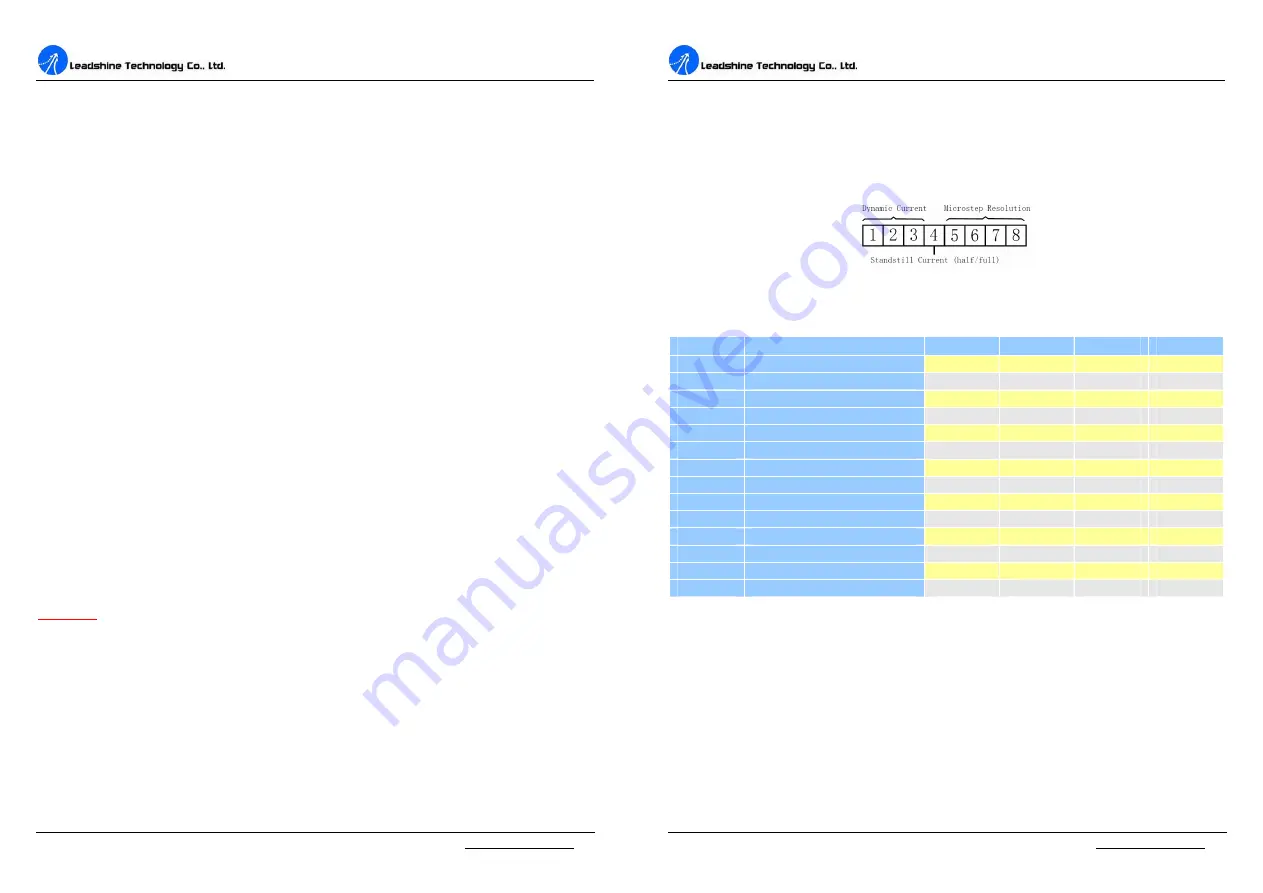
M880/M840 Microstepping Driver Manual V1.0
Tel: +086 0755-26434369 7 Web Site: www.leadshine.com
6. Power Supply Selection
The M880 and the M840 can match medium and small size stepping motors (from Nema size 17 to
43) made by Leadshine or other motor manufactures around the world. To achieve good driving
performances, it is important to select supply voltage and output current properly. Generally speaking,
supply voltage determines the high speed performance of the motor, while output current determines
the output torque of the driven motor (particularly at lower speed). Higher supply voltage will allow
higher motor speed to be achieved, at the price of more noise and heating. If the motion speed
requirement is low, it
’
s better to use lower supply voltage to decrease noise, heating and improve
reliability.
