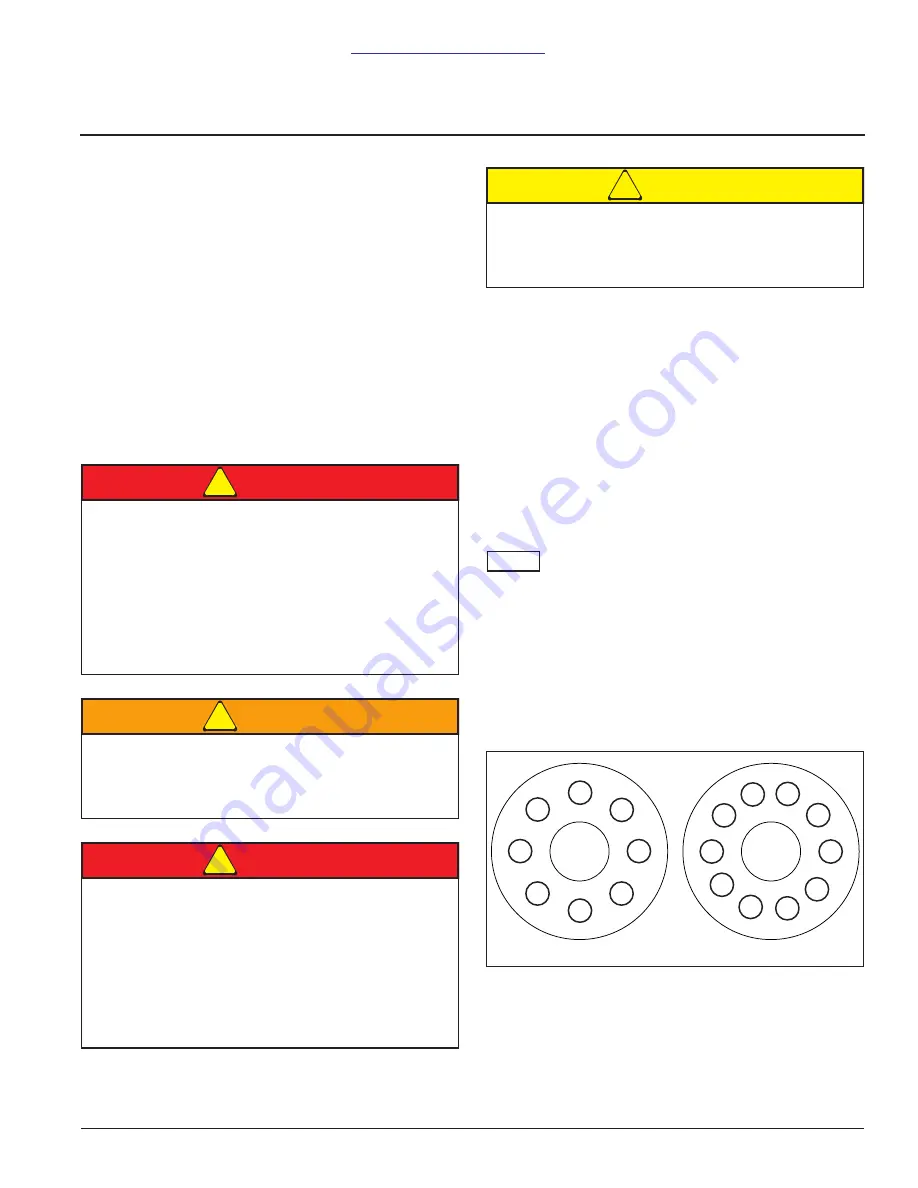
3-1
Chapter 3
Assembly Instructions
It is very important that your new 7822 High Speed
Landoll () be properly assembled, adjusted and
lubricated before use. Illustrations in this section show
proper assembly procedures. Remove paint from grease
fittings. Replace any grease fittings that are damaged or
missing. Be sure to return screws, clips, etc., to their
original locations.
To ensure alignment of assemblies,
leave the nuts
loose until completion
of final assembly. Use lock
washers or flat washers as specified. Spread all cotter
pins.
After completion of final assembly, tighten all nuts
evenly
to prevent misalignment, distortion or binding.
Tighten all screws and nuts to the recommended torques
shown in
“General Torque Specifications (rev. 4/97)”
DANGER
WARNING
DANGER
CAUTION
Unloading the HSL and
Final Assembly
I
n most cases the 7822 has come to you with the main
wheels and tires shipped loose due to shipping width,
restrictions.
1.
Install the main wheels and tires to the hitch
rockshaft hubs.
2.
Due to the being a towed implement the tire tread is
typically installed opposite of that of a tread where
power would be applied through it.
NOTE
There is a protruding step on the hub pilot. The wheel
center plate must fit over the hub pilot and then bottom
out against the hub flange. Failure to get the wheel
properly positioned against the hub face will cause the
wheel to loosen and cause damage to the hub and/or
wheel.
3.
With the tire and wheel assembly correctly positioned
against the hub, begin to tighten the flange nuts
sequentially as shown below.
Figure 3-1: Lug Nut Tightening Sequence
4.
Re-check the positioning of the wheel relative to the
hub and proceed by tightening the lug nut assemblies
sequentially to 450 to 500 foot pounds.
Disc blades are extremely sharp. Exercise
extreme care when working on or near disc
blades. Do not allow discs to roll over or fall onto
any bodily part. Do not allow wrenches to slip
when working near disc blades. Never push
wrenches toward disc blades. Do not climb over
machine above disc blades. Failure to stay clear
of disc blade edges can cause serious personal
injury or death.
Do not attempt to lift heavy parts (such as the
frame, disc gangs, rockshaft, and pull hitch)
manually. Use a hoist or a fork lift to move these
parts into position.
To prevent accidental lowering:
•
All hydraulically elevated equipment must be
locked out using the cylinder lockouts.
•
Lower equipment to the ground while
servicing or when it is idle.
Failure to take measures to prevent accidental
lowering may result in serious personal injury or
death.
Be sure to bleed the hydraulic system of all air in
lines after installation. Failure to bleed the system
of all air can result in improper machine
operation.
8 Stud Hub
10 Stud Hub
2
3
4
5
6
7
8
1
2
3
4
5
6
7
8
9
10
1
Содержание 7822 Series
Страница 2: ...Manuals for 7822 HSL Manual Number Manual Name F 1045 Operator s Manual F 1034 Parts Manual ...
Страница 12: ...2 4 F 1045 0819 STANDARD SPECIFICATIONS TABLE OF CONTENTS NOTES ...
Страница 16: ...3 4 F 1045 0819 ASSEMBLY INSTRUCTIONS TABLE OF CONTENTS NOTES ...
Страница 32: ...5 4 F 1045 0819 TROUBLESHOOTING TABLE OF CONTENTS NOTES ...