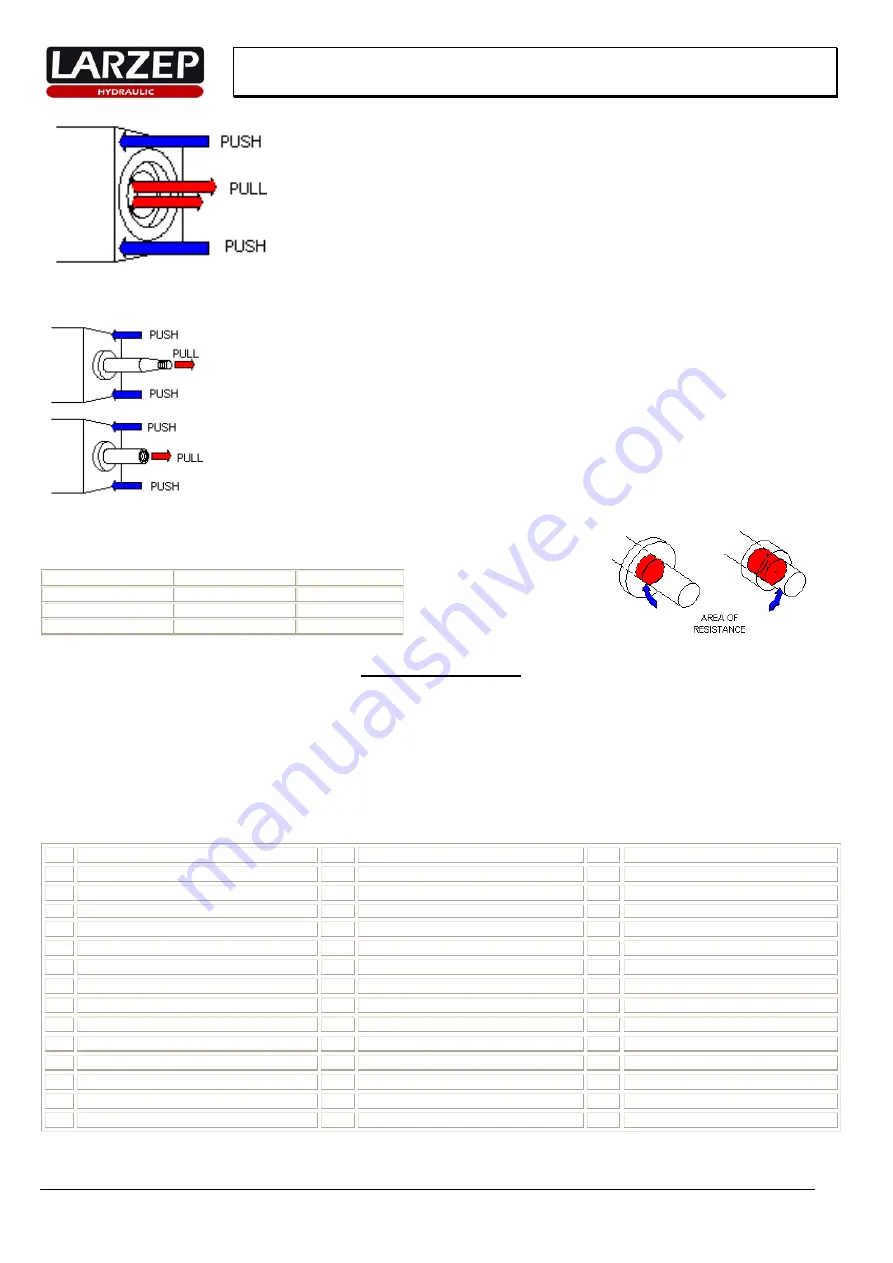
5
Instruction Manual
Hydraulic Pullers
To grip and pull an internal bearing:
Place the (FI) Bearing Cup Puller inside the bearing to be pulled, check the puller is centred.
Use the internal puller FI in combination with the FZ o FT models.
To grip and pull a shaft from housing:
Fasten to the threaded male end of the shaft to pull while pushing against the housing.
Use the thread of the shaft to tighten the puller and this way pull while pushing against the housing.
How to choose the capacity of a puller
For hydraulic pullers, the maximum
force exerted in tons should be 7 times the diameter of the shaft in
inches.
Shaft diam. in inches
Shaft diam. in mm
Cap. Puller in Tons
0" - 2"
0 - 50
20
2" - 3 1/2"
50 - 87
30
3 1/2" - 5 1/2"
87 - 136
50
5. MAINTENANCE.
o
All the maintenance operations must be done with depressurized equipment and disconnected hydraulic and electrically.
o
Always use
LARZEP
original spare parts.
o
In every use of the equipment make a visual inspection; check the oil level, damages in hydraulic part (scratched piston, thread, leaks, etc.), the condition
of the accessories.(hoses, couplers, etc.)
o
Clean the equipment after each use and keep grease critical areas: threads, shafts, inside the roller, piston, etc. before store the equipment in the box.
o
In case of frequent use, replace periodically the hoses and couplers although they do not seem damaged.
o
Periodically (at least once to the year), replace the hydraulic oil of the tank by clean oil.
o
The oil filling it’s made through the plug. Check the level with the dipstick placing the pump head down in vertical position. Use L
ARZEP AZ8901 oil.
o
The maintenance operations or repairs that suppose the dismantling of the mechanical parts of the equipment (jack, cylinder or pump) must be done by
specialist personnel.
PROBLEM
DIAGNOSIS
SOLUTION
1
The piston of the cylinder does not advance.
1.1
Excess or lack of oil in the tank.
1.1
Check the level and refill.
1.2 Clogged
filter.
1.2 Dismantle the pump and clean it.
1.3
Oil leak by the admission ball of the pump.
1.3
Repair the ball seat and replace the ball.
1.4
Pressure collar of the cylinder damaged.
1.4
Replace the detent.
1.5
Cup of the pump damaged.
1.5
Replace the collar.
1.6
Pressure relief valve of the pump unrated.
1.6
Rate the valve.
1.7
A bad connection of the hose.
1.7
Check the connection.
2
The cylinder does not reach pressure.
2.1
Pressure collar of the cylinder damaged.
2.1
Replace the detent.
2.2
Leak by the ball of the action screw.
2.2
Repair the ball seat and replace the ball.
2.3
Oil leak by the admission ball of the pump.
2.3
Repair the ball seat and replace the ball.
3
The piston does not return.
3.1
Ball of the action screw pasted.
3.1
Release the screw and move the ball.
3.2
Jamming or twisted piston in the cylinder.
3.2
Repair or replace the piston.
3.3
Damaged spring in the cylinder.
3.3
Replace the spring.
3.4
Excess of oil in the tank.
3.4
Check the level.
The solutions in black must be carried out by specialist personnel.