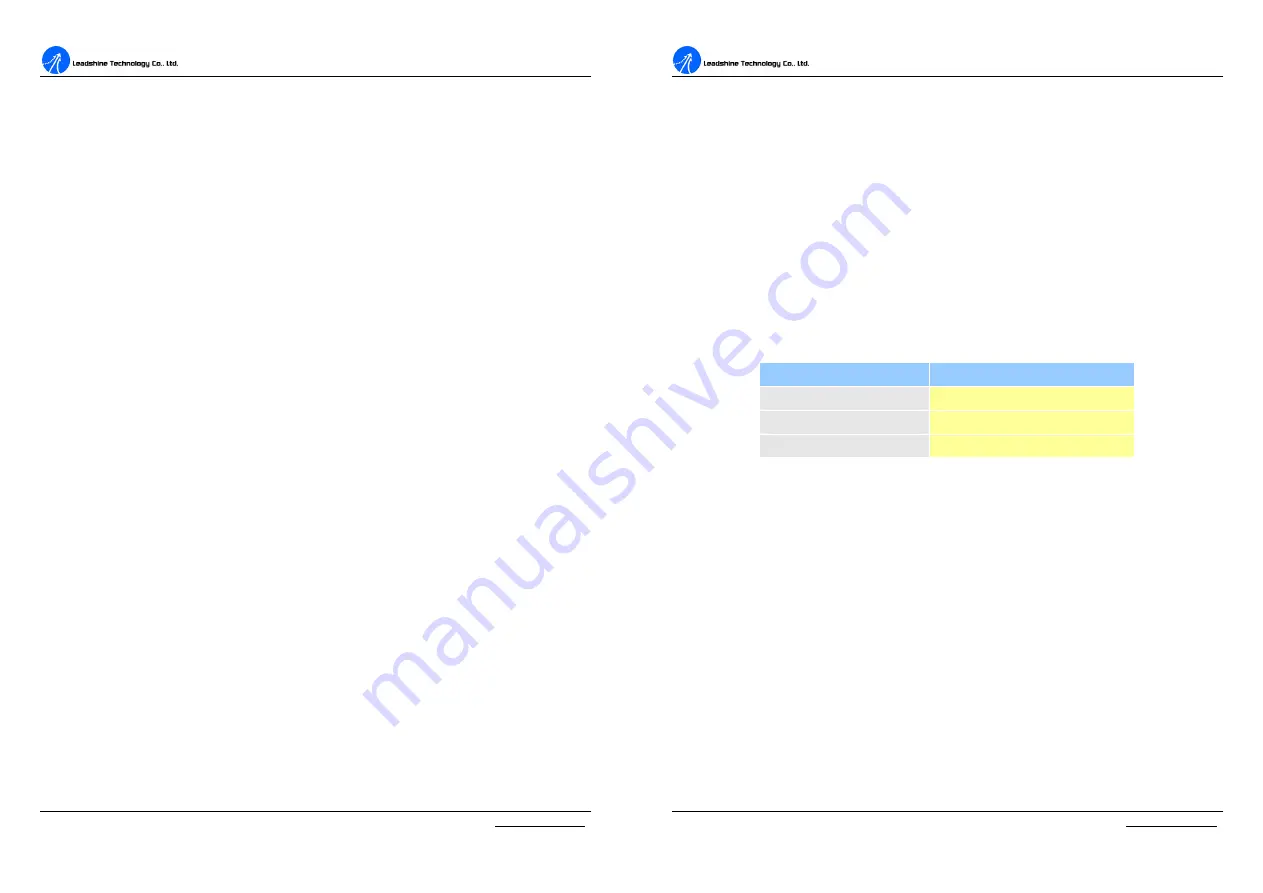
A
A
C
C
S
S
3
3
0
0
6
6
D
D
i
i
g
g
i
i
t
t
a
a
l
l
A
A
C
C
S
S
e
e
r
r
v
v
o
o
d
d
r
r
i
i
v
v
e
e
M
M
a
a
n
n
u
u
a
a
l
l
R
R
e
e
v
v
1
1
.
.
0
0
Prepare Power Supply
Regulated or Unregulated Power Supply
Both regulated and unregulated power supplies can be used to supply the Drive.
However, unregulated power supplies are preferred due to their ability to withstand
current surge. If regulated power supplies (such as most switching supplies.) are
indeed used, it is important to have large current output rating to avoid problems like
current clamp, for example using 4A supply for 3A motor-drive operation. On the
other hand, if unregulated supply is used, one may use a power supply of lower
current rating than that of motor (typically 50%
~
70% of motor current). The reason
is that the Drive draws current from the power supply capacitor of the unregulated
supply only during the ON duration of the PWM cycle, but not during the OFF
duration. Therefore, the average current withdrawn from power supply is
considerably less than motor current. For example, two 3A motors can be well
supplied by one power supply of 4A rating.
Selecting Supply Voltage
The ACS306 can actually operate within +20 ~ +30VDC, including power input
fluctuation and back EMF voltage generated by motor coils during motor shaft
deceleration. The rated voltage of the motor is an important parameter when selecting
supply voltage. Generally speaking, do not use a power supply voltage more than 5
volts of the rated voltage of the motor. Higher voltage may cause bigger motor
vibration at lower speed, and it may also cause over-voltage protection or even drive
damage.
Prepare Controller
Prepare a controller with pulse and direction signals. However, the ACS306 has a
built-in motion controller for self-test and Servo Tuning. The built-in motion controller
can generate pulse signal with trapezoidal velocity profile.
A
A
C
C
S
S
3
3
0
0
6
6
D
D
i
i
g
g
i
i
t
t
a
a
l
l
A
A
C
C
S
S
e
e
r
r
v
v
o
o
d
d
r
r
i
i
v
v
e
e
M
M
a
a
n
n
u
u
a
a
l
l
R
R
e
e
v
v
1
1
.
.
0
0
System Connections and Noise Prevention
After finishing the above steps, you can connect your servo system. Before you start,
make sure that the power is off. Connect your system according to previous
connection diagrams, and pay attention to the following tips when wiring.
Wire Gauge
The smaller wire diameter (lower gauge), the higher impedance. Higher impedance
wire will broadcast more noise than lower impedance wire. Therefore, when selecting
the wire gauge, it is preferable to select lower gauge (i.e. larger diameter) wire. This
recommendation becomes more critical as the cable length increases. Use the following
table to select the appropriate wire size to use in your application.
Current (A)
Minimum wire size (AWG)
10
#20
15
#18
20
#16
Cable Routing
All content sensitive signal wires should be routed as far away from motor power
wires and Drive power wires as possible. Motor power and Drive power wires are
major sources of noise and can easily corrupt a nearby signal. This issue becomes
increasingly important with longer motor power and Drive power wires lengths.
Twisted Wires
Twisted wires effectively increase noise immunity. The successive twists eliminate
noise transients along the length of the cable. Both signal cables and power cables
should be of the twisted and shielded type. Differential signal wires should be twisted
as a pair. The combination of twisted pair wires and a differential signal significantly
adds to noise immunity. Power wires should be twisted as a group along with the
ground (or chassis) wire, if available.
Содержание ACS306
Страница 13: ......