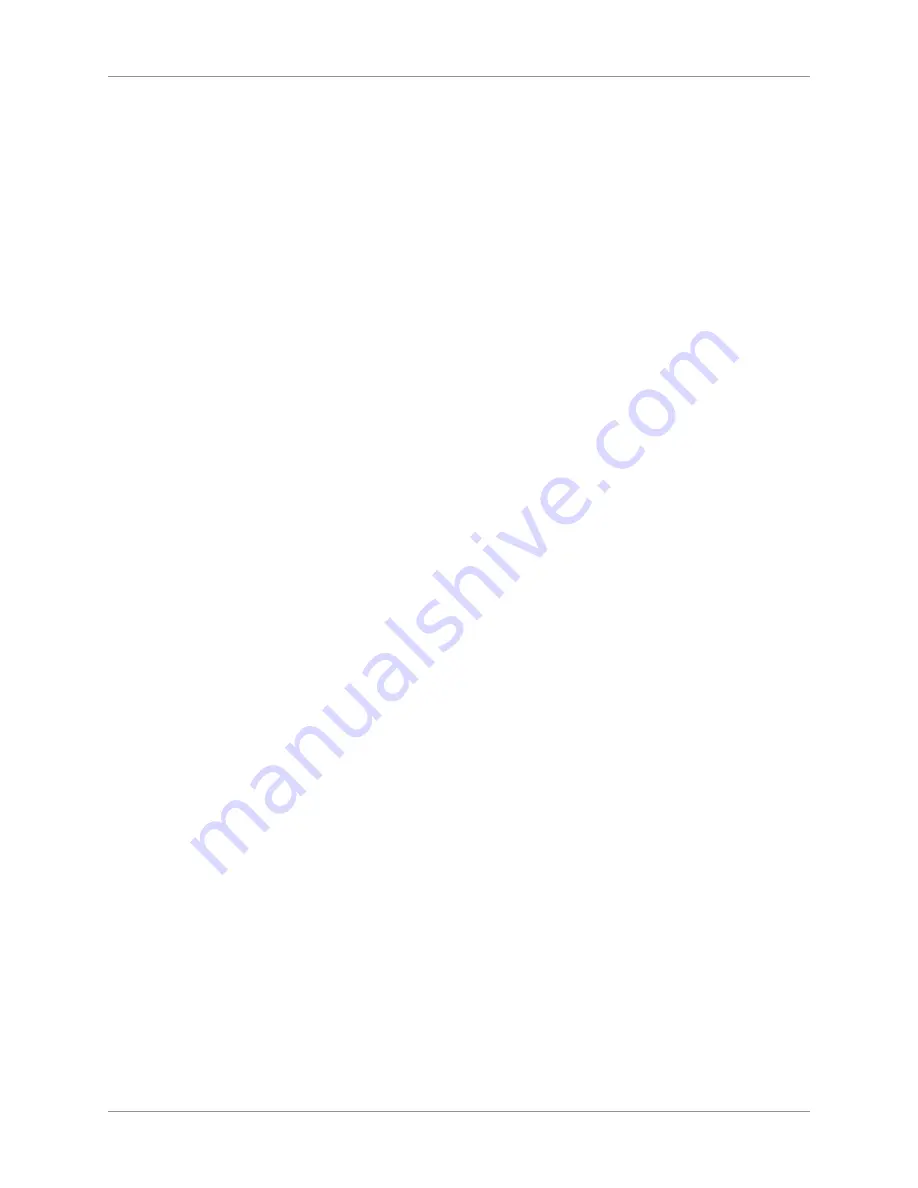
Activity Guide
Tech-Design by Lab-Volt
17
Automation & Robotics
Editing Programs
In the animation toolbar of the Program window, click on the Execute Step by Step button, and
6.
observe the action performed by the robot for each separate command:
Starting from the home position, the end effector is lowered to point B, then the gripper is fully
a.
opened.
The end effector grasps the film canister at point A, raises it to point B, and moves it in a straight
b.
path right over the metallic can at point C.
The film canister is lowered a certain distance within the can (point D), and then returned to point
c.
A through the reverse path (D>C>B>A).
The gripper is opened, and then the end effector is returned to the home position. A new cycle
d.
can begin.
Turn on the Power Supply of the robot and wait until the green LED at the rear of the robot base
7.
stops flashing and the red LED turns off.
In the Toolbar of the
8.
RoboCIM
main window, set the communication to Control.
Once the hard home positioning has been performed, run the program by steps: click several times
9.
on the Execute step by step button in the Program window.
Once the program is operational, you can run it continuously by clicking on the Run Continuously
10.
button and then the Execute button in the animation toolbar of the Program window.
When you are ready, stop the program by clicking on the Stop button.
11.
Program Editing
You will first modify the position of the metallic can.
Place
1.
RoboCIM
in the Simulation mode.
On the work surface, modify the position of the metallic can by placing it at (R5, C2).
2.
Now modify the position of the metallic can displayed in
3.
RoboCIM
to reflect the change made by
first selecting the Object tab. The Object window appears.
In the upper section of the Object window, click on the line of the metallic can to display the
4.
parameters of the object at the bottom of the window.
Set the metallic can position to (R5, C2) by changing the R value to “5” and the C value to “2”.
5.
You will now modify the coordinates of the points that need correction (points C and D), due to the
6.
change in the position of the metallic can.
Modifications for point C:
7.
Make sure the end effector is at the home position.
a.
Fully open the gripper.
b.
Double click on the name of point B in the Point Recorder panel to make the open gripper go
c.
right over the film canister.
Double click on point A to make the gripper ready to grasp the canister.
d.
Fully close the gripper to grasp the canister.
e.
Double click on point B to raise the canister over the work surface.
f.
Using the arrows of the robot’s articulations in the Motion window, move the canister over the
g.
approximate center of the metallic can.
Save Point C with the new required coordinates by doing the following:
h.
In the Point Recorder panel, click on the Record button.
i.
Enter the name of the point being modified, as recorded in the Point Recorder panel, using
ii.
the same case (enter C). Click OK. You will be asked if you want to replace the old point.
Click on Replace.
Содержание TECH-design E Series
Страница 1: ......
Страница 2: ......
Страница 3: ...Tech Design Automation Robotics Activity Guide eSeries Edition 1 37640 S0 ...
Страница 4: ......
Страница 8: ...Table of Contents Automation Robotics Activity Guide viii Tech Design by Lab Volt ...