and 4285 061.4).Reassemble in
exact reverse sequence,rewire exactly as shown in the
schematic.Heat system should now be operational.
If not,the ribbon cable and heat control board are the only
components left to test and/or replace.Since there is no
easy way to accurately test the ribbon cable,your best bet is
to just replace it.Logically this will rectify any ribbon cable-
related problems.To replace the ribbon cable,and to gain
total access to the heat control board for testing and/or
replacement,the bottom motor cover must be removed.
With both housings removed,place the machine upside
down on your work bench.Using a phillips head screw