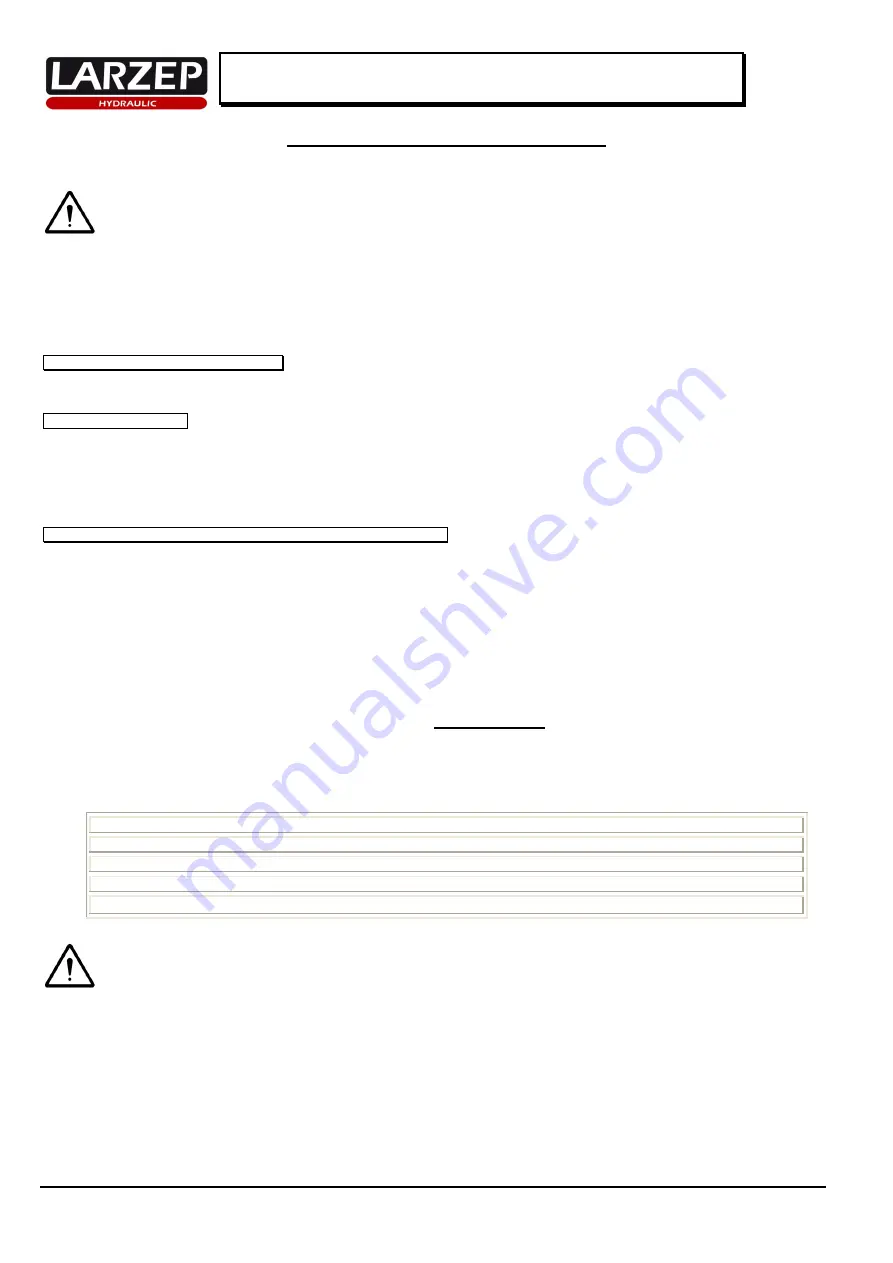
4
Instruction Manual
Column Press with Electric Pump “EE12018”
4. TRANSPORT AND INSTALLATION.
The machine is delivered properly packed in a wooden ballet. For it’s handling, it is recommended to use a forklift truck or a crane. In the last case, it is necessary to
make the slings trespass the arc of the frame. When doing this operation, you should be cautious and prevent the flexible hoses and couplings from any damage.
The machine is stable enough to operate without fixing, but if is placed in an area commonly operated by mobile machinery (cranes, lifting equipment…)
it is strongly recommended to fix it to the desired place by drilling the supporting plates.
ELECTRIC CONNECTION
Bear in mind the voltage indicated in the terminal box of the motor.
Assure that the directional distributor valve’s command is in position “C”.
Check that the motor rotates in the sense of the arrow labelled in the electrical motor. In opposite case, change the position of two cables between themselves in the
terminal and try again. This operation will be made with the equipment depressurized.
SUBSTITUTION OF THE TRANSPORT PLUG
Replace the plug of transport located in the cover of the tank, by the pressurized plug given with the press. (Plastic bag in the lever of the valve).
INSTALLING THE GAUGE
1-Replace the threaded tap in the top of the cylinder by the gauge. (Supplied separately).
2-Tighten the gauge cone to the gauge adaptor seat by using a flan wrench size 22.
3-Hold the gauge screen by hand during threading process and after reaching a comfortable reading position set the gauge screen free so that it turns the last quarter
solidarily with the thread.
4- The hydraulic system also includes a gauge adaptor with 3/8 “BSP thread.
CHECKING THE RIGHT OPERATION OF ALL DEVICES AND MECHANISM
1.
Put the distributor valve’s command in position “C” and push the start switch button (black) of the electrical cabinet.
2.
Check the rotate of the motor.
3.
If the rotate sense is the opposite of the labelled arrow in the motor, change the phases of the electrical connection. Disconnect the equipment for this
operation.
4.
Put the distributor valve’s command ion “A” position. The cylinder’s piston advances, familiarize with the speed.
5.
Guide the piston to the end of the stroke and submit to pressure, check the reading of the gauge and that there is not oil leaks.
6.
Put the distributor valve’s command in “C” position to assure that the cylinder maintains the pressure.
7.
Put the distributor valve’s command in “B” position to return the piston, familiarize with the speed.
8.
Push the stop switch (red) of the electrical cabinet, to stop the motor. Move the command from “A” position to “B” position to depressurize the cylinder
and finally let the distributor valve’s command in “C” position.
5. START UP.
Connect the machine as explained in the previous point.
Displacement of the table’s height:
MODEL EE122018
Choose the wished height.
Elevate the table rotating the lever of the winch to the right, until let free the pins and extract them.
Put the table in the wished height, let free the holes of the columns in order to introduce the pins.
Descend the table by means of the winch, until the table is perfectly supported in the pins and the cables of the winch must be without tension.
VERY IMPORTANT! THE POSITIONING SYSTEM OF TEH TABLE IS NOT DESIGNED TO RESIST THE FORCE THAT THE CYLINDER IS
ABLE TO DO. THE USE IS ONLY IN ORDER TO POSITIONING THE TABLE.
Regulation of the maximum working pressure:
The maximum pressure developed by the hydraulic system is 700 Kg/cm
. An internal limiter valve races in the moment that the installation reaches the pressure.
If the working pressure wished is inferior, act in the following sense:
1.
In the cover of the power pack is located the pressure regulation screw.
2.
Release the lock nut and go releasing the regulation screw. Go checking with the gauge and once the pressure wished is reached, tighten the lock nut to
avoid that the vibrations deregulate the system.