Regulated or Unregulated Power Supply
Both regulated and unregulated power supplies can be used to supply the driver. However,
unregulated power supplies are preferred due to their ability to withstand current surge. If regulated
power supplies (such as most switching supplies.) are indeed used, it is important to have large
current output rating to avoid problems like current clamp, for example using 4A supply for 3A
motor-driver operation. On the other hand, if unregulated supply is used, one may use a power supply
of lower current rating than that of motor (typically 50%
~
70% of motor current). The reason is that
the driver draws current from the power supply capacitor of the unregulated supply only during the
ON duration of the PWM cycle, but not during the OFF duration. Therefore, the average current
withdrawn from power supply is considerably less than motor current. For example, two 3A motors
can be well supplied by one power supply of 4A rating.
Multiple Drivers
It is recommended to have multiple drivers to share one power supply to reduce cost, if the supply
has enough capacity. To avoid cross interference,
DO NOT
daisy-chain the power supply input pins
of the drivers. (Instead, please connect them to power supply separately.)
Attention:
NEVER connect power and ground in the wrong direction, as it will damage the M880 or
the M840.
Selecting Supply Voltage
The power MOSFETS inside the M880 and the M840 can actually operate 24V
~
+80VDC,
including power input fluctuation and back EMF voltage generated by motor coils during motor shaft
deceleration. Higher supply voltage can increase motor torque at higher speeds, thus helpful for
avoiding losing steps. However, higher voltage may cause bigger motor vibration at lower speed, and
it may also cause over-voltage protection or even driver damage. Therefore, it is suggested to choose
only sufficiently high supply voltage for intended applications, and it is suggested to use power
supplies with theoretical output voltage of +24
~
+ 75V, leaving room for power fluctuation and
M880/M840 Microstepping Driver Manual V1.0
Tel: +086 0755-26434369 8 Web Site: www.leadshine.com
back-EMF.
7. Selecting Microstep Resolution and Driver Output Current
This driver uses an 8-bit DIP switch to set microstep resolution, and motor operating current, as
shown below:
Microstep Resolution Selection
Microstep resolution is set by SW5, 6, 7, 8 of the DIP switch
as shown in the following table:
Microstep
Steps/rev.(for 1.8
°
motor)
SW5
SW6
SW7
SW8
2
400
ON
ON
ON
ON
4
800
ON
OFF
ON
ON
8
1600
ON
ON
OFF
ON
16
3200
ON
OFF
OFF
ON
32
6400
ON
ON
ON
OFF
64
12800
ON
OFF
ON
OFF
128
25600
ON
ON
OFF
OFF
256
51200
ON
OFF
OFF
OFF
5
1000
OFF
ON
ON
ON
10
2000
OFF
OFF
ON
ON
25
5000
OFF
ON
OFF
ON
50
10000
OFF
OFF
OFF
ON
125
25000
OFF
ON
ON
OFF
250
50000
OFF
OFF
ON
OFF
Current Settings
For a given motor, higher driver current will make the motor to output more torque, but at the same
time causes more heating in the motor and driver. Therefore, output current is generally set to be such
that the motor will not overheat for long time operation. Since parallel and serial connections of
motor coils will significantly change resulting inductance and resistance, it is therefore important to
set driver output current depending on motor phase current, motor leads and connection methods.
Phase current rating supplied by motor manufacturer is important in selecting driver current, however
the selection also depends on leads and connections.
The first three bits (SW1, 2, 3) of the DIP switch are used to set the dynamic current. Select a setting