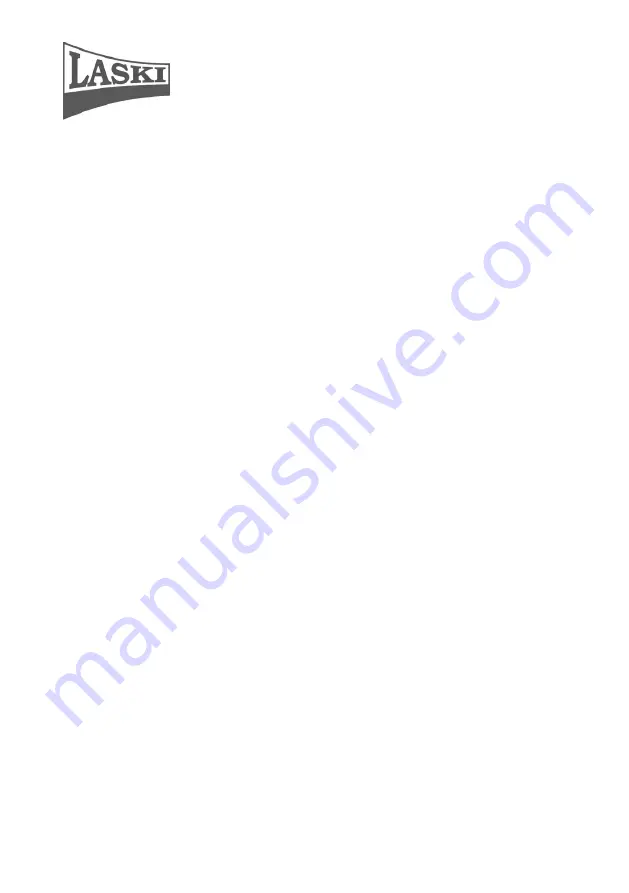
Chipper LS 160T
32
-
Do not load materials with parts of metal, glass, ceramics and other similar
objects.
-
Do not chip or load materials while driving.
-
Having put materials in the loading chute/between loading rolls, release the
loaded material immediately and keep a certain distance from the chute.
-
Do not load materials with diameters exceeding 160 mm and 3 m in length. Do
not load wooden boards with thickness more than 60 mm.
-
When working, never lean over the loading chute and never pull out wooden
materials, already loaded, from the chute.
-
Do not load materials with diameters exceeding 160 mm. Speed of loading
should correspond with quantity and characteristics of the material to be
loaded.
-
If loaded materials are spreading with risks of catch holding of attendant's
dress being drawn in the loading chute then it is necessary to prepare such
materials accordingly (trimming, cutting).
-
Pay special attention to thorny materials, such as acacia and roses, which may
easily catch your sleeves.
-
Be careful while loading since materials may unexpectedly move in unwished
directions.
-
In case of two attendants it is necessary to make simple signals clear before
working. During operation it is not easy to make any agreements because of
operating noise.
-
Observe the working area. If any person, children or animals approach while
chipping, then stop working immediately.
-
Be aware that there is a certain time period required between loading, chipping
and final ejection of chips.
-
As far as possible load the chipper evenly, adapt loading speed accordingly
and keep continuous chipping.
-
While loading, stand aside the loading chute.
-
While loading short materials, throw them in the chute and push them forward
between the loading rolls by means of a wooden stick or a board, more than
160 cm long, to push materials between the loading rolls.
-
Never use metal objects. They could cause serious damage of the loading rolls
and blades.
-
When finishing the work, first wait for emptying of the loading chute.
Содержание LS 160
Страница 1: ...Orig version 11 2016 OPERATING INSTRUCTIONS CHIPPER LS 160 model LS 160T...
Страница 5: ...Chipper LS 160T 5...
Страница 6: ...Chipper LS 160T 6...
Страница 52: ...Chipper LS 160T 52 Service Report...
Страница 53: ...Chipper LS 160T 53 Hydraulic scheme...
Страница 54: ...Chipper LS 160T 54 ELEKTRICK ZAPOJEN ELEKTRISCHE SCHEMA WIRING DIAGRAM...
Страница 55: ...Chipper LS 160T 55 ELEKTRICK ZAPOJEN ELEKTRISCHE SCHEMA WIRING DIAGRAM...