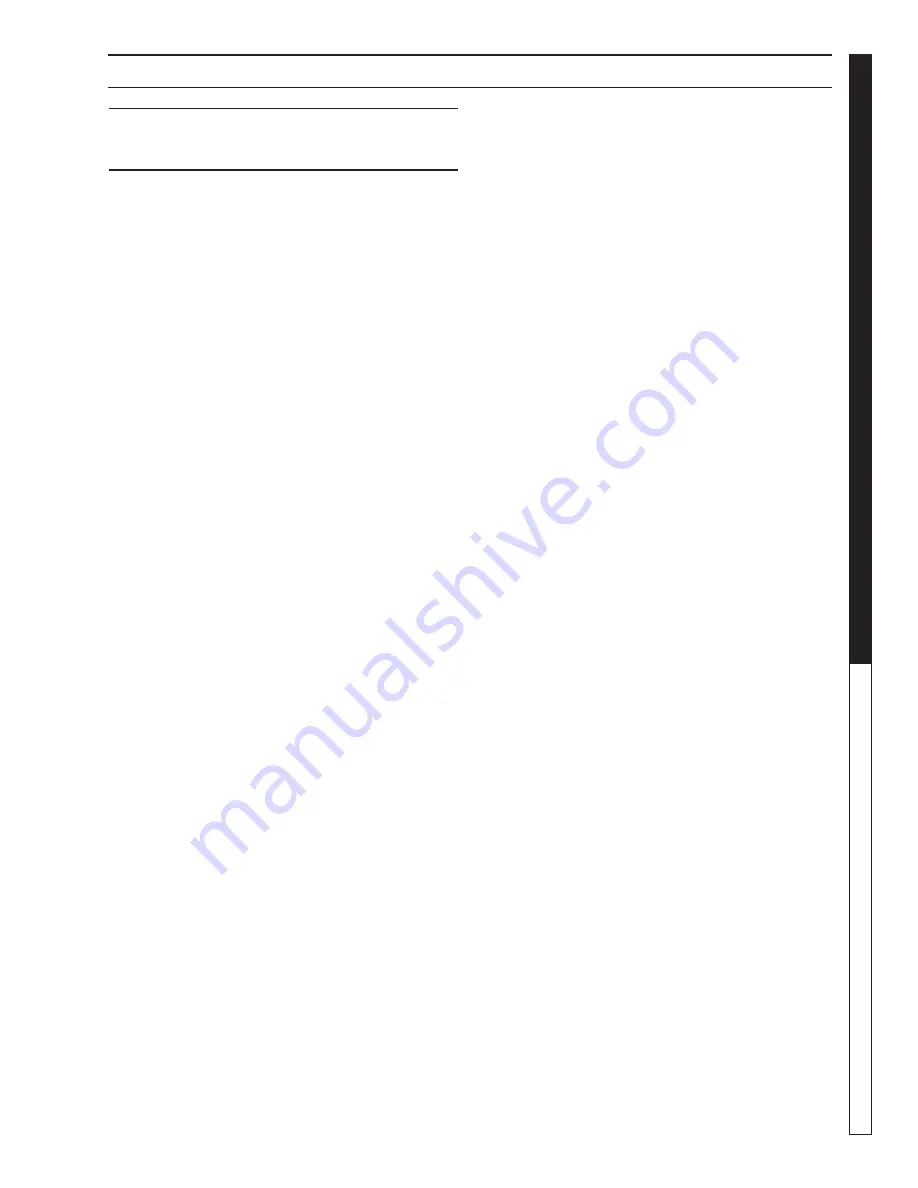
Landa SLT/SLX • Gas 8.914-002.0 • Rev. 4/13
13
PRESSURE
W
ASHER
OPERA
TOR’S MANU
AL
MAINTENANCE & SERVICE
PREVENTATIVE
MAINTENANCE
• Check to see that water pump is properly
lubricated.
• Follow winterizing instructions to prevent freeze
damage to pump and coils.
• Always neutralize and flush detergent from system
after use.
• If water is known to be high in mineral content, use
a water softener on your water system, or de-scale
as needed.
• Do not allow acidic, caustic or abrasive fluids to
be pumped through system.
• Always use high grade quality cleaning
products.
• Never run pump dry for extended periods of time.
• Use clean fuel-kerosene, No. 1 fuel oil, or diesel.
Clean or replace fuel filter every 100 hours of
operation. Avoid water contaminated fuel as it will
damage the fuel pump.
• If machine is operated with smoky or eye burning
exhaust, coils soot up and prevent water from
reaching maximum operating temperature. (See
section on Burner Adjustments.)
• Never allow water to be sprayed on or near
the engine or burner assembly or any electrical
component.
• Periodically delime coils per instructions.
• Check to see that engine is properly lubricated.
It is advisable, periodically, to visually inspect the
burner. Check air inlet to make sure it is not clogged
or blocked. Wipe off any oil spills and keep this equip-
ment clean and dry.
The flow of combustion and ventilating air to the burner
must not be blocked or obstructed in any manner.
The area around the Landa washer should be kept
clean and free of combustible materials, gasoline and
other flammable vapors and liquids.
Unloader Valves
Unloader valves are preset and tested at the factory
before shipping. Tampering with factory setting may
cause personal injury and/or property damage, and
will void the manufacturer's warranty.
Winterizing Procedure
Damage due to freezing is not covered by warranty.
Adhere to the following cold weather procedures when-
ever the washer must be stored or operated outdoors
under freezing conditions.
During winter months, when temperatures drop be-
low 32°F, protecting your machine against freezing
is necessary. Store the machine in a heated room. If
this is not possible then mix a 50/50 solution of anti-
freeze and water in the float tank. Turn the engine on
to siphon the antifreeze mixture through the machine.
If compressed air is available, an air fitting can be
screwed into the float tank by removing the float tank
strainer and fitting. Inject the compressed air. Water
will be blown out of the machine when the trigger on
the spray gun is opened.
High Limit Hot Water Thermostat
For safety, each machine is equipped with a tempera-
ture sensitive high limit control switch. In the event that
the water should exceed its operating temperature, the
high limit control will turn the burner off until the water
cools then automatically reset itself. The thermostat
sensor is located on the discharge side of the heat-
ing coil. The thermostat control dial is located on the
control panel.
Pumps
Use only SAE 20/40 weight non-detergent oil. Change
oil after first 50 hours of use. Thereafter, change oil
every three months or at 500 hour intervals. Oil level
should be checked through use of dipstick found on top
of pump, or the red dot visible through the oil gauge
window. Oil should be maintained at that level.
Cleaning of Coils
In alkaline water areas, lime deposits can accumulate
rapidly inside the heating coil. This growth is increased
by the extreme heat build up in the coil. The best
prevention for liming conditions is to use high quality
cleaning chemicals. In areas where alkaline water is
an extreme problem, periodic use of Landa Deliming
Powder (Landa Part #9-028008) will remove lime and
other deposits before coil becomes plugged.
Deliming Coils
Periodic flushing of coils or optional float tank is rec-
ommended.
Step 1 Fill a container with 4 gallons of water, then
add 1 lb. of deliming powder. Mix thoroughly.
Pour mixture into float tank.
Step 2 Remove wand assembly from spray gun
and put spray gun into float tank. Secure
the trigger on the spray gun into the open
position.
Step 3 Turn engine on, allowing solution to be
pumped through coils back into the float
tank. The solution should be allowed to
circulate 2-4 hours or until the color changes.