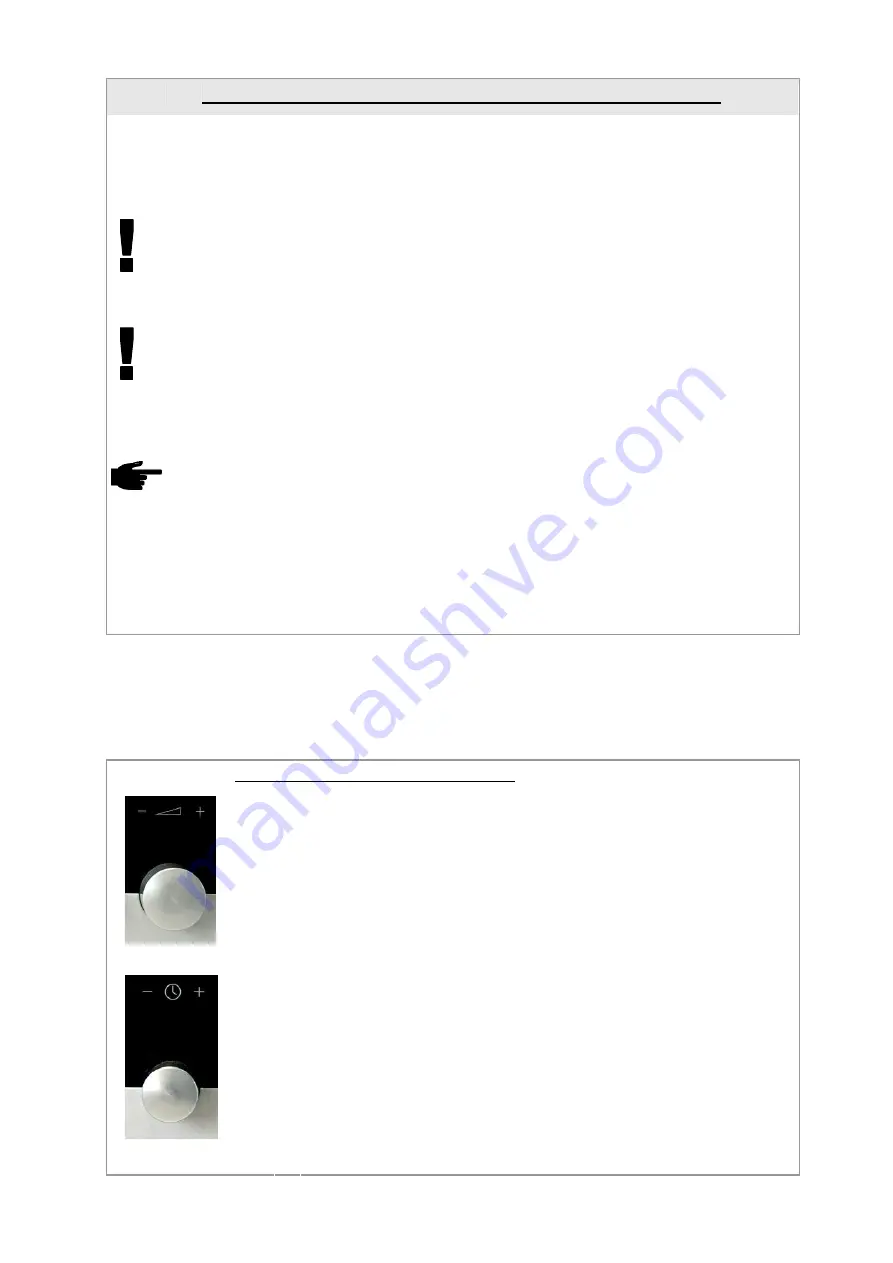
10
5
OPERATING PRINCIPLES AND SETTING THE PARAMETERS
After being switched on and running the self-test, the machine will start from its initial
settings:
Standard mode, 7 ms impulse length/welding time, and a low power setting.
The initial settings for mode, welding time and power, correspond to the blue LEDs in the
display. The display also has blue LEDs to mark the entire parameter range.
Important !
At the outset, until a basic proficiency is reached, we recommend to only change the
parameter welding power, leaving the welding time constant. After a short time, when
you have become more confident with the technique and have gained more experience,
then you can naturally also change the welding time to suit your needs.
The machine automatically saves the last three sets of welding parameters that
have been used.
By pressing in the rotary knob “Impulse length / welding time” (3), these previous settings
can be recalled one after another.
Even when the machine is switched on, or after accidentally changing the parameters,
the settings that were last used are there to be recalled again.
Please note !
Please remember that only when the gas flow rate has been correctly set up and
adjusted, can good welding results be achieved.
To adjust the gas flow to the correct amount, press in and hold the rotary knob – welding
power (4). (The gas valve in the machine will now be open and the gas will flow freely).
Without letting go of the rotary knob – welding power (4), adjust the Flowmeter regulator
to the correct flow rate ca.
2
litres per minute.
5-1
SETTING THE WELDING PARAMETERS
Power:
The welding power (potency of the welding energy), can be set by
adjusting the rotary knob – welding power (4)
The size and intensity of the welding spot can thus be governed.
Welding time:
Using the rotary knob – Impulse length / welding time (3), the user can
regulate for how many milliseconds the welding energy impacts upon the
work piece.
Depending on the angle at which the electrode is held in relation to the
work piece, the penetration depth and direction of flow (of molten metals),
can be influenced.
The penetration depth is at its greatest when the electrode is held
vertically to the work piece